Time to read: 9 min
In the world of plastics, there are a lot of different options for a designer to choose from. There are so many plastic materials, in fact, that the process of selecting the proper 3D printing plastics for prototyping and subsequent manufacturing plastics for production may seem intimidating. This article seeks to clarify the main types of plastic materials available, as well as applications for each.
Overview: Different Types of Plastic Materials
Plastics are a synthetic material used for a multitude of different applications. They are commonly made of petrochemicals, but can also be made of some natural components. Some common plastics include Nylon, Acetal, and High Density Polyethylene.
While the two main types of plastics are thermoplastics and thermosets, this article will focus on grouping plastics by their mechanical behavior, as detailed below:
Rigid Plastics
In short, these are the plastics that we use for items such as electronics enclosures, football helmets, power tool bodies, tape dispensers, and cutting boards. They are substantially less flexible than elastomers but much stronger. They are commonly rated on the Shore D scale, which will be detailed below. Some common rigid plastics are ABS, Nylon, HDPE, and PolyCarbonate.
Elastomers
Also known as rubbers, elastomers are a class of polymers that are characterized by low elastic modulus and high strain to failure. In other words, they are “stretchy”. Some common elastomers are silicone rubber, HNBR, Nitrile, Buna-N, and Urethane rubber. The image below is of a part made from a liquid silicone rubber compound.
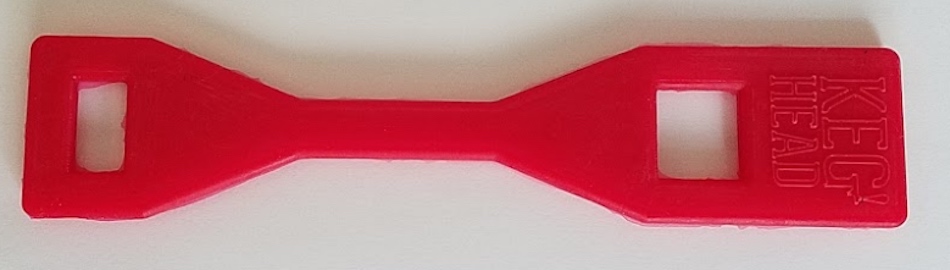
More specifically, the component is a platinum catalyzed silicone rubber that is cured at room temperature under light pressure.
Fiber Reinforced Plastics
These are plastics that have reinforcing fibers dispersed within the plastic to add rigidity, strength, and wear resistance. Common examples of this include fiberglass and carbon fiber layups. It’s also somewhat common to have chopped fiber in injection molded plastics. The image below shows a pocket knife with handles that have a nylon plastic with a glass fiber fill.
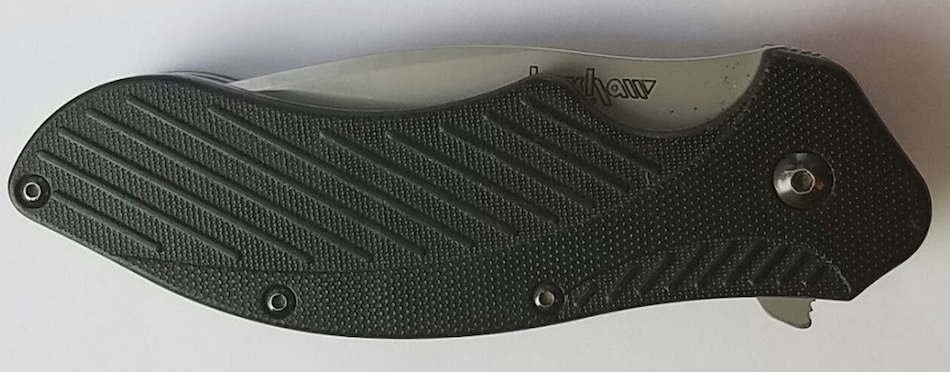
This knife has been carried around daily for well over two years, and it shows very little wear. This is largely thanks to the mechanical properties of glass-filled plastics.
Some SLS printed parts may have glass filled nylon powder, which produces parts with a much higher stiffness than standard nylon. Picking such an option would be a good choice to replicate the handle above.
Modified Plastics with Additives
It’s also common to incorporate additives into a base plastic to produce a variety of desirable characteristics. Some common additives are: antimicrobials, antistatics, plasticizers, pigments, UV stabilizers, fillers, and flame retardants. There are more options, so if you have a specialized need beyond the common additives, I recommend contacting a plastics material vendor.
