Time to read: 5 min
Developing a new product and bringing it to market is a massive undertaking, but it’s also what drives the advancement of any industry. The Harvard Business Review says that “ideally, a successful new product can set industry standards—standards that become another company’s barrier to entry—or open up crucial new markets.”
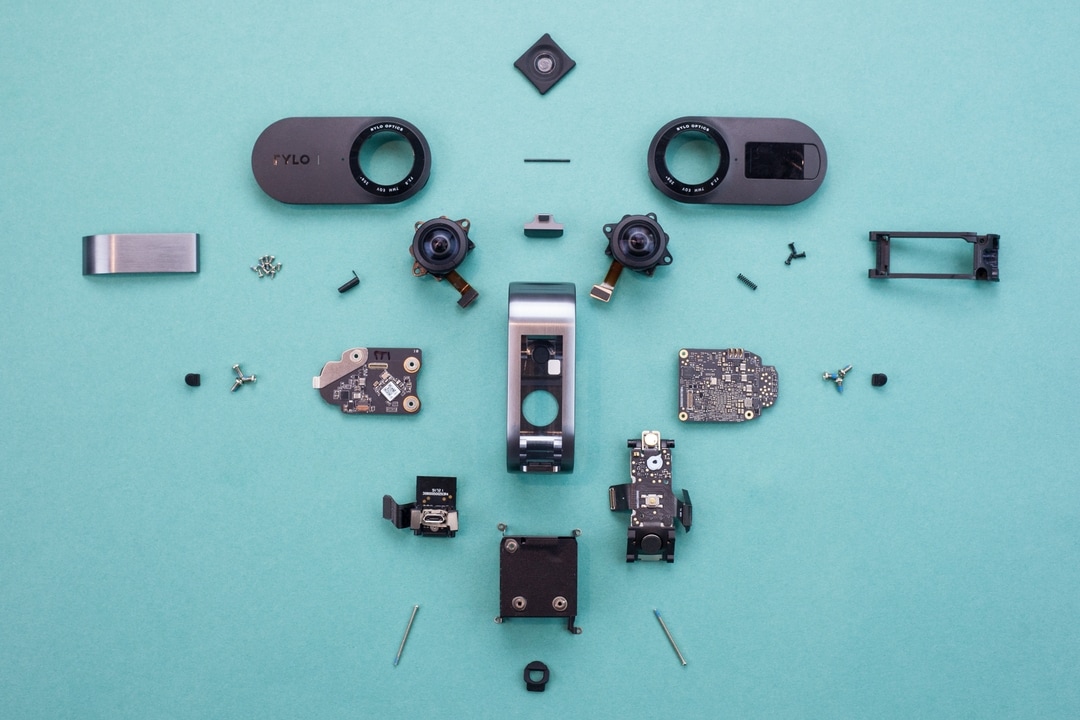
Not every product can pace the industry, of course, but every new project benefits from a considered, organized approach. It’s vitally important that all the working parts are managed equally so that nothing is overlooked in the process. It’s how you ensure that your project team is working together seamlessly so that the design, prototyping, engineering, and manufacturing phases are efficient and effective.
Proper new product introduction (NPI) planning is valuable because it creates a concise action plan to manufacture your product from start to finish. Successful NPI improves the clarity of the design and implementation process while allowing you to both monitor all the stages and manage the other aspects of your business effectively.
In this article, we’ll discuss each stage of the design and manufacturing process, and how a well-thought-out new product introduction process can benefit you.
Product Conceptualization
All great inventions and new products start with conceptualization or the conceptual stage of developing an idea. This is when brainstorming happens and the idea begins to form.
It’s also the time to start planning, even if you’re only working with rough ideas or simple sketches. There are two simple goals with the conceptualization process: determine which ideas will work and eliminate those that aren’t beneficial. This is where the concept of ‘fail hard and fail fast’ applies — you want to discuss and vet your concepts, then eliminate those likely to fail and focus on developing the others.

Most inventions or new products aim to solve an existing problem. So, you must first clearly identify and articulate the problem that needs solving (ideally one with existing market demand for a solution) and then figure out how to solve it.
A well-defined problem statement is critical because it helps to accurately shape your concepts into a fleshed-out design. But defining the problem and honing in on your solution are only the first steps in NPI.
Research and Development
When bringing a new product to market, extensive research is required to confirm market demand (aka are people are interested in this product). This stage is when you perform due diligence on your competitors in the space. One way to perform competitor research is to answer the following questions:
- Does a similar product already exist in the industry?
