Time to read: 2 min
In prototyping automotive parts, it’s common for NVH (noise, vibration, and harshness) to be placed on the back burner in the early product design phases, as there are often bigger challenges at play (like not breaking parts). NVH studies, often difficult and elusive, are not exactly a low-hanging fruit in the prototype phase.
However, a gram of prevention is worth a kilogram (nay, a slug!) of cure. Procrastination leads to costly design tear-ups and logistical havoc and having multiple different prototype pedigrees released to the customer makes program tracking exponentially more difficult. Valuable vehicle testing data is lost as old designs are now obsolete and mostly useless for validation.
3D printing is an invaluable tool in early stage prototyping for NVH—here are a few tips to help you get the most out of this technology.
1. Print Rapid Iterations of Geometric and Material Tweaks
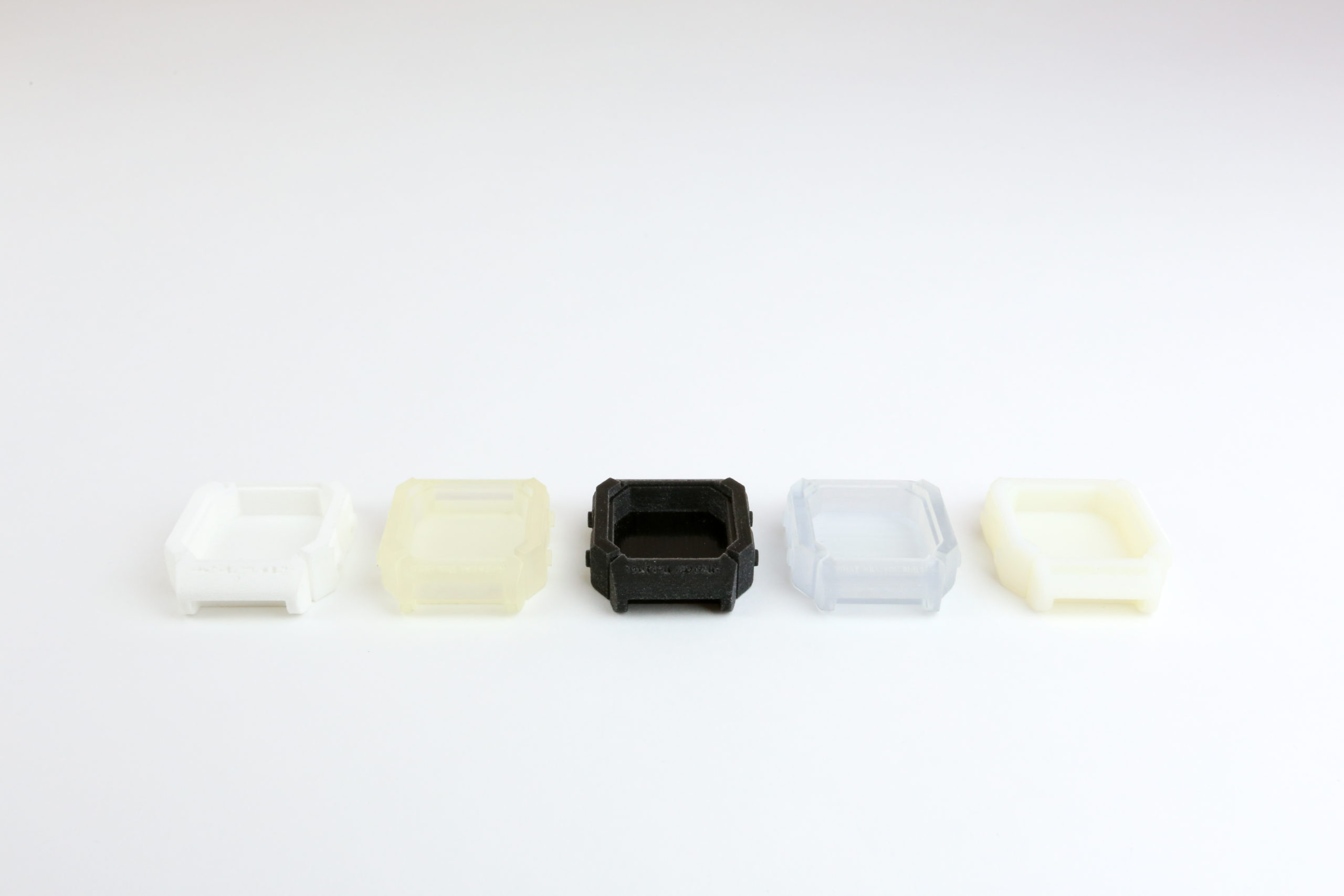
The speed of 3D printing is extremely useful for experimentation (NVH or otherwise) in the prototype phase, as geometric and material tweaks (such as rubber stiffness) are trivially easy, whereas the cost to make changes to casting molds or forgings is time-consuming and costly.
This speed is especially useful for more challenging designs that have a high degree of uncertainty, and therefore benefit from physical experimentation. You can check out the different 3D printing material specs here.
2. Design Transparent Enclosures
Also useful in the prototyping phase is the 3D printed transparent housing, which is a very helpful tool to gain insight (literally) into what’s happening inside an enclosed product, such as a gearbox. While commonly use for lube flow observation, a clear housing is also invaluable for observing physical mechanisms which are otherwise shrouded in darkness. A clear housing makes the understanding of a click or clunk as easy as looking through a window.
As an example, you can see the aesthetic difference between different clear 3D printing materials in our post about prototyping light pipes.
