Time to read: 6 min
EDM (Electrical Discharge Machining) is a rapidly growing and versatile manufacturing method for cutting parts out of stock material. In 2022, the EDM market is growing at a rapid, predictable rate of 6.9% CAGR (based on a market size of US$5.3 billion in the year 2020 and projected growth through 2027).
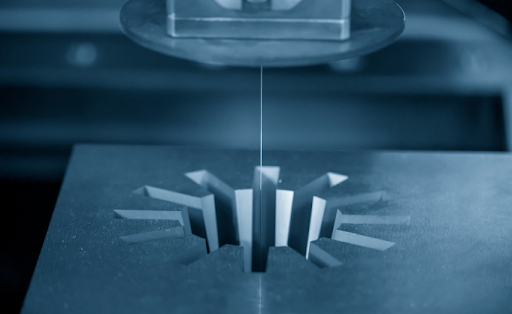
What is the Electrical Discharge Machining (EDM) Process?
EDM is a non-traditional form of subtractive machining (typically via CNC) whereby a component is cut from a volume of raw material.
- Electrical Discharge Machining is unique because it does not utilize sharp tooling for material removal, as traditional CNC machining does. Instead, EDM removes material using a flow of electricity and thermal energy, which is why it’s referred to as an electro-mechanical process.
- EDM works using controlled electric spark erosion where the electric spark serves as a ‘cutting tool’ to erode or remove material from a workpiece to produce the desired part shape.
- The sparks are turned on and off to create a pulsating electrical charge that removes material at a steady, controlled rate.
- EDM is a non-contact machining method and does not exert cutting forces on the part, so it works particularly well for delicate structures and complex geometries.
At a microscopic level during EDM:
- Spark erosion occurs between the anode (a component on the Electrical Discharge Machine), the cathode (the tooling material or part), and a dielectric EDM fluid.
- The dielectric fluid is ionized and these positive ions hit the surface of the cathode. This causes the surface of the part being machined to heat up to extremely high temperatures (thousands of degrees Fahrenheit) which vaporizes the metal.
- Microscopic bits of vaporized metal flow into the dielectric fluid, form chippings, and are flushed away from the surface of the machined part.
- Occasionally, chips adhere to the surface of the part and form a localized area of rough texture. Some materials are more prone to chip adhesion than others.
Like traditional CNC machining, part movement is typically controlled through pre-programmed input movements. For conductive materials, the workpiece completes the electrical circuit.
EDM is accomplished through two methods:
- Sinker EDM: a pre-shaped or pre-formed electrode (which is typically CNC machined) with the geometry of the desired cavity is pressed into the workpiece to create said cavity. This type of EDM is also referred to as die-sinking EDM, or cavity-type EDM, and is optimal for producing geometries like internal gears.
- Wire EDM: a thin, metal wire is used to cut through material and form the desired part shape.
China Manufacturing parts offers both types of Electrical Discharge Machining (EDM) processes, which are useful for cutting deep pockets and complex features like gears or holes with keyways.
Material Considerations for Electrical Discharge Machining (EDM)
Electrical Discharge Machining can generally be performed on all conductive materials. Conductive materials range from metals to graphite (a non-metallic conductive material commonly utilized for sinker EDM electrodes). Due to the thermo-electric process that removes material, EDM is not a good choice for non-conductive materials. EDM also tends to be more expensive than traditional CNC machining, and so should be reserved for components with thin-walls or complex geometries.
