Time to read: 7 min
The first step in designing a part is to determine what material it should be made out of. If you decide the part should be plastic, and it should be CNC machined, the selection does not simply stop there. There is a plethora of machinable plastic to choose from for plastic machining in 2022, each with its own combination of properties. In general, CNC machined plastic components make excellent prototypes and are readily available.
In this guide, I’m going to help you align your project needs with the right material for CNC plastic part machining. For the purposes of this article, I’m going to narrow the selection to several of the plastic materials offered by the China Manufacturing parts, Inc. platform for CNC machining. For more information on a broader selection of plastics for CNC machining, check out China Manufacturing parts’s full range of capabilities on fictiv.com under “Materials” in the navigation.
I’ll provide a material properties overview, advantages, disadvantages, and common uses for:
P.S. If you know your part should be plastic, but you’re not sure if it should be CNC machined or 3D printed, check out this article first.
ABS Plastic CNC Machining
Overview
ABS is a well-rounded general use plastic that is widely used. It offers high impact strength, toughness, and electrical resistance at a low price. It is also easy to finish, as it can be readily painted, glued, or welded together. ABS machining will leave a matte finish, although it can be somewhat shiny, depending on how it is machined. ABS CNC machining involves cutting or engraving using a CNC milling machine.
ABS CNC Machining Processes
- CNC Mill
- CNC Lathe
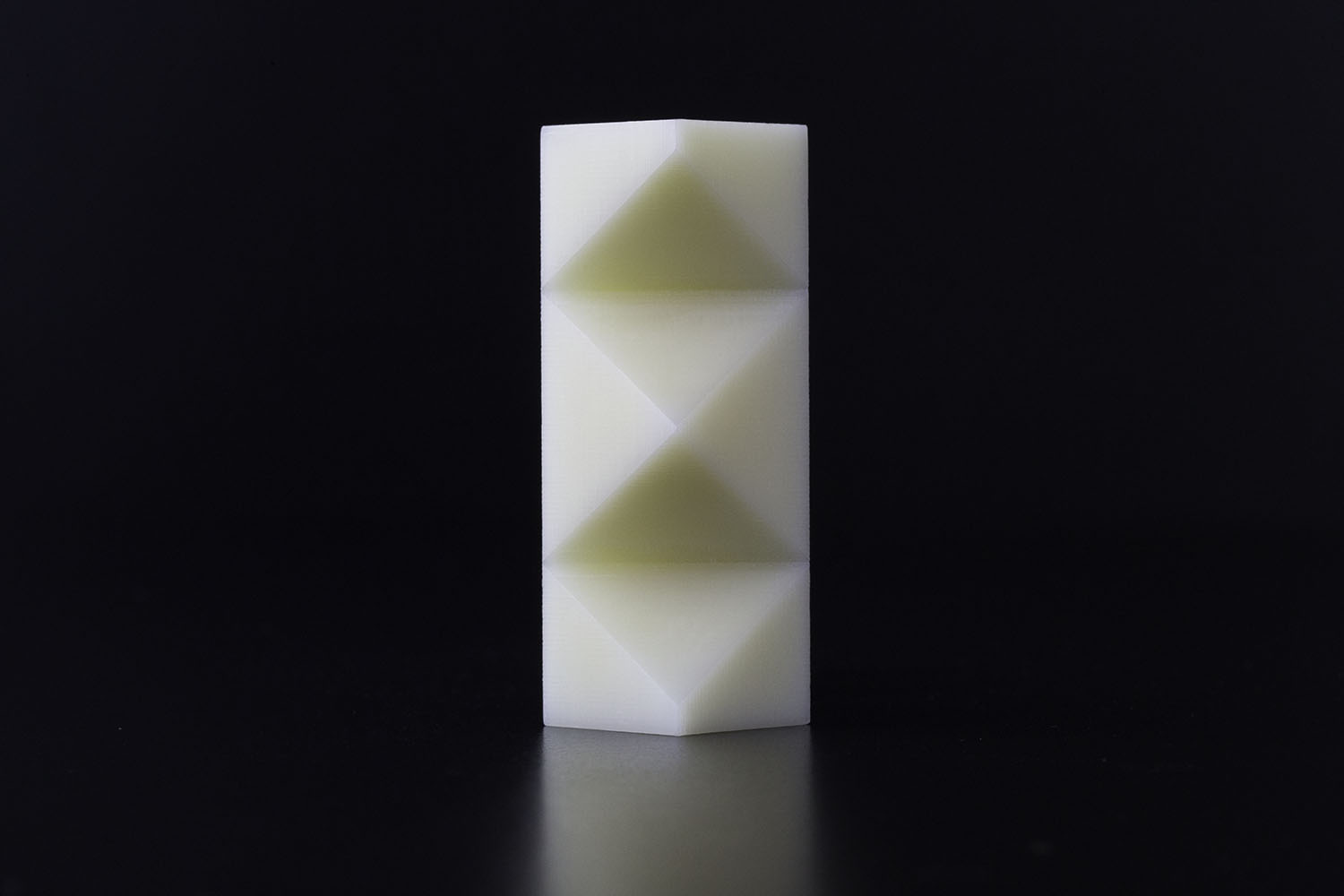
Benefits
ABS is an excellent choice for general purpose prototyping, pre-molding prototypes, parts that will receive impact and require toughness, or when low cost is desired.
Drawbacks
ABS does not have good abrasion or chemical resistance and will melt in acetone. It is also not an exceptionally strong plastic. Additionally, due to stricter environmental regulations on the West Coast of the U.S., large pieces of ABS are only manufactured in the Midwest and on the East Coast. This means that stock over two inches thick often takes a week to ship, leading to long production time for large ABS parts.
Common Applications
The most common applications of ABS are for pre-injection molding prototypes, make electronics enclosures, household appliances, and even the iconic Lego bricks.
Learn more in about ABS in the Capabilities Guide
Nylon CNC Machining
Overview
China Manufacturing parts offers Nylon 6/6 and glass-filled nylon. Nylon 6/6 is a strong and durable plastic which can be utilized for a wide variety of applications. It has relatively high chemical and heat resistance with rigidity necessary to retain its shape and strength to resist deformation under loading conditions. Glass filled nylon is also popular and provides a great CNC machining material to work with.
