Time to read: 8 min
In my last article, we discussed methods of improving part stiffness through geometric changes and why that is an important tool. Here in Part 2 of the “Designing for Stiffness” series, we’ll be looking at changing part stiffness through material properties. We’ll use many of the same formulas, but we’ll focus on the properties we can control with just material selection.
The following paragraphs will detail the specific material properties we’ll examine and how they apply to part stiffness. Furthermore, we’ll work through some example problems to help us understand exactly how we can apply this knowledge.
Material Basics
When we set out to increase or decrease part stiffness by changing the material properties, we’re really saying that we need to select a material with a higher or lower elastic modulus. The elastic modulus is a specific property of a given material that defines how stiff it is. In this article, we’ll also briefly look at the yield and ultimate strength of materials, since they’re somewhat related.
Elastic Modulus
The Elastic Modulus of a material, also known as the Young’s Modulus, is defined as the slope of the stress-strain curve in the linear (elastic) region. We’ll look at some figures to help explain this, but first, let’s recall what stress and strain are:
Stress – Stress is the force per unit area imparted on a part. If we suspend a vertical bar that is 1 square inch and hang a 100 lb weight on the bottom, the stress in the bar will be 100 pounds per square inch (psi).Strain – Strain is defined as the change in length, divided by the original length of a specimen under stress. Going back to our suspended bar example, let’s say that the bar was originally 100 inches, and it stretched a total of 0.25 inches. That means our strain was 0.0025 in/in.
Now that we have that out of the way, we can start to talk about a stress-strain curve. This is a curve that is typically developed through testing materials by “stretching” them with specialized machines. The x axis of the curve is the strain value, while the y axis is the stress value. The figure below from the University of Texas at Arlington details the main components of a simple stress-strain curve.
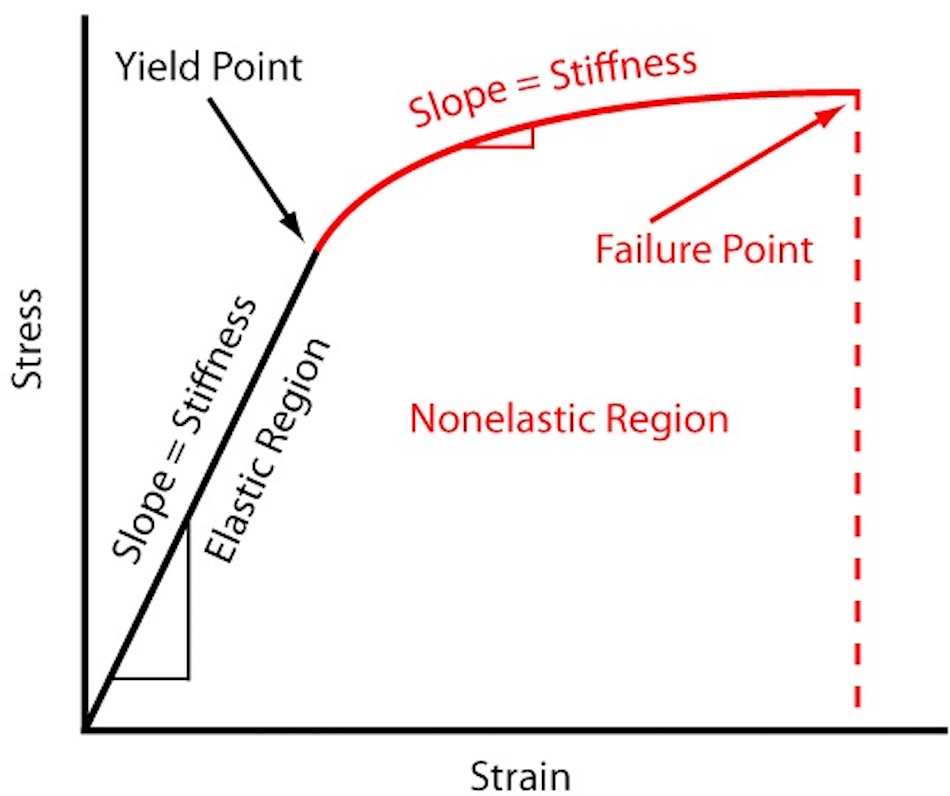
In this image, the slope is said to equal stiffness, which is true for the material itself. That is to say, a material with a steeper slope will be stiffer than a material with a shallower slope. As an example, ABS would have a much steeper slope than a rubber band. This slope of the black line segment is the elastic modulus that was mentioned previously. Up to the yield point, the material behaves elastically, which means that it will return to its original shape and size when the stress is removed. If we exceed the yield point, the material will be permanently deformed, which is typically a bad thing, unless the part is designed to deform such as a rivet. The slope of the red line will not be used in this article because it is not used in the formulas or FEA studies we’re going to investigate.