Best Electrical Discharge Machining Materials
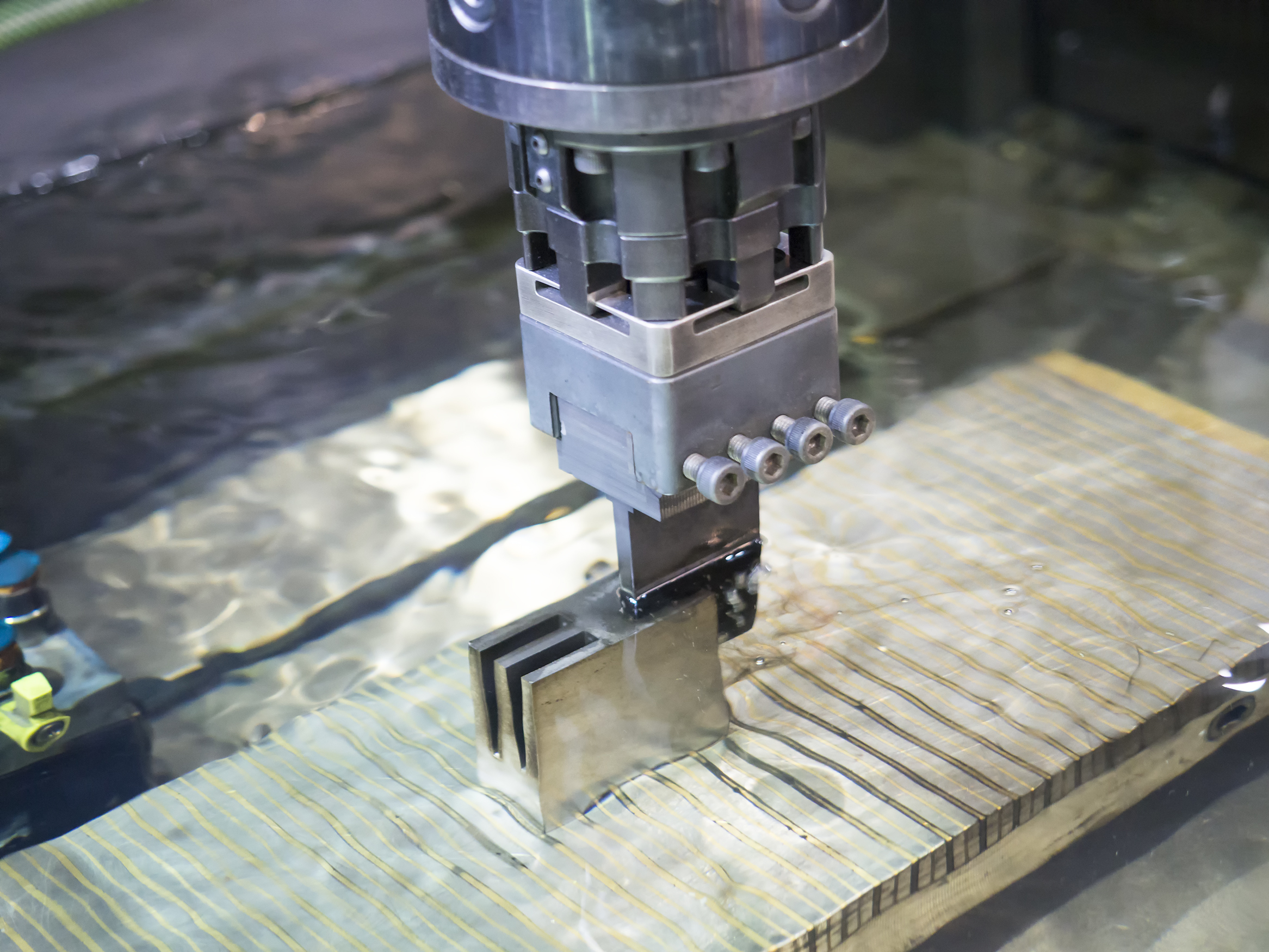
EDM A2 Tool Steel/Steel
Steel is a great choice for Electrical Discharge Machining as it has excellent wear resistance and toughness. A2 Tool Steel and other grades of steel are commonly used to make fixtures, tools, tool holders, gauges, bolts, torsion bars, shafts, and punches.
