Time to read: 5 min
Collaborative robots, commonly known as cobots, are so named because they are designed to provide collaborative, safe assistance to people. The first cobot was invented in 1996 by J. Edward Colgate and Michael Pashkin – and today, cobots are growing increasingly popular in manufacturing and industrial settings, performing simple, repetitive tasks such as feeding a CNC machine with parts or taking machined parts from a CNC machine and putting them in crates for inspection.
Cobots vs Robots
Cobots are different from traditional industrial robots as they tend to be smaller, less expensive, and supremely flexible. Whereas a traditional manufacturing robot can cost hundreds of thousands of dollars, most cobots cost less than fifty thousand dollars. And they’re considered revolutionary because they can function directly next to humans without cages or safety gates.
Common Cobot Utilizations
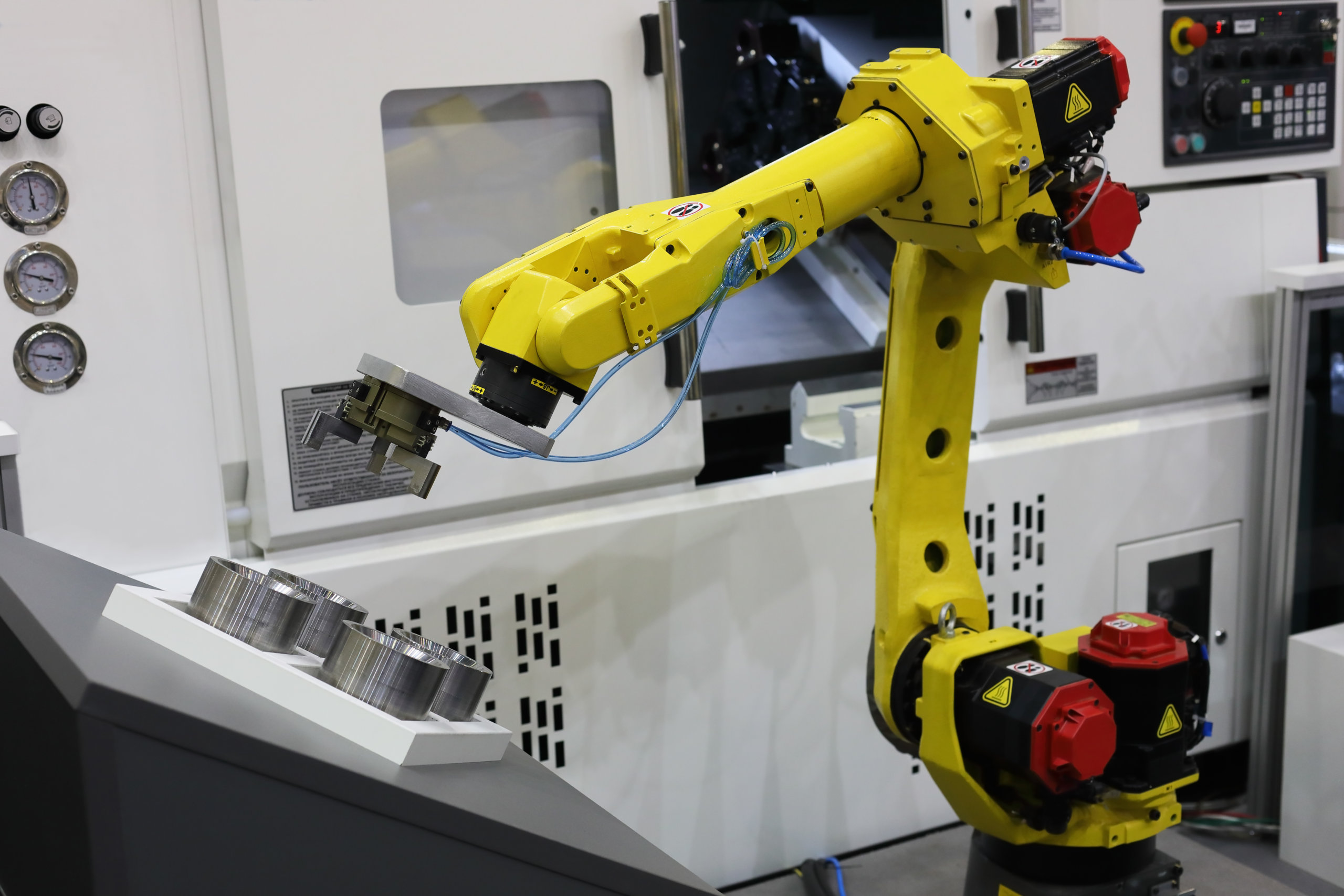
Machine tending is the most common utilization of cobots in manufacturing applications, due to the overwhelmingly mundane nature of the task. Parts must be individually loaded, machined, and then unloaded. By utilizing cobots to manage that monotony, employees can instead focus on more complex tasks. It’s even possible for a single employee to oversee the operations of several machines at once.
The popularity of cobots in machining can be attributed to their ability to perform tasks that may be riskier from a safety standpoint. Cobots are ideal for manual operations where the employees would otherwise be exposed to conditions such as excessive heat, noise, or pollutants. It’s also no secret that the tasks we ask humans to perform in manufacturing environments are often ergonomically challenging and cause excessive stress on the human body. Cobots are an excellent solution to the ergonomic problem, performing all the physically strenuous tasks and protecting the health and safety of the employees.