- Does your product already exist in the market?
- Do patents or other IP hinder your ability to execute your idea?
- If your product already exists, what improvements or modifications to that product will differentiate it in the market?
Next, you need to define what the function of the product is for your consumers and identify what their buying cycles look like as well.
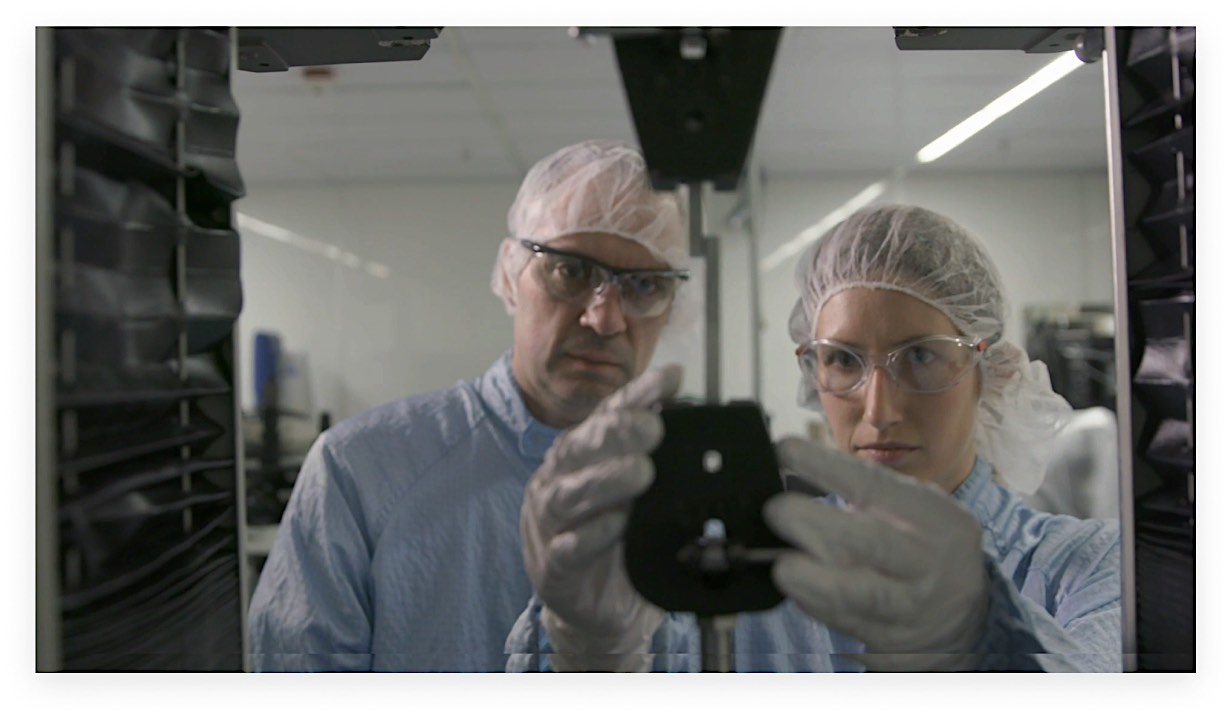
After your research comes design and development. This is when you narrow down your conceptualized ideas into a preliminary design. You and your team will begin to map out the costs of the project, including the manpower required and any costs associated with development and testing.
Doing so means performing the necessary calculations for required dimensions and material selection based on desired functionality. This is the time to explore which materials are optimal for manufacturing the product and for your budget.