Yield and Ultimate Tensile Strength
Now that we’re clear on the basics of a stress-strain curve, let’s review two of the most important stress values from these curves. The first is the yield strength of a material, which is the highest stress we can place on a material, without permanently deforming (indicated by the yield point above). Next is the ultimate tensile strength (UTS) of the material, which is defined as the maximum stress the material can support. The stress-strain curve below has these values labeled.
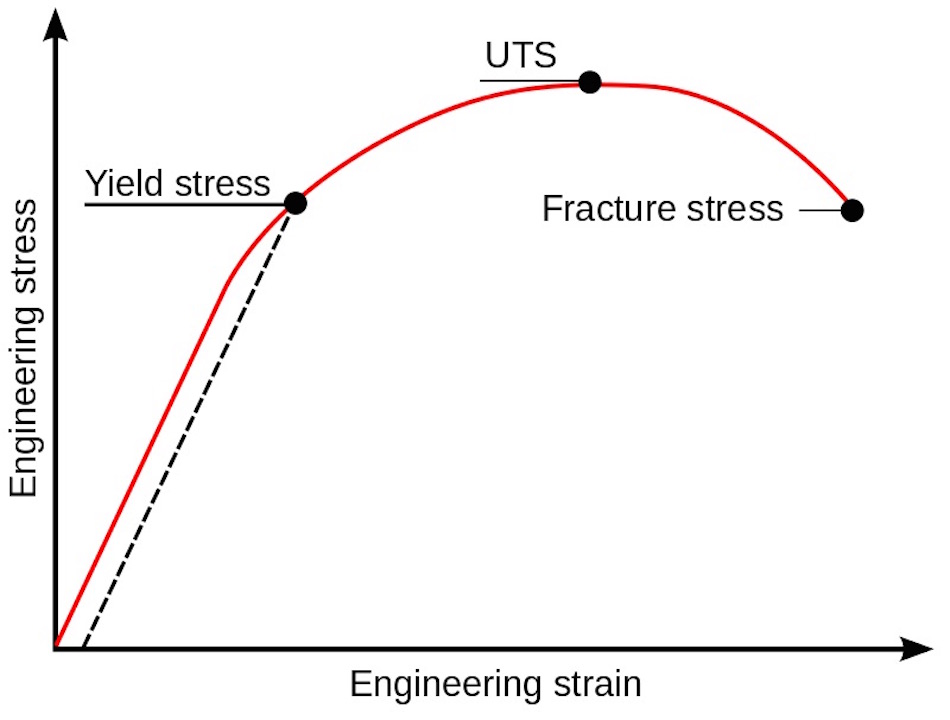
If we draw a horizontal line from the point labeled “Yield stress” to the vertical axis, it will cross at the stress value that will define the material’s yield strength. This is the same for the UTS. Our curves don’t have any numeric values assigned to the axes, so we can’t get physical values, but we define what some of those values are in the examples later in this article.
Basic Problem Explanation
The key reason we need to understand these properties is to know how we can use them in the design of components. We’ll need some components to be very stiff, so they don’t deform under a load. In some cases, we want the material to deform easily, without requiring too much force. This article will solve this basic problem from both sides of the spectrum.
Applied Examples
In this section, we’ll look at how we can actually apply what we’ve learned from the stress-strain curves. But first, we need to review some of the formulas that we discussed in Part 1 of this series.
Formulas of Interest
The first formula we’ll recap defines the deflection of a cantilever beam with a load at one end, as detailed below.
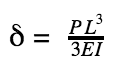
Where:
- δ= Deflection
- P = The Force Applied at the End
- L = The length of the Rod
- E = Elastic Modulus
- I = Area Moment of Inertia (MOI)
Next, we will revisit our stiffness formula as shown below:
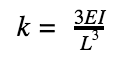
We can see just how the elastic modulus fits in with stiffness from a mathematical standpoint with this formula. The relationship is linear, so if we double our elastic modulus, we double the stiffness. Doubling the stiffness means that it will take twice as much force to deflect a part as compared to its original self. This principle is the heart of our article.