Nylon CNC Machining Processes
- CNC Mill
- CNC Lathe
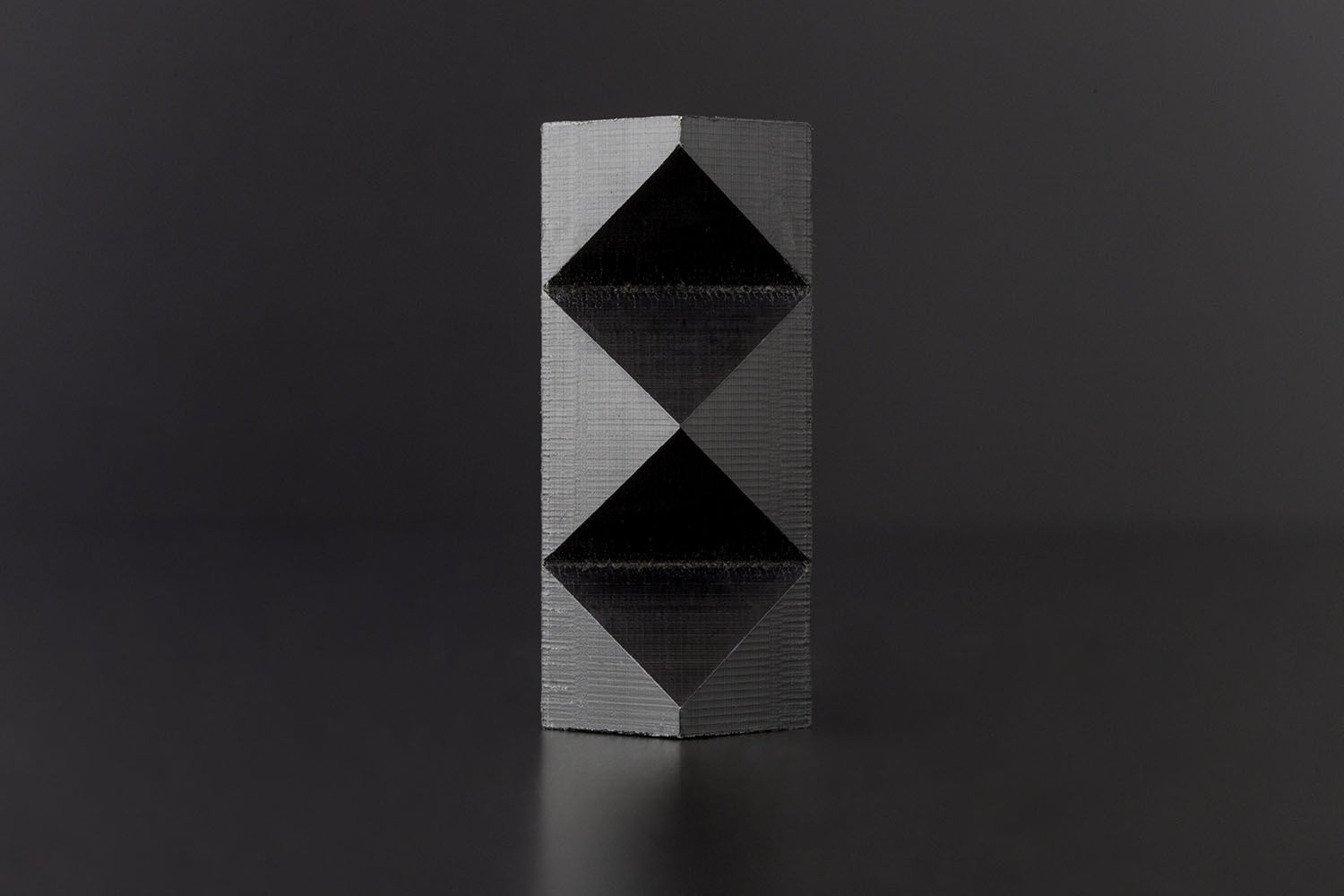
Benefits
Nylon has a high strength and rigidity that it maintains over a wide temperature range, good electrical insulation, and good chemical and wear resistance. Nylon 6/6 is a good choice for applications in which strong, durable parts are needed at a low cost.
Glass-filled nylon is rigid, strong, hard, tough and dimensionally stable.
Drawbacks
Nylon 6/6 will absorb moisture, causing it to swell and lose some dimensional accuracy. It can also warp if there is a large amount of asymmetric material removal during machining, due to internal stresses inherent in the material.
Common Applications
Nylon is most commonly found in medical devices, circuit board mounting hardware, electrical insulation, automobile engine compartment components, and aerospace components. In many of these applications it is used as an economical alternative to metals.
Learn more in about nylon in the Capabilities Guide
Acrylic
Overview
Acrylic, which is also known by trade names Plexiglass or Luctie, has a chemical composition known as PMMA (Poly Methyl MethAcrylate) plastic. It is tough, with decent impact strength and scratch resistance, and can be easily glued using acrylic cement.
