Time to read: 6 min
The Product Requirements Document (PRD aka Product Requirement Document) is a familiar term to most engineers. Typically, we get the PRD from a product manager; it tells us what to build but not how to build it. But let’s face it, it’s probably better that way. Engineers hate being told how to implement an idea — that’s the fun part! An Engineering Requirements Document (ERD) specifies what product will be built in order to fulfill the Product Requirements Document’s specifications.
The ERD should provide clarity on the goal or purpose of the new product and should fulfill all relevant specification requirements. The effort of writing this document is usually led by a system design or engineering lead, but it’s essential that engineers from all disciplines (mechanical, electrical, firmware) contribute.
An ERD is useful for the development process of all types of manufactured components or assemblies, including those manufactured utilizing CNC machining, injection molding, urethane casting, and 3D printing processes.
Why Should I Write an ERD?
An Engineering Requirements Document serves a few purposes:
An ERD is an Excellent Project Planning/Management Tool
It helps to break down a large project into smaller tasks, so you can then delegate the tasks to team members, giving everyone a clear scope of responsibility. Consider it an excellent project planning tool, as well as a tool to ensure all requirements are met. In addition, the breakdown of larger projects allows for simple outsourcing to manufacturing partners if internal resources are constrained.
An ERD Allows for Cross-Functional Collaboration
Writing an ERD can reduce miscommunication between product, design, and engineering teams. It enables a valuable and performance-enhancing, cross-functional approach, from a single source of truth. The ERD is the output of interpreting the PRD, any required engineering specification documents, industry specification requirements, and determining additional assumptions that must be made during the writing process. After a draft has been written, the product, design, engineering, and manufacturing teams can all reference the ERD and check those assumptions, ensuring product and design intent are sufficiently captured.
An ERD is a First Step in Determining Testing Requirements
Since drafting an ERD involves reviewing and analyzing all product conformity requirements, the draft is the first step in establishing a sound test plan. Any performance requirements listed in the ERD need corresponding tests to verify them. After all, why require something if it cannot –or will not– be tested?
Simple Approach to Getting Started with an ERD
Follow this 3-step approach for drafting your ERD:
1. Translate the Features and Performance Requirements Described in the PRD to Engineering Specifications
Example product: a portable, wireless speaker |
Testing: The PRD calls for 7 days of battery life testing |
This spec needs to be translated into battery capacity (in amp-hours). To do this, the electrical engineers probably need to make a power budget and ask questions like: “What is the active and inactive/standby time that make up 7 days?” Both engineering and product need to agree on that answer.
Based on charging or replacement requirements, you can narrow down the type of battery you’d like to use. With this additional constraint, battery capacity translates well into standard sizes or volume (in the case of Li-Po) – useful information for mechanical engineers. The requirement should determine how the testing is performed, as well as how the product is designed – i.e. the engineering specification related to battery performance.
PRD Instruction: speakers should be designed for heavy bass output |
The PRD also says that the speakers should be bass-heavy. To an audio engineer, this translates to a set of frequency response graphs with a certain shape. These graphs will be the engineering specification. The DAC (digital-analog converter) and mechanical enclosure both have an impact on the frequency response, and they will be designed to meet the audio specification.
2. Identify Cross-Functional Dependencies
As we just saw, achieving each product feature involves the collaboration of multiple disciplines. Thus, the ERD should document how mechanical and electrical components work together.
PRD Instruction: speakers should be designed with buttons to control volume |
Using our example speaker again, there are buttons to control volume. A mechanical engineer will design the physical buttons, choose the switches underneath, decide how to mount the switch PCB assemblies (PCBAs), and give an electrical engineer the printed circuit board (PCB) footprint and switch pad locations so they can do the schematics and layout. The ERD should capture the division of responsibility for each feature of the product and help to draft the engineering specification for each of the electro-mechanical components or interfaces.
3. Mechanical Engineering Special: Translate the Industrial Design Spec into ME Language
Mechanical or product design engineers not only need to fulfill the PRD’s requests, but also make the industrial designers happy. Tough job indeed!