This inquiry and assessment process is time-consuming and can be tedious, but proper research and development yield many benefits:
- Lower manufacturing costs
- Decreased risk of designing products too close to existing products or patents
- Reduced testing and prototyping costs
- Strategic competitive advantage over existing, similar products
Mechanical Design and Modeling
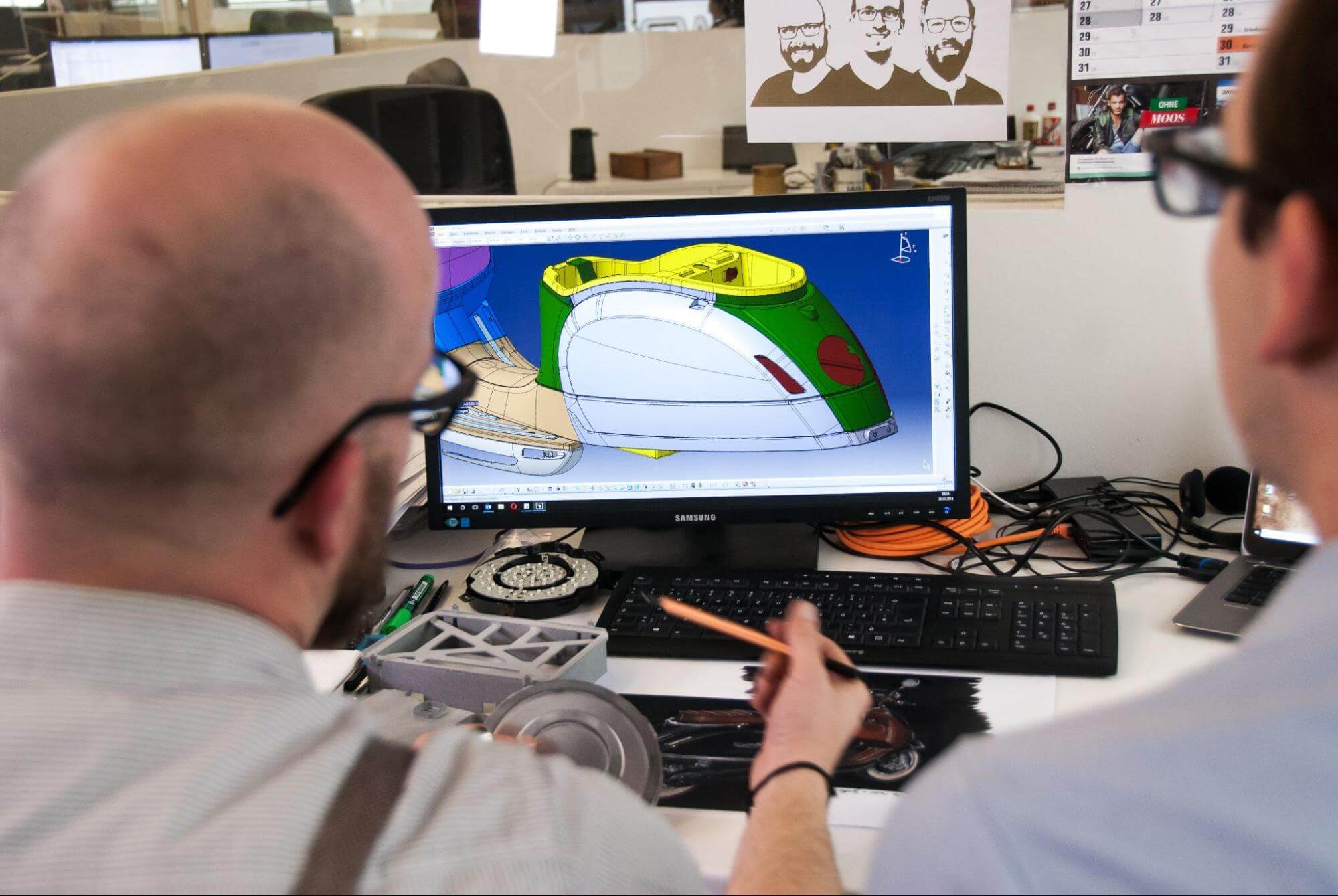
The mechanical design/CAD stage is where you will start to see your idea come to life. Visualization of your design is solidified with the creation of 3D models and 2D engineering drawings, whether you’re modifying an existing product or starting from scratch with an entirely new design.
Typically, Design for Manufacturing (DfM) is a key part of this step in the process. That means choosing the manufacturing processes for each component of the assembly: injection molding, CNC machining, 3D Printing, or something else.
Working with an experienced CNC machining vendor, like China Manufacturing parts, simplifies the DfM process. You can leverage their machining expertise to make design choices that efficiently use materials and generally optimize production time and costs. It also helps you design the quality assurance objectives used to validate the product.
And design validation and testing vary depending on the certification requirements and application of the product — it may range from physical testing such as stress or fatigue testing to theoretical testing using software to do finite element analysis. Once data is collected from the testing, further optimizations and design modifications are informed by the results.
Prototype Manufacturing
The manufacturing process generally begins with prototypes and samples. Design and manufacturing engineers should work closely together during the prototyping phase to efficiently work out any issues. Issues may require a structured change process to be followed (such as DfM or formal design change request from the customer).