Acrylic CNC Machining Processes
- CNC Mill
- CNC Lathe
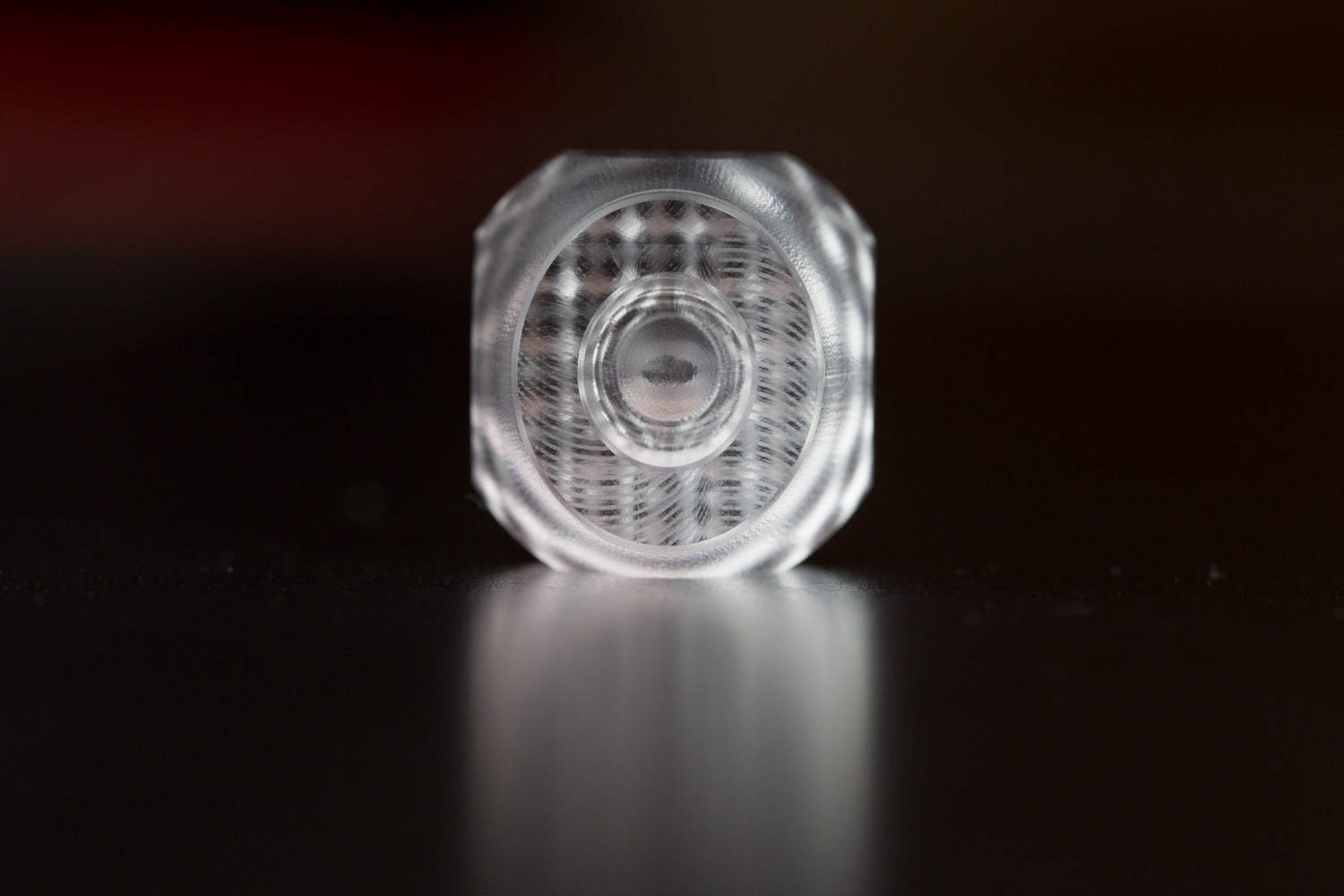
Benefits
It is well suited for any applications that require optical transparency or translucence, or as a less durable but cheaper alternative to polycarbonate. Its scratch resistance also makes it optimal for areas with slight abrasive environments.
Drawbacks
However, acrylic is a brittle plastic and has a tendency to crack or shatter, rather than stretching as a ductile material would. Attention should be paid to the wall thickness in acrylic components as thinner walls are more brittle.
Any machined surfaces on a piece of acrylic will lose their transparency and take on a frosted, translucent appearance. Because of this, it is usually a good idea to note if an acrylic part should be left at stock thickness to preserve transparency or not. If transparency is needed on a machined surface, it can be polished as an additional post processing step.
Common Applications
As-machined, acrylic is transparent and is most commonly used as a lightweight substitute for glass or for light pipes. Other common uses include automobile light components, light tubes, tanks, panels and components for optical engineering.