Important Mechanical Properties to Consider
Regardless of the type of plastic, there are some basic material properties that need to be understood for the optimum material selection.
Yield Strength
This is the maximum stress that can be applied to the material before the material deforms permanently. My article here goes into much more detail on this topic. The important thing to know in almost all cases is that you want the material stresses to remain below the yield strength of the material during use.
The image below details a plastic component in its original state, and again after it has been loaded past its yield strength.
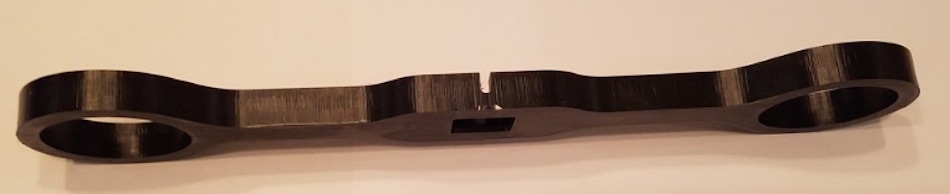
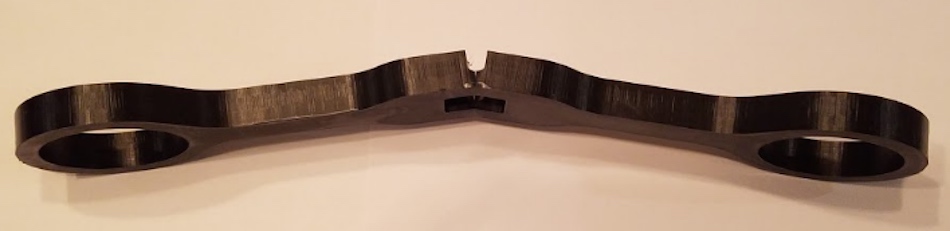
As we can see, the part is now permanently deformed, due to excessive force. We could not expect this part to perform as it was designed because we have exceeded the yield strength of the material.
Ultimate Strength
Ultimate strength is much like yield strength, except it’s the stress at which the part fails completely. The image below shows the same component from above that has been loaded even further and completely separated.
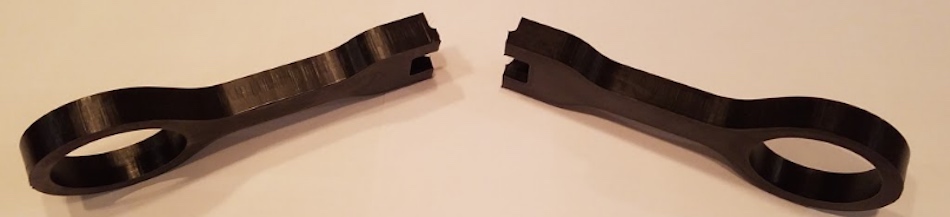
Youngs Modulus
Also known as elastic modulus, this is the amount that a material will “stretch” when a load is applied. If we remain below the yield strength, the part will return to its original shape after the load is removed. More details of this concept are detailed in the article mentioned above.
The image below shows a fishing lure that is made of an elastomer in two conditions: the original state and stretched.
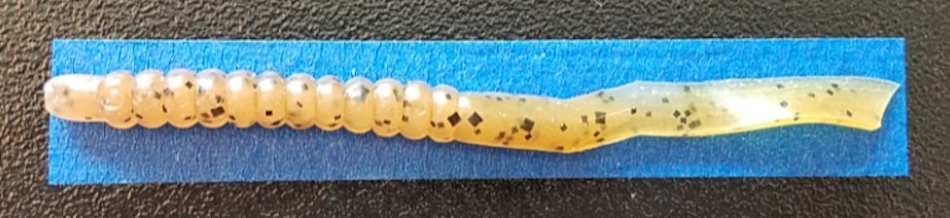

While the material has stretched quite far, it will return to the original state when the load is removed. Elastomers are also commonly used for gaskets and seals. The image below shows an elastomeric ring gasket on the bottom side of the lid for my pressure chamber.
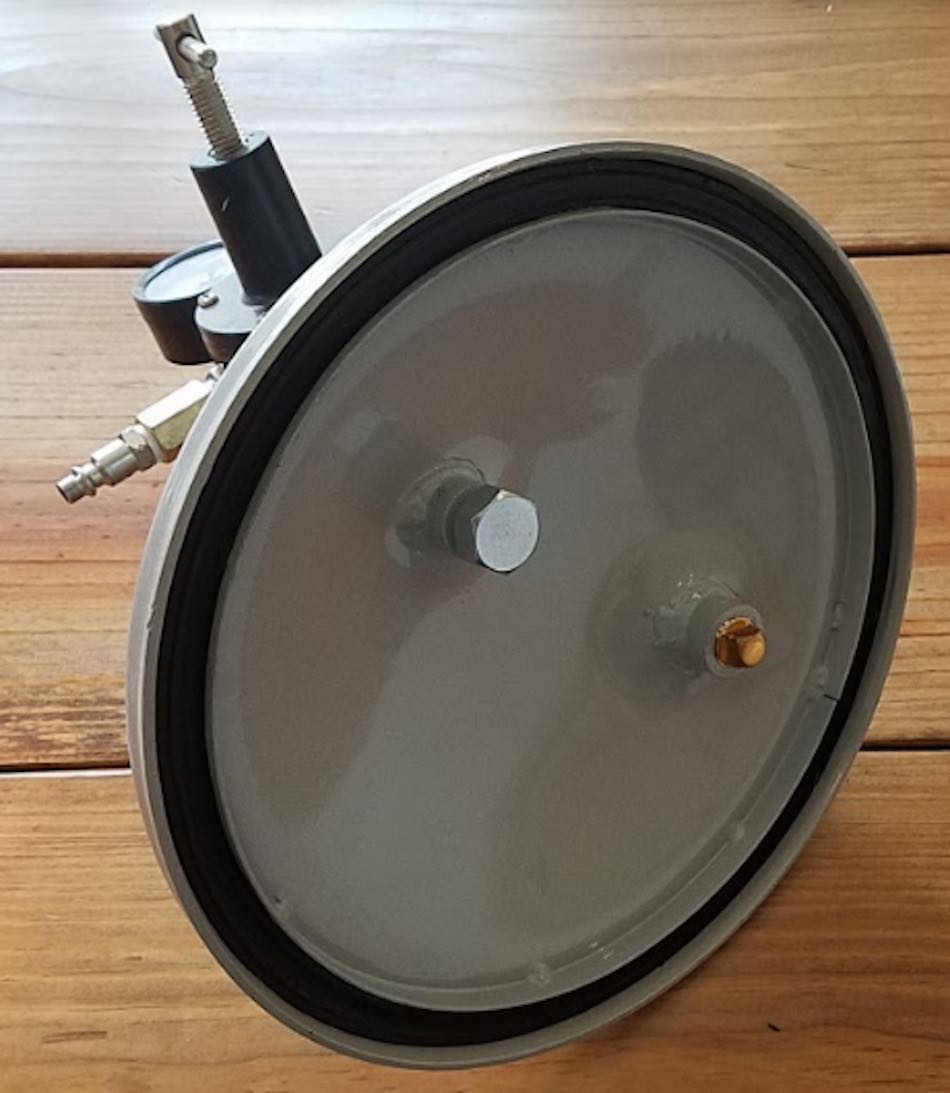
This elastomer holds 60 psi while the chamber remains pressurized and prevents the captive air from leaking off. Gaskets similar to this can also be found on blenders, travel coffee mugs, and many other items.
Durometer
Different plastics and rubbers have different hardness values that are known as the material’s durometer. More specifically for this article, the shore hardness scale is typically used. Within shore hardness, there are three classifications: 00, A, and D, in order of increasing hardness. A pencil eraser would have a hardness of around 40 on the Shore A scale, while a plastic hard hat would be closer to 80 on the Shore D scale.
Elongation
Elongation describes the amount that a material is able to stretch. If the stresses remain below the yield point, the component returns to the original shape in most cases. If the stresses exceed the yield point but are below the ultimate strength of the material, the part will deform but remain intact. If the stresses exceed the ultimate strength, the part will separate as shown above.
Plastics and elastomers typically have a higher elongation when compared with most other materials, with the former having a high elongation in the elastic region. Standard plastics can’t stretch quite as far as an elastomer, but they are also commonly characterized by a high elongation after plastic deformation.
Coefficient of Friction
The coefficient of friction is a term that describes the ratio of the force to move and object perpendicular to normal force. In more simple terms, it describes how well an object slides on the material. This is important for items that will be used in sliding or dynamic contact applications. Some bearings are made of a Teflon (PTFE) material because of the low coefficient of friction.
Additional Material Properties of Importance
Outside of the common list of mechanical properties of materials, there are some additional properties of plastics that may be important based on your intended application. Those properties are as follows:
- Biocompatibility – Not all plastics are safe for use in biomedical applications, but those that can be are considered biocompatible. These are plastics that can be used in the body without adverse reaction. Some common biocompatible plastics are: PEEK, PE, PVC (Medical Grades), PP, PTFE, and a few others. Most of those materials would be injection molded, extruded or some other method of thermoforming. There are, however, grades of 3D printed biomaterials, such as MED610 and ULTEM CG, that can be procured in the certified state. Nylon and VisiClear are also suitable for some applications…a broader guide can be found in this post. Remember that even if a particular material is capable of being biocompatible, other controls must be in place to certify that they are. This is the reason why stratasys offers ULTEM 1010 in both the certified and uncertified options.
- Antimicrobial – A material that is antimicrobial inhibits the ability of a microorganism to grow or may even destroy them. Typically, it is a surface treatment of a plastic that is grafted onto the surface through specialized processes. It can also be driven by the surface roughness and ability to shed water. It’s rare that you will find an antimicrobial 3D printed surface, but manufactured plastics such as HDPE, PETE, PP, and SAN are common options to treat. You have likely seen antimicrobial HDPE cutting boards at some point in your life.
- Manufacturability and Process ability – This is a broad category that simply describes the ability of a plastic to be manufactured through different processes. For example, PEEK can be injection molded, extruded, CNC cut, pultruded, and more. Liquid Silicone Rubber will be limited mostly to forms of molding. Common thermoplastics can typically be manufactured through more methods than thermosets, but not always.
- Temperature Resistance – Plastics have a limited range of operating temperatures, especially when compared to metals or ceramics. For this reason, it’s important to select a plastic that will survive your operating conditions. As an example, 3D printed ULTEM and PPS are some high-temperature options.
- Optical Properties – The ability to transmit light or block light may be needed for some components. For light pipes, you will want a transparent material such as VeroClear or Acura 60. For the housing that holds the light pipes, you will most likely want to prevent light leakage or transmission. There is a good article on how to design light pipes here.
- Dimensional Stability and moisture absorption – Some plastics are more dimensionally stable than others, due to their mechanical stability. This can be driven by a few factors, one of the common ones being moisture absorption. Plastics such as urethanes and nylons will absorb a fair amount of moisture, and the part will tend to grow. This also happens with ABS, which causes issues with blistering when vacuum-forming sheets. When it comes to 3D printing, it’s also important to understand the dimensional limitations of your material as manufactured by the 3D printer. Some materials such as PLA cannot achieve the level of dimensional accuracy that a material such as VeroWhite/Black can.
- Food Safe – Similar to biocompatibility, food safety is a term used to describe a plastic that is safe for use to store or contain food, and it is dependent on the material certification. As an example, HDPE is commonly used to store food items such as a milk jug, but not all HDPE is deemed food safe.
Design Guidelines: 3D Printing Materials vs Production Materials
When it comes to 3D printing and production level manufacturing, the plastics available for one technology may not be available for the next. 3D printing material selection is more limited than CNC machined or injection molded parts due to the difficulty in printing certain materials, but there are some common materials between the technologies as well as materials that will be a close representation to bridge the gap. To get the closest match, we have created some guidelines in the chart below.
If you want to use 3D printing to prototype components while remaining as close as possible to a final product that may undergo higher quantity manufacturing, you need to select the closest material match. The best way of doing this is by specifying the key properties that you want to replicate. I suggest starting with key properties that are inherent to the function of the part and moving onto the common mechanical properties listed above.
Here’s an example:
Say you want to design a light pipe, created based on the product need for light transmission. Because you need light transmission, your material choices will be limited to plastics like VeroClear.
If you’re looking at a structural application, the key properties you will be concerned with are young’s modulus and yield strength because you want to replicate both deflection and failure point.
If we return to the light pipe example, let’s assume that you plan to use acrylic for the production parts. In that instance, Acura 60 is a closer match than the VisiClear, as shown in the table below:
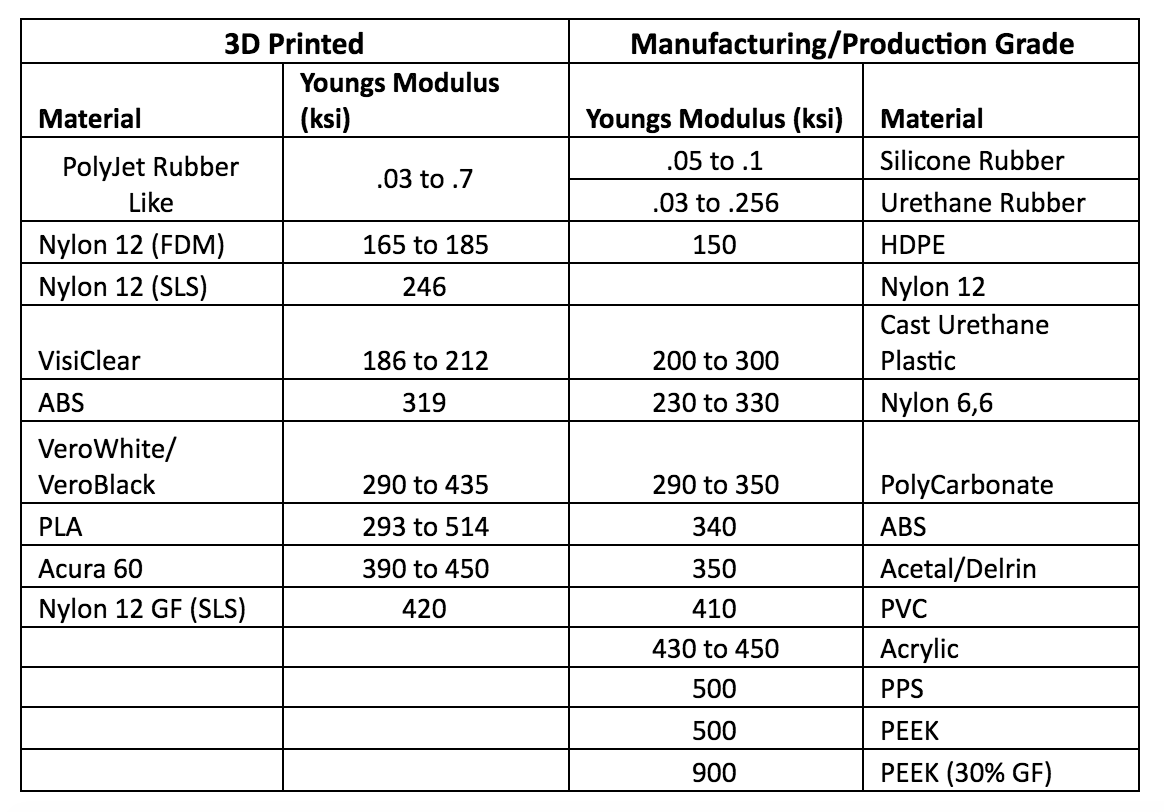
This table is not fully comprehensive, but hopefully it gives you a greater indication of how to match the modulus of a 3D printed component with the manufacturing/production grade counterpart. Additionally, note that this table simply orders the materials by increasing modulus and does not place the best matches side by side. That is to say: If we want to simulate production grade ABS, we will most likely use 3D printed ABS and not the PLA that is listed next to it.
Furthermore, this table omits additional mechanical properties such as elongation and yield strength. As an example, VeroWhite has a modulus close to that of PolyCarbonate (PC), but the elongation is much different. The elongation of VeroWhite is between 10-25%, while unfilled PC has an elongation of between 60 and 100%. That means the materials may behave the same up to the yield strength, but VeroWhite will fail much sooner after the yield point because it’s not capable of the same elongation.
Main Takeaways
There are a wide variety of plastics and an even broader range of combinations. In the design stages, it’s important to first define the critical requirements for your prototype, as well as for future production parts, to inform proper material selection.
From these requirements, a suitable plastic can be chosen based on available options for prototyping, to get the closest representation to the final production units. This will ultimately reduce uncertainty and risk in the final product while increasing the rate of learning in the new product development process.
For more information on 3D printing materials available for prototyping on the China Manufacturing parts, Inc. platform, visit the China Manufacturing parts Website and to get an instant quote for 3D printed parts or injection mold, create a China Manufacturing parts, Inc. account.