Examples of other common cobot utilizations include:
- Object Relocation: Specifically picking and placing from bins or a conveyor system
- Packaging/Palletizing: Prepping products for shipment, box assembly, and placing objects on pallets
- Manufacturing Processes: Utilization of tooling to perform a task on a workpiece – such as gluing, welding, soldering
- Post-Machining Finishing: Manual operations involving tooling and precision – such as deburring, polishing, grinding
Why Design Your Cobot Tooling?
Now that we understand some of the most common cobot applications, it is time to consider the best route for obtaining cobot tooling. On the one hand, you could purchase a pre-made system, but that may result in having an incorrect configuration for the task you are hoping to have the cobot accomplish. On the other, designing cobot tooling or components yourself can be a challenging task – albeit, we think a rewarding one.
Choosing to design cobot tooling yourself also means that you can determine the ideal cobot/human interaction. A cobot’s automation can be partial, requiring human input and assistance, or complete, allowing the cobot to function autonomously. Designing and building your cobot components ensures that it is correctly and purposefully incorporated into your manufacturing environment. You can simplify or modify the movements and operation of the cobot to fit in with your company’s processes and approach to automation.
Which Cobot Components are Optimal for Designing and CNC Machining?
When designing cobot components, the most obvious for CNC machining is the End of Arm Tooling (EOAT). The term EOAT defines a broad group of tooling that is attached to the end of the robotic arm. This tooling is what connects and allows interactions to occur with cobots and the physical world around them.
There are endless possibilities for EOAT configurations and applications. Some are more optimal for CNC machining though, so be sure to reference our CNC quick guide at the end of this article to help you determine where you should start with your cobot’s End of Arm Tooling.
Vacuum Grippers
Popular for numerous cobot applications, vacuum-powered grippers are an excellent choice for CNC machining. These types of tooling are easy to operate and provide impressive lifting power for their size. These types of EOAT grippers are particularly useful for picking and placing applications, especially where workpieces have uneven or irregularly shaped surfaces. Vacuum gripper EOATs typically consist of a frame with attachment points for suction cups and vacuum lines – although, some types utilize electricity instead of an external air supply. Both the frame and attachment points are suitable for CNC machining.
Pro-tip: Choose lightweight materials for CNC machined EOAT. China Manufacturing parts offers a wide range of materials for cobot tooling, such as aluminum, titanium, and various grades of plastic polymers.
Mechanical Grippers
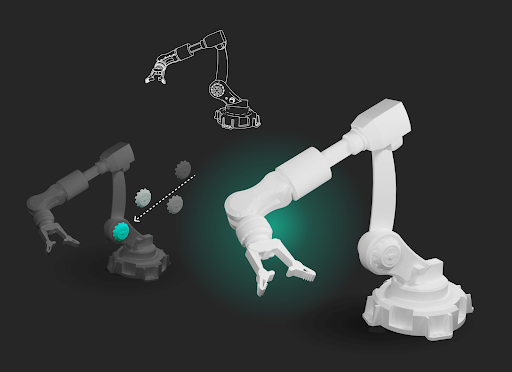
If you’ve ever been around tiny humans (aka children) or studied biomechanics, you’ve probably heard of the pincer grasp. This is humans’ ability to hold an object between their thumb and index finger. We start to develop this skill as babies around the age of 9-10 months. It’s an important skill that allows for precision when picking up and relocating objects. The mechanical gripper EOAT was developed to model the human pincer grasp, typically involving gripper mechanisms with a type of fingers attached to the end of them. The fingers of the mechanical grippers are coated with -or have been covered with- material that provides grip, without allowing objects to slide off of them, such as silicon or rubber. All of the components, except for the gripping surfaces, can be CNC machined.
Pro-tip: Aim for a mechanical gripper design that will allow you to replace the fingers as the gripping surface wears.
Manufacturing Process Tools
With the advancements in cobot design and maneuverability, companies also choose to have cobots perform the tedious manufacturing process tasks they require regularly. Great examples of these are drilling, sealant application, welding, deburring, and shearing processes. To determine which manufacturing processes you should consider for cobot incorporation first, consider the following:
- How ergonomic is the process now? If there is significant wear on humans performing the tasks, consider breaking them up and having a cobot perform the most physically strenuous task component.
- Does the manufacturing process require steady pressure, application speed, or consistent timing? If so, cobots are ideal for achieving consistency.
- Would the incorporation of a cobot in the manufacturing process allow for more throughput in the manufacturing system as a whole? Cobots provide a helping hand to increase productivity.
Common EOAT types which are suitable for CNC machining include:
- Cobot welding nozzles
- Cobot sealant or caulk applicators
- Cobot drilling heads
- Cobot shearing tools
Pro-tip: Design your EOAT with a tapered end, where possible. This will enable you to utilize the tooling to reach narrow crevices and even inside smaller cavities.
For more, check out our Ultimate Guide to CNC Machining which will help spark your innovative energy to begin designing your custom cobot components today. Simply upload a design for an instant quote and DFM feedback and start optimizing your manufacturing process today!