Learn more in the Capabilities Guide
Delrin/POM CNC Machining
Overview
Delrin is a trademarked name for class of semi-crystalline thermoplastic acetal resin aka the abbreviation POM which stands for polyoxymethylene. It has a slippery, low friction surface, excellent dimensional stability, and high stiffness. There are many classifications of this acetal resin, including:
- Standard
- Toughened
- Low friction
- Glass-filled/reinforced
- UV-stabilized
Fictiv’s material selection for plastic CNC machined components also includes Delrin with glass fibers and Delrin AF. Delrin with added glass fibers is also excellent for superior stiffness and dimensional stability along with a high creep resistance. Delrin AF, another variation, with increased coefficient of friction, providing a self-lubrication, has excellent wear resistance, toughness, and strength.
Delrin/POM CNC Machining Processes
- CNC Mill
- CNC Lathe
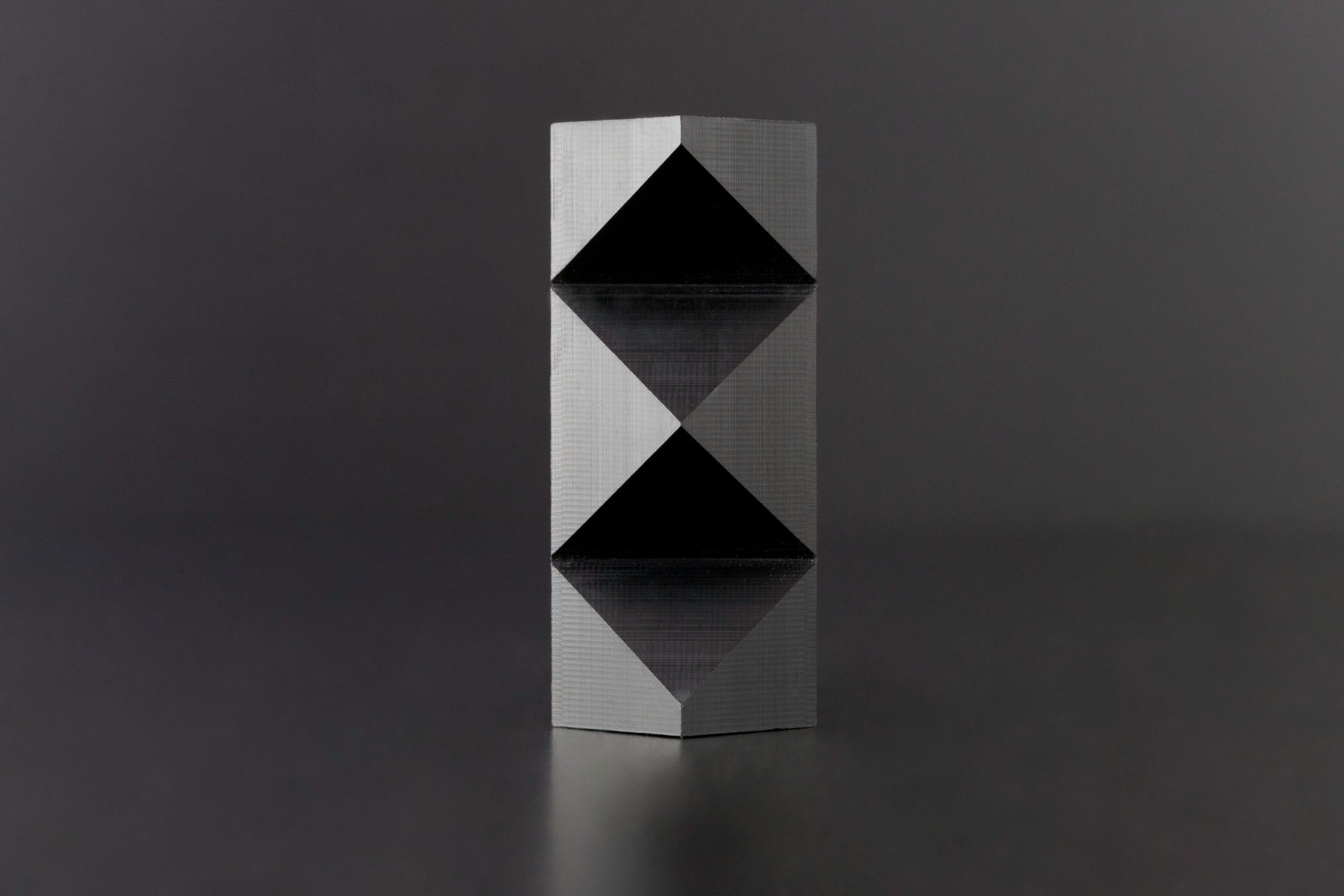
Benefits
Delrin/POM is a good plastic for these or any other applications that will experience lots of friction, require tight tolerances, or need a high stiffness material. It has been used in commercial markets for decades due to its reliability and durability. It also has excellent impact, chemical, moisture and fatigue resistance. It is also easy to CNC machine Delrin/POM.