Materials to Consider
The next step in applying this concept is to know the materials we may use and their elastic modulus. The list below details the 3D printed plastics offered by China Manufacturing parts and their elastic modulus:
Material Elastic Modulus (psi)
FDM PLA 293,000 to 514,000
FDM ABS 319,000
VeroWhite/VeroBlack 290,000 to 435,000
SLS Nylon 12 185,000
VisiClear 186,083 to 212,190
These values are published in the Stratasys materials section and may depend on the build orientation of the parts in some cases. In the next example, we’ll use two materials that aren’t listed on the chart but have known properties. Those materials are Nylon 12 (FDM) and Nylon 12 Glass Filled (SLS). These materials are used in the example below to provide better contrast between a material of higher stiffness and lower stiffness. The Nylon 12 (FDM) has a modulus of 185,000 psi while the Nylon 12 Glass Filled (SLS) has a modulus of 420,000 psi. We can see that Nylon 12 Glass Filled is 2.27 times as stiff as regular nylon 12. We’ll use these properties to see just what that means in the examples below.
Design Example – Increasing Stiffness
In this first example, we’ll look back at a simple tube that is cantilevered with a force applied at one end. The figure below shows the fixed end with the image of a lock and the loaded end with the arrow pointing downward.
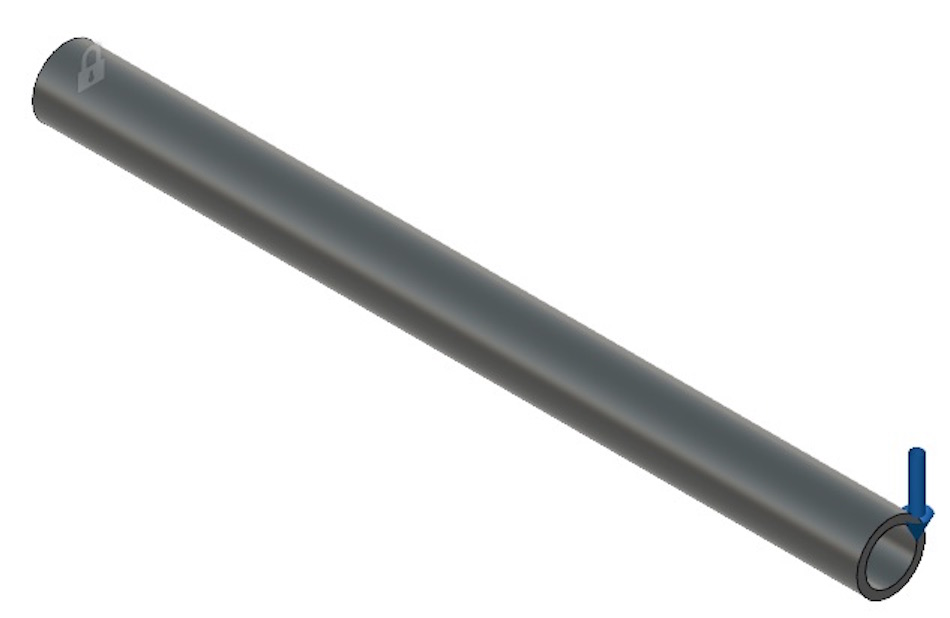
The applied load is 10 lbf, and the first simulation material is Nylon 12, with a modulus of 185,000 psi. The figure below demonstrates that we will see 0.934 inches of deformation at the end with the applied load.
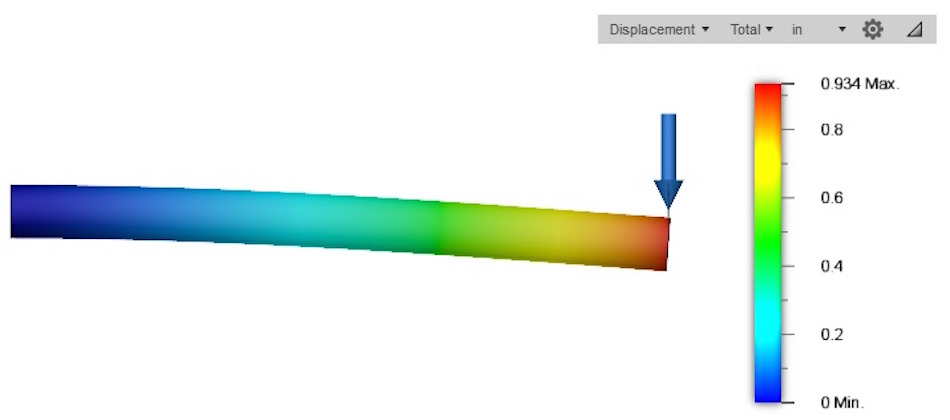
Next, we will change the material to the glass filled Nylon 12 GF and see if we really see the stiffness increase by a factor of 2.27. The figure below details the results of this study.