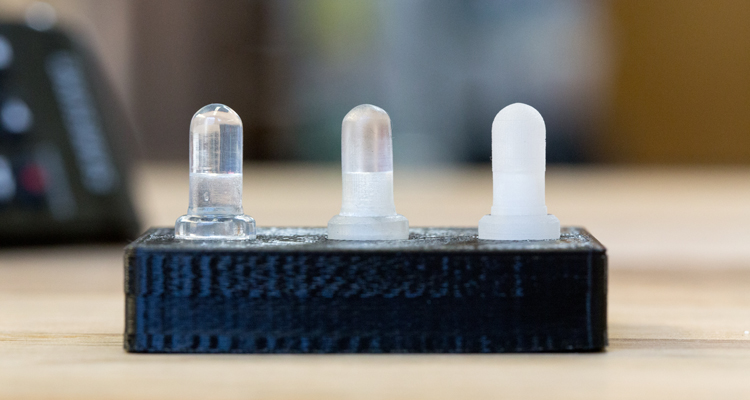
3. Prototype Temperature Control with 3D Printed Housings
Without going too hogwild, consider this idea: Temperature can play a role in NVH performance. 3D printing allows you to create a prototype housing with built-in cooling channels in order to run a system (such as a gearbox or transmission) at high power without the added variables associated with temperature increase (decrease in lubrication viscosity, change in rubber stiffness, etc.).
Choose the Right 3D Printing Material
There are many different 3D printing materials available. To find the right material for your prototypes, use this material decision tree to consider the most important features you’re looking for:
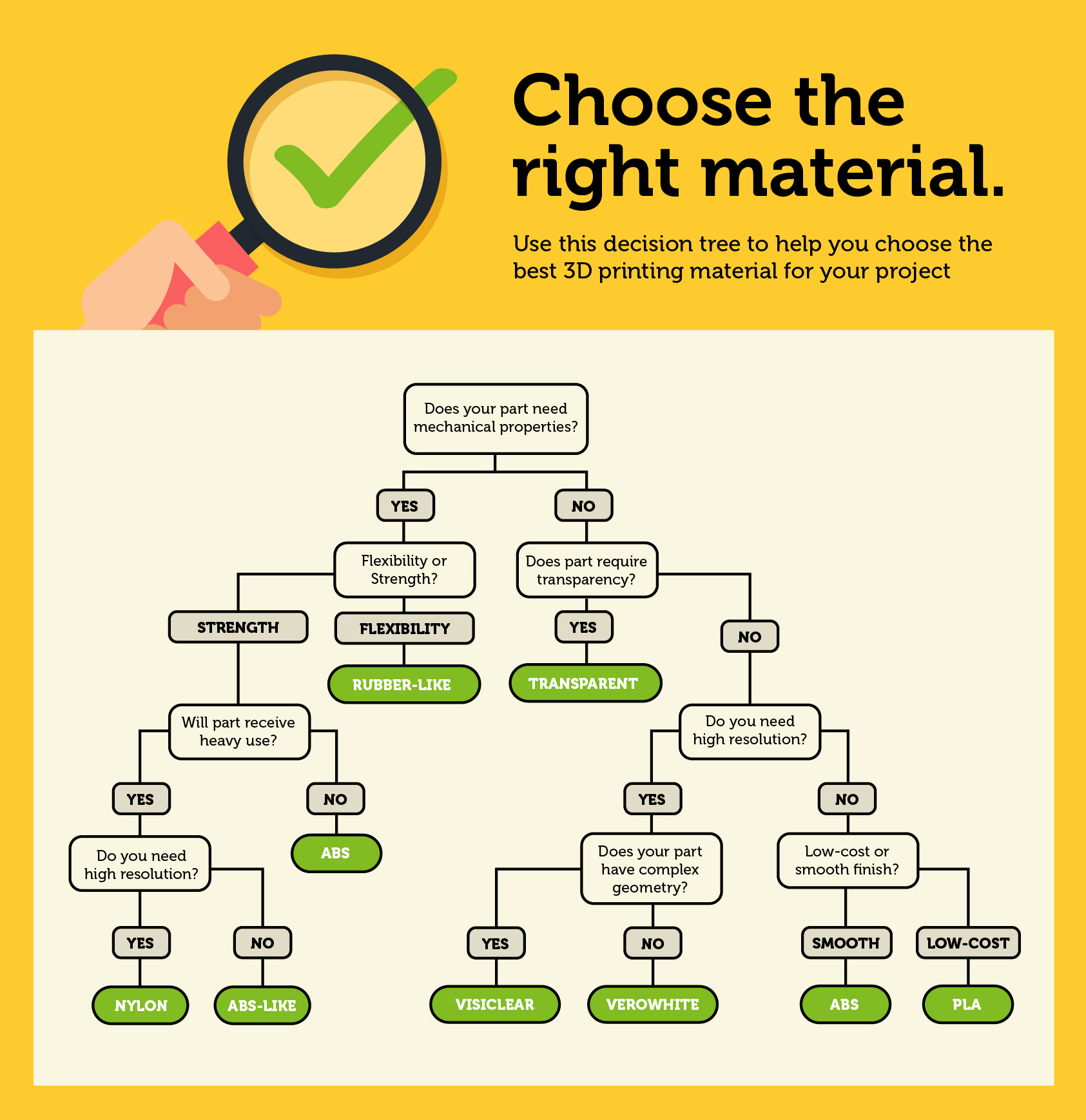
Vroom
There are a lot of great prototyping tools available to the 21st century engineer, 3D printing included. To get instant quotes and fast, high quality 3D prototypes, hop on over to fictiv.com to upload your parts and get a free design review from one of our prototyping engineers.