Because of its high stiffness and rigidity, Delrin is an excellent choice for CNC plastic machining parts that require dimensional accuracy and tight tolerances.
Drawbacks
The downside to Delrin’s slippery, wear resistant surface is that it’s very hard to glue. The material also has internal stresses that make it prone to warping in areas that are thin or have large amounts of asymmetric material removal. In addition, heating Delrin/POM in excess of the maximum capability can result in dangerous off gassing.
Common Applications
Delrin is commonly used in gears, bearings, bushings, and fasteners, or to make jigs and fixtures for assembly, or even automotive, construction, and electronics components.
Learn more in the Capabilities Guide
HDPE CNC Machining
Overview
HDPE stands for high density polyethylene. It is naturally opaque, due to its crystalline structure, with a waxy finish but is also commercially available in a black dyed finish.
HDPE CNC Machining Processes
- CNC Mill
- CNC Lathe
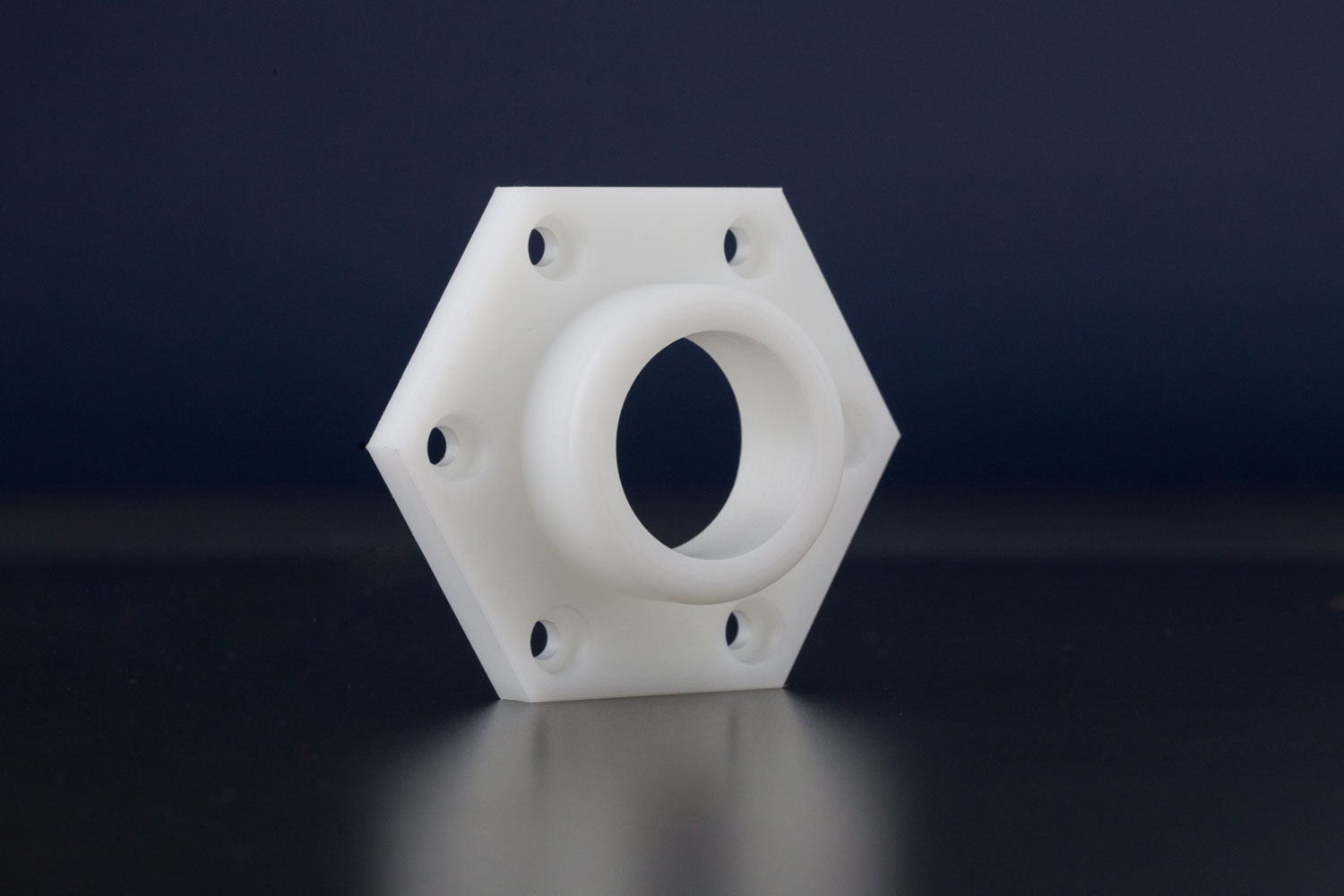
Benefits
Despite its name, HDPE is the least dense plastic China Manufacturing parts, Inc. offers, and it also has excellent chemical resistance, electrical insulation, and a slippery surface. It offers a low coefficient of friction and good low temperature impact resistance. It is an overall affordable, durable choice for CNC machined plastic parts.
Drawbacks
HDPE’s main disadvantage is its poor strength, particularly in tension and flexing. Due to this, it is susceptible to stress cracking .
Common Applications