Unlisted Requirement of ERD: ensure industrial/manufacturing design specifications are conveyed correctly |
The industrial design spec usually comes in the form of a surface CAD model and a color, material, finish (CMF) document. The surface model often needs to be converted to a solid CAD model, and the CMF document needs to be translated into a mechanical engineering spec.
PRD Instruction: speaker visual design and materials must be determined |
Color
Has the industrial designer called out a Pantone number? A Pantone plastic number is great, but some plastics vendors don’t own the $2000 plastics catalog, so you may still have to provide the sample chip. Usually, it’s sufficient to have a Pantone Coated (C) number and do any fine-tuning at the time of injection.
White is notoriously hard to get right, and referencing a Pantone C number may not be suitable for communicating exactly what kind of white you want. The easiest thing to do here is to provide an actual plastic swatch — it doesn’t have to be Pantone, just an example from another product you like.
Also, note that sometimes in-mold coloring won’t achieve the aesthetic quality required by industrial designers. It’s up to the mechanical engineer to determine whether painting is more suitable.
If you’re looking for an injection molding manufacturing partner, look no further than China Manufacturing parts. Our intelligent platform allows for simple, streamlined quoting and we have injection molding experts available for any size project, from small to enterprise. Check out our Gantt chart for injection molding for help project planning from your ERD.
Material
If the industrial designer has called out plastic, it’s up to you, the mechanical engineer, to choose the resin. The durability and performance characteristics of the PRD will inform the choice.
If metal shows up in the design, it’s of utmost importance to understand the industrial designer’s intentions. Sometimes we can get away with metallic vapor deposition over plastic to achieve a metal appearance – or use sheet metal trim over plastic structure. However, if solid metal components are called for (often to suggest higher quality), we have to determine whether to use casting, CNC machining, or metal injection molding to produce the parts.
Finish
The texture of the product enclosure can be achieved in a multitude of ways. Specific painting, blasting, brushing, and polishing techniques can be worked out with the contract manufacturer at a later stage. If the plastic parts require texturing, in-mold is a good option. You, the engineer, can ask the industrial designer to choose a swatch out of a Mold-tech or Yick Sang texture catalog and give this number to the mold maker.
PRD to ERD Translation Table
The table below examples of translating PRD requirements into ERD requirements.
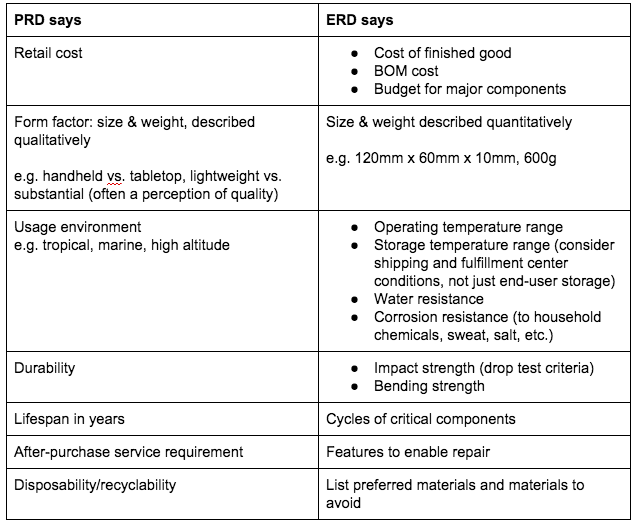
Main Takeaways
Writing an ERD is a great first step for kicking off the engineering process of any product, especially if there are a lot of moving pieces – and when many engineers or a cross-functional team needs to work together.
An ERD is a living document in the early days of product development. You can begin by writing a high-level ERD consisting of requirements and fill in the details as more decisions are made, such as what material to use.
When you’re ready to engage manufacturers, you’ll thank yourself for having written a great ERD. Just imagine how impressed your manufacturing partner will be when you present the PRD and the ERD as you request a quote.
After all, the better they can understand your product, the better they’ll build it.
And we should know. China Manufacturing parts, Inc. is the ultimate manufacturing partner, providing an intelligent platform to upload your 3D models or 2D drawings for an instant quote and DFM feedback. We’re experts in CNC Machining, Injection Molding, Urethane Casting, and 3D Printing.
Ready for a quote? Log into China Manufacturing parts or create an account to upload your design files and get started in minutes.