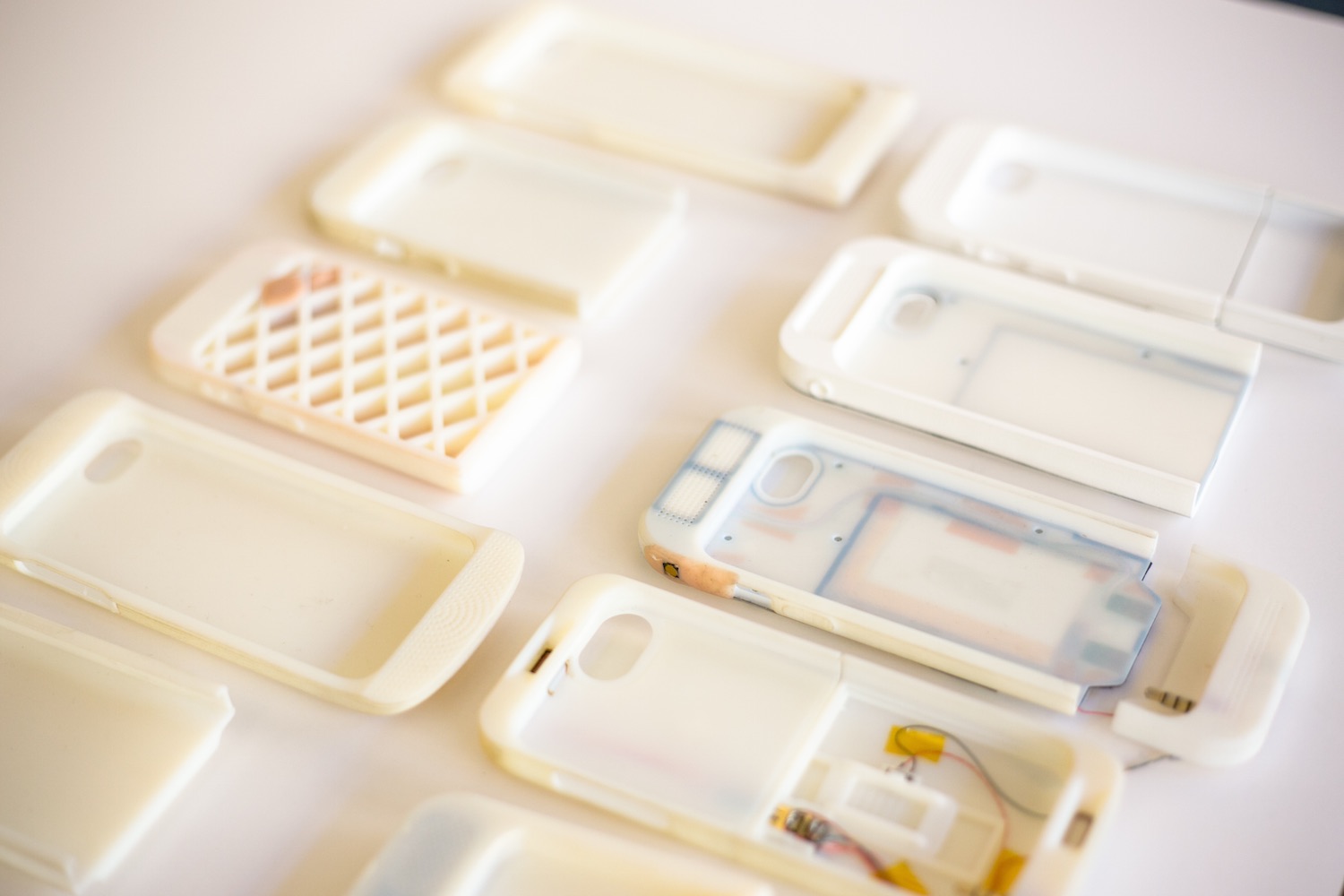
Once finished, prototypes must be inspected to ensure they meet quality control requirements. Then comes testing to ensure that they meet the criteria for the design.
If the product passes all necessary testing, then you move to mid-scale manufacturing or bridge production. The product may also need to undergo more extensive quality inspection.
In many industries, bridge production is the last step prior to full-scale production. For others, further testing and customer feedback, as well as customer-directed design optimization or designer and engineer observation are required before moving to production. For example, aerospace components typically undergo extensive FAA-required testing before components can be certified and manufactured.
Production Level Manufacturing
Full scale production is typically the final stage of NPI. This is when any post-processing or secondary operations are completed and your product is assembled.
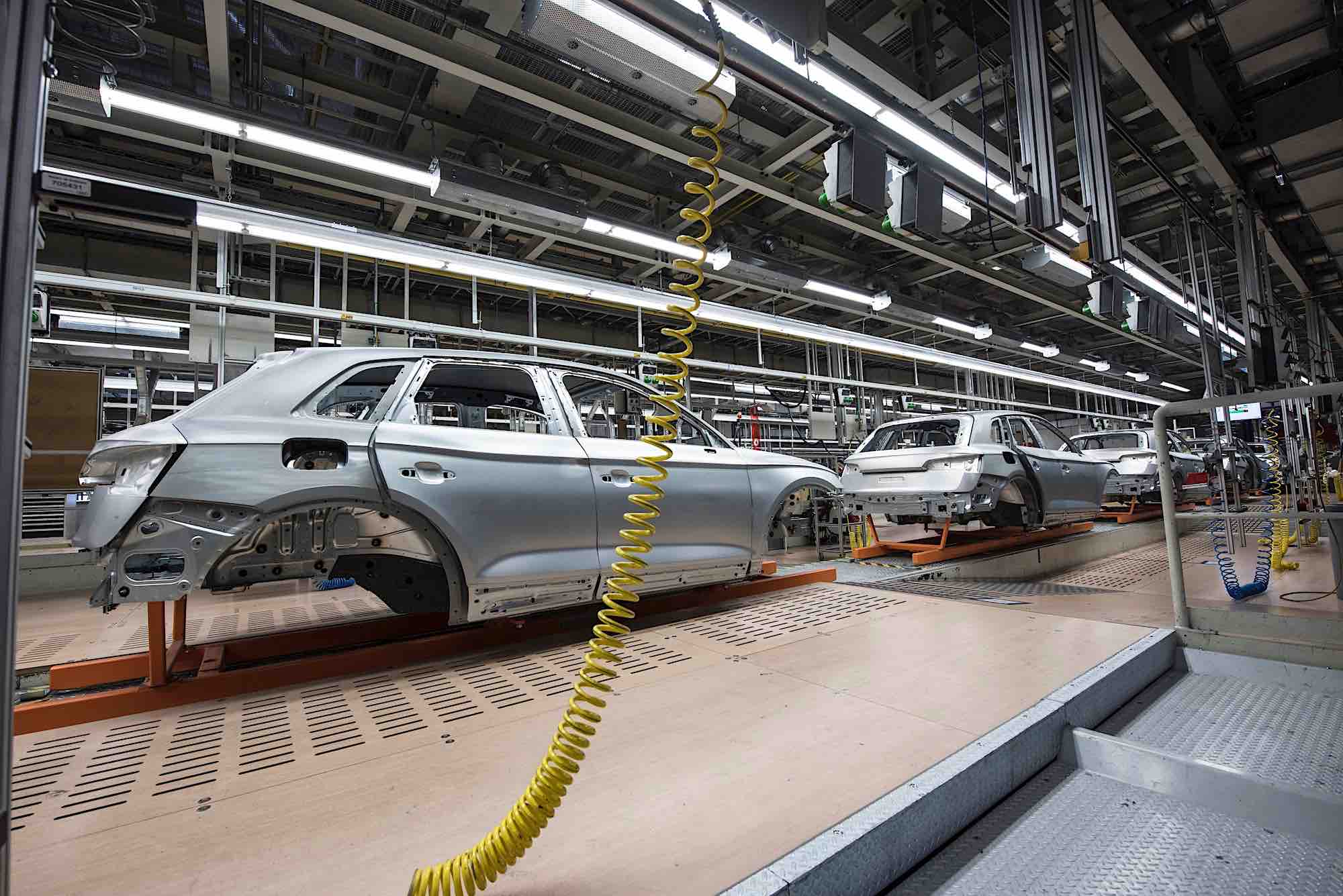
Products produced in production-level manufacturing facilities also typically go through a less rigorous final inspection and quality check defined during the design process. For aerospace parts, some products are required to have in-house 3rd party testing or inspections prior to release from production. Deployment to production typically means that the design engineers hand the project over completely to manufacturing engineers or their production partners, like China Manufacturing parts.
Conclusion
Now that you know what the new product introduction process looks like, you have an idea of how challenging it can be. Using this guide, you can create a process that works for you, but keep in mind that there are advantages to working with an experienced manufacturing partner. Partnering with a digital manufacturing company can provide peace of mind knowing that experts are helping refine your designs and ensure that the manufacturing process will go smoothly.
Fictiv’s network of experienced and knowledgeable partners can deliver you the precision parts you need to make your next new product a success. All you need to do is create an account and upload your part, and you can get an instant quote with free DfM feedback today!