HDPE is often used in fluid applications, such as fuel tanks, plastic bottles, and fluid flow pipes. It is well suited for making plugs and seals, due to its chemical resistance and slipperiness, but is also a good choice for weight-sensitive or electrically sensitive applications.
Learn more in the Capabilities Guide
Polycarbonate CNC Machining
Overview
Polycarbonate, aka PC, is the most durable plastic offered by China Manufacturing parts. PC is a transparent thermoplastic. It is also one of the most commonly CNC machined plastics and one of the most commonly recycled plastics globally. It has a natural transparent milky-blue appearance but is commercially available in a black hue. Both the black and milky-blue tints are naturally glossy.
China Manufacturing parts offers machine-grade polycarbonate which provides the transparency and high impact strength needed for structural applications.
Polycarbonate CNC Machining Processes
- CNC Mill
- CNC Lathe
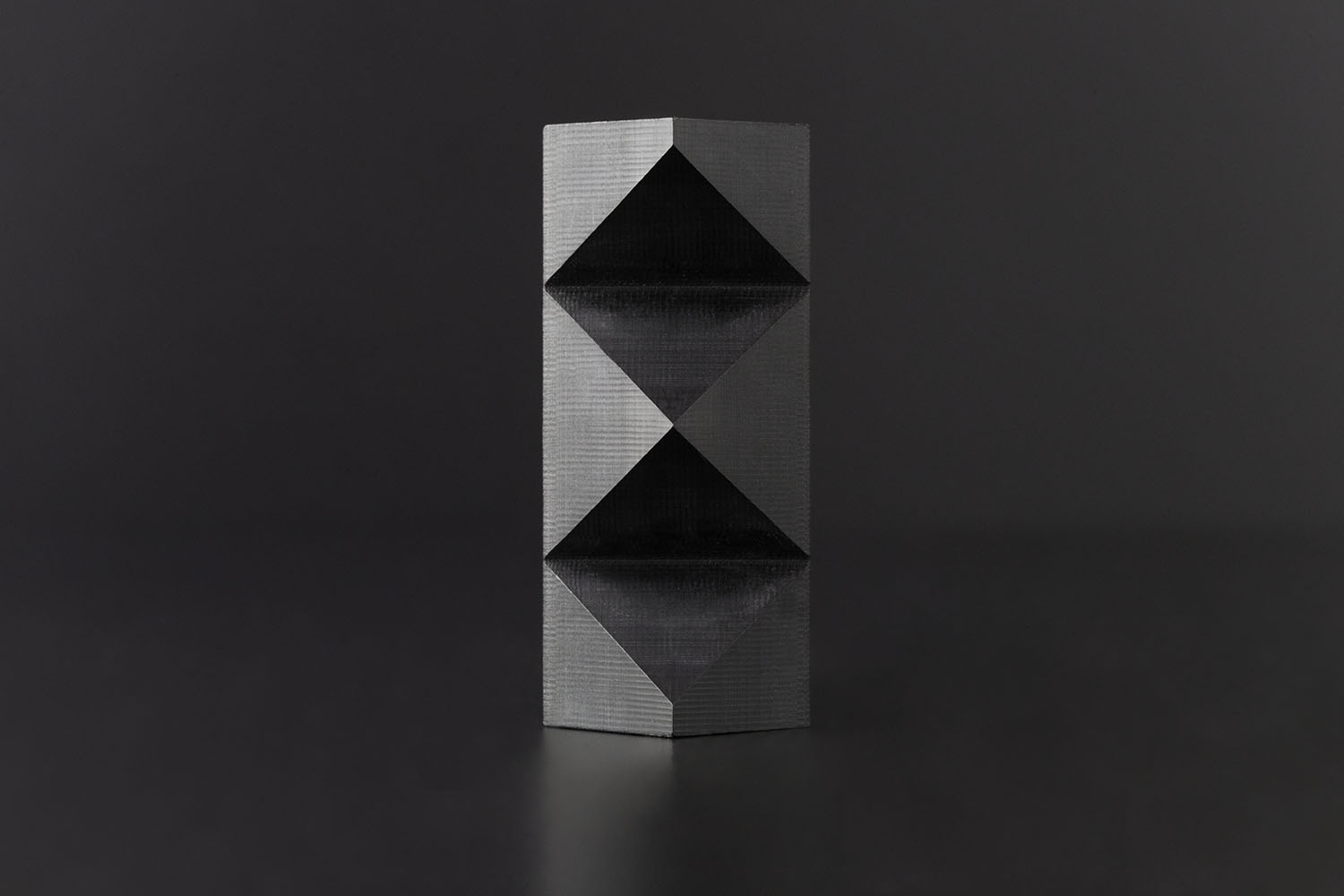
Benefits
Polycarbonate has a very high impact resistance and stiffness, and remains functional over a wide range of temperatures. It is also optically semi-transparent, although it can be dyed black if opaqueness is needed. Polycarbonate is best suited for applications in which a very tough or very strong plastic is needed, or where optical transparency is desired. Because of this, polycarbonate is one of the most used, and most recycled, plastics.
Polycarbonate is often utilized over glass because it is 250X more impact resistant and over acrylic because it has a higher resilience.