There are four metallurgically distinct layers produced on the EDM cut cross-section of A2 Tool Steel and other grades of steel:
- An unaffected cross-section furthest from the point of impact
- A tempered layer of the cross section next to the unaffected layer that’s slightly harder than the unaffected layer. This layer doesn’t heat to the hardening temperature.
- A rehardened layer on top of the tempered layer formed by the temperature rising above the austenitizing (hardening) temperature for the metal. This layer is a martensite that has a hard and brittle structure.
- A melted and resolidified layer (aka the white zone) where a rapidly resolidified layer forms and induces long pillar crystal growth from the surface of the metal. This layer is prone to fracturing along the direction of the crystal growth. The carbon content in this area can also grow or diminish during cutting due to flow of carbon atoms to and from the dielectric fluid.
Tips for EDM of A2 Tool Steel/Other Grades of Steel:
- Shorten the spark duration to reduce the thickness of the brittle metallurgical layers and obtain fine finishing of the cut area.
- Maintain adequate flushing to reduce chips from forming a bridge for current to flow across. Such a bridge can cause burns that look like porosity or slag inclusions.
- Increase off time to reduce the possibility of double sparking ignitions. Such ignitions lead to constantly burning arcs between the electrode and work piece.
EDM Aluminum
EDM Aluminum is one of the most commonly used metals in the world because of its excellent strength-to-weight ratio, low cost, and recyclability.
Tips for EDM of Aluminum:
- Aim for a higher pulse power supply no-load voltage amplitude by processing pulse gap (reducing pulse width). This helps to decrease the potential for debris to attach to the EDM electrode wire.
- Ensure fluid flow is equal for the top and bottom portions of the EDM wire when cutting.
- Ensure filtering is sufficient for the dielectric fluid to allow for quick removal of debris.
- If you are having trouble cutting with certain metal wires, try a brass wire instead.
EDM Brass
360 Brass, also known as free machining brass, is commonly used for a variety of parts including gears, lock components, pipe fittings, and ornamental applications. Brass is a good choice for wire for EDM and EDM tubing. Brass is also a commonly used EDM electrode material.
EDM Copper
101 and 110 copper alloys offer excellent thermal and electrical conductivity, which makes them natural choices for bus bars, wire connectors, and other electrical applications. Wire EDM of copper also results in a re-cast layer but the layer does not pose the same microscopic issues that EDM cut steel shows (cracking, porosity, etc.). This is because copper distributes the heat from the EDM process better due to its higher thermal conductivity. Copper’s thermal conductivity also causes a high rate of energy dissipation at the surface of the workpiece, which inhibits material removal.
Tips for EDM Copper Alloys:
- Reduce the duration of the EDM spark to reduce the chance of sublimation.
- Increase amperage to maintain the same amount of spark intensity as less conductive materials.
- Utilize negative polarity to the electrode along with a high amperage setting (which may require a bigger electrode) to reduce electrode wear and a good material removal rate.
- Ensure adequate flushing of the workpiece, meaning: maintain a pressure and flow rate that doesn’t induce turbulence, but still sufficiently removes debris.
EDM Titanium
Titanium is an increasingly popular material because it has excellent corrosion resistance, high strength, and low density. Titanium may also be preferred over other materials like steel due to its ability to withstand both high and sub-zero temperatures. Common use cases include aerospace fasteners, turbine blades, engine components, sports equipment and marine applications.
Tips for EDM Titanium Alloys:
- A slight increase in pulse-on time can lower the tooling wear rate.
- Decrease pulse-on current and time to decrease white layer thickness.
China Manufacturing parts is the ultimate CNC EDM provider. Click here to see all of the materials China Manufacturing parts, Inc. can cut with EDM. Our intelligent platform lets you easily upload your 3D models or 2D drawings and get an instant quote and DfM feedback. At China Manufacturing parts, we’re also experts in CNC Machining, Injection Molding, Urethane Casting, and 3D Printing.
If you’re ready to start uploading your EDM CNC design files, you can get an online quote in minutes.