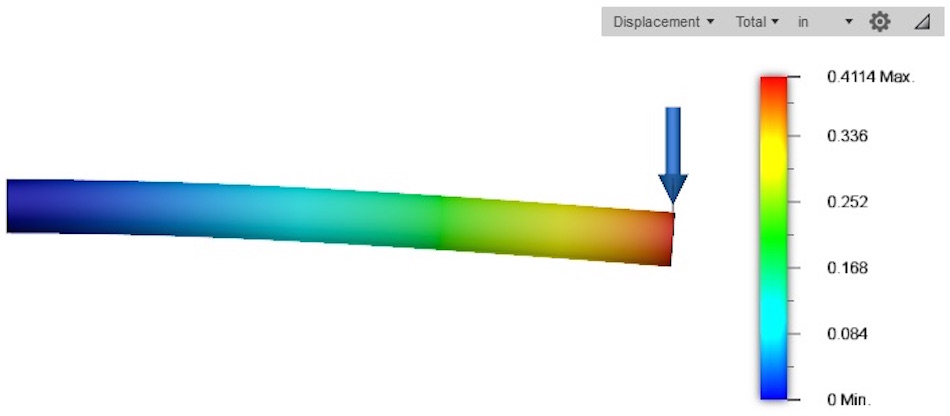
The new deflection is only 0.4114 inches, and if we divide the original 0.934 inches by the new 0.4114 inches, we get exactly 2.27. This tells us that our FEA study agrees perfectly with our increase in material stiffness, as a result of changing the elastic modulus.
In this example, we’re using a simple shape, but this concept has real-world applications. We may want to increase the stiffness of a plastic hook that will hold items, so they don’t fall off under a load. Another example may be increasing the stiffness of enclosures and housings, so the walls don’t deform or collapse as easily. It is likely that a large number of the plastic parts you use in your everyday life have been carefully designed to achieve the appropriate stiffness.
Design Example – Decreasing Stiffness
In this next example, we’re going to look at a case in which we may actually want to reduce the stiffness. Let’s travel back to the snap-fit example from my article on Mechanical Fasteners, as shown below.
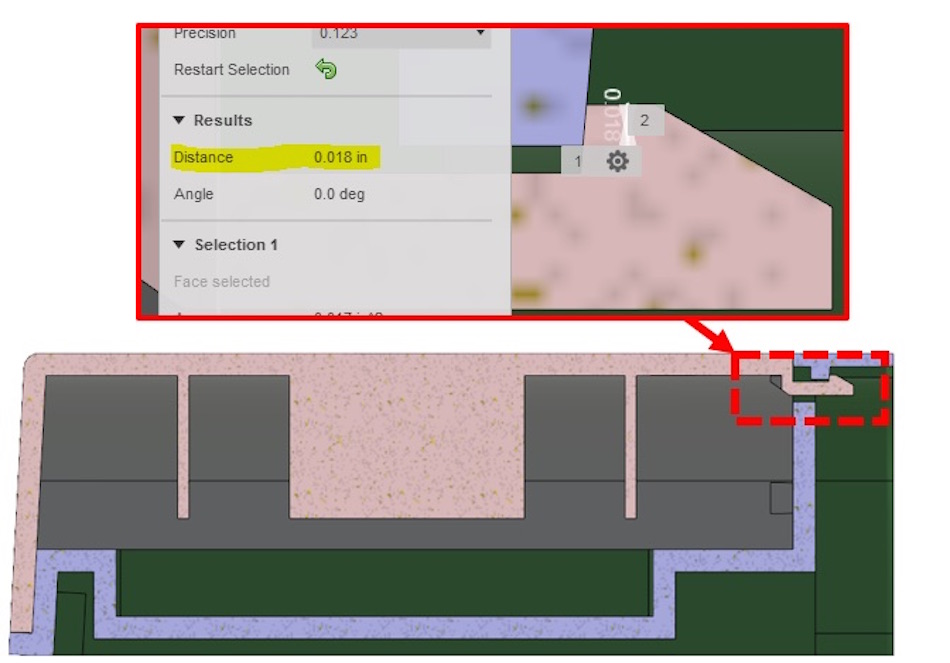
In this image, we can see that the snap-fit must deform 0.018 inches to clear the feature that retains it. However, if the material is really stiff, the stresses will be too high in this component when it does undergo 0.018 inches of deflection. Let’s see what the stresses are when the snap deforms this much, and the part is made of Nylon 12 GF with a 420,000 psi modulus. The first image below demonstrates a 4.136 lbf load generating the 0.018” of deformation.
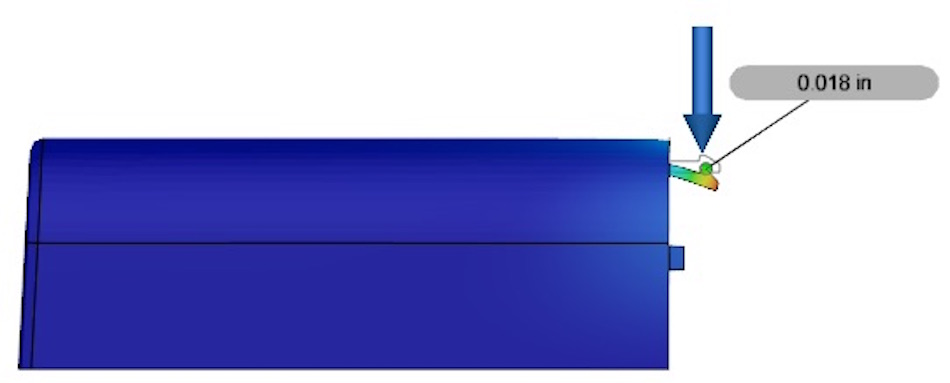
Once we have achieved the deflection we need, we can look at the stresses that will be present when the part deflects this much. The image below is of the same simulation, but we are now looking at the stresses in the part.
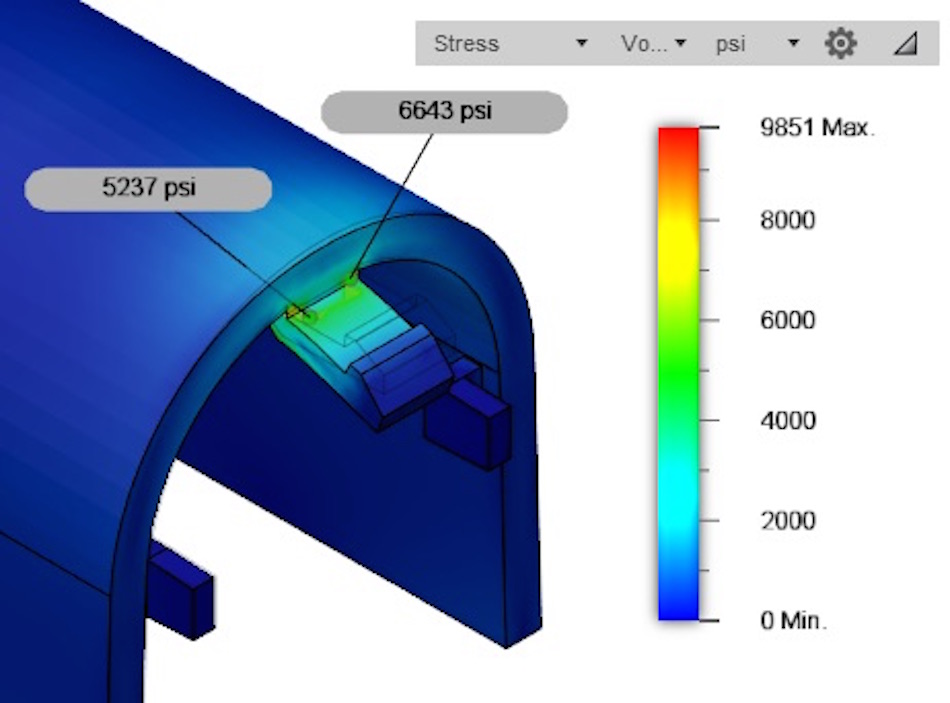
This analysis indicates that we are seeing stresses well in excess of our 5,250 yield strength, so we will likely damage this part simply by installing and removing this cover. We would almost certainly see stress cracks forming in the corners after a few cycles.
What if we came in with a material that had a lower modulus, like our original Nylon 12 (185,000 psi)? If you recall from the stress-strain curves we discussed, a material that has a lower modulus will undergo more strain for a given stress value. In simple terms, that means we can expect the snap to move the same 0.018”, with much lower stresses.
Once again, we’ll run an FEA study, but with our lower modulus Nylon 12 this time. The results below are of the same study; however, the load on the snap has been reduced to 1.822 lbf because a lower modulus material requires less force to deflect the same amount.
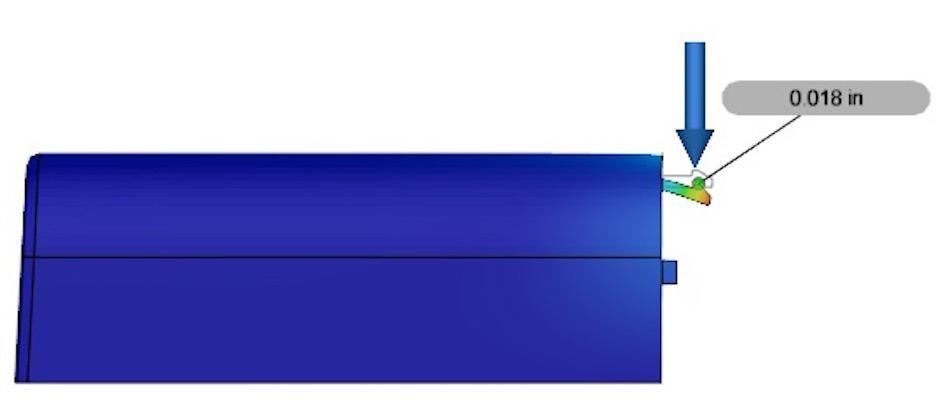
We have achieved the 0.018” of deflection needed, so let’s take a look at the stresses with which we’re concerned in the image below.
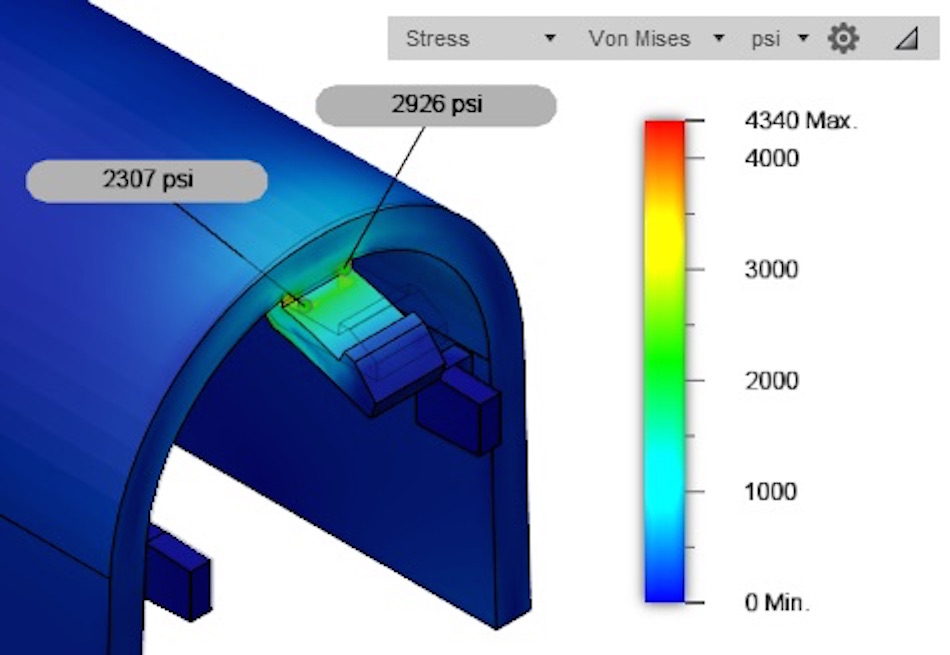
The area that was stressed to 6,643 psi before is now only at 2,926 psi. And if you’re anything like me, you’ve already done the math to ensure that the stress in the Nylon 12 GF is exactly 2.27 times as much as the standard Nylon 12.
This concept can be further expanded to allow for different insertion and removal forces for snap-fit parts, so I encourage you to play around with different modulus materials to get a feel for how they behave.
Main Takeaways
I hope the principles in this article grow more valuable to you as your material knowledge and material options increase. To check out material options for 3D printing and CNC machining service, visit the China Manufacturing parts Hardware Guide.