Drawbacks
Pure polycarbonate does not have good wear resistance and is prone to scratches. Anti-scratch coatings and vapor polishing can be added as a post processing step to improve wear resistance or optical clarity, if needed. It is also not readily available in pieces over two inches thick, which limits the size of parts that can be made of polycarbonate.
Common Applications
Polycarbonate’s durability and transparency mean it is used to make optical disks, safety glasses, light pipes, CDs, DVDs, mobile phones, and even bulletproof glass.
Learn more in the Capabilities Guide
Main Takeaways
Hopefully, this guide has provided insight into which plastic is best suited to your application. For more information on additional CNC materials and CNC machining services in general, visit China Manufacturing parts’s website.
- Plastic is relatively straightforward to CNC machine.
- Polycarbonate and ABS are commonly CNC machined plastics.
- ABS is one of the most cost-effective and simplest materials to CNC machine.
- A CNC mill for plastic machining is a good choice but you should be cognizant of the mill speed as higher speeds will warp or melt some plastic materials.
Ready to learn more about China Manufacturing parts’s innovative platform which allows you to easily upload CNC plastic machined component designs, receive DFM feedback, and pairs you with a Manufacturing Partner to provide optimized quality, delivery and a human touch that is unparalleled in the industry? Submit a design for a quote today: