Time to read: 2 min
The Challenge: Avoid Unnecessary Costs and Complexity
Injected molded parts that have recessed features called undercuts are more difficult to eject during manufacturing. This adds costs and complexity to tooling, and undercuts that are too deep may be especially hard to remove. Yet, some product designs use undercuts for a fastening point or locating edge. Examples include the threads on injection-molded fasteners.
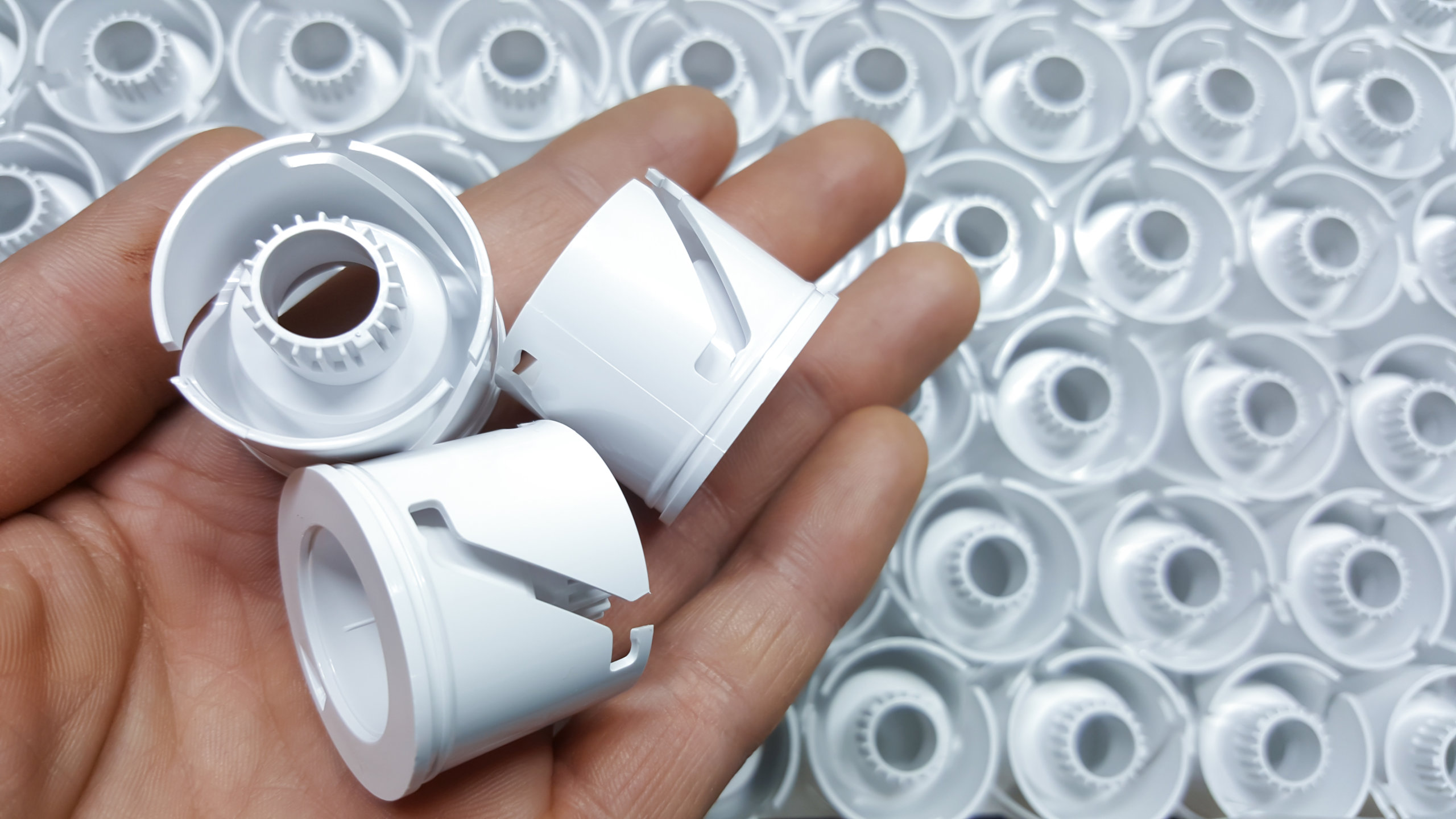
The Solution: Necessary Undercuts and Expert Design Help
When you partner with China Manufacturing parts, we’ll help you determine which undercuts are necessary for your design – and which ones are not. If your part requires undercuts, we may recommend using shut-offs, bump-offs, or sliding side-actions and cores. Moving the parting line is also an option if the undercut is on an external surface and you can adjust your draft angles accordingly.
For the internal regions and the sides of parts, shut-offs can be used. Shut-offs are also a good choice for snap-fits, and for holes and handles. Bump-offs, or stripping undercuts, can be used if the part feature is flexible enough to allow for expansion and deformation. Slide action cores are inserts that slide into the mold as it closes and slide out of the mold before it opens. They also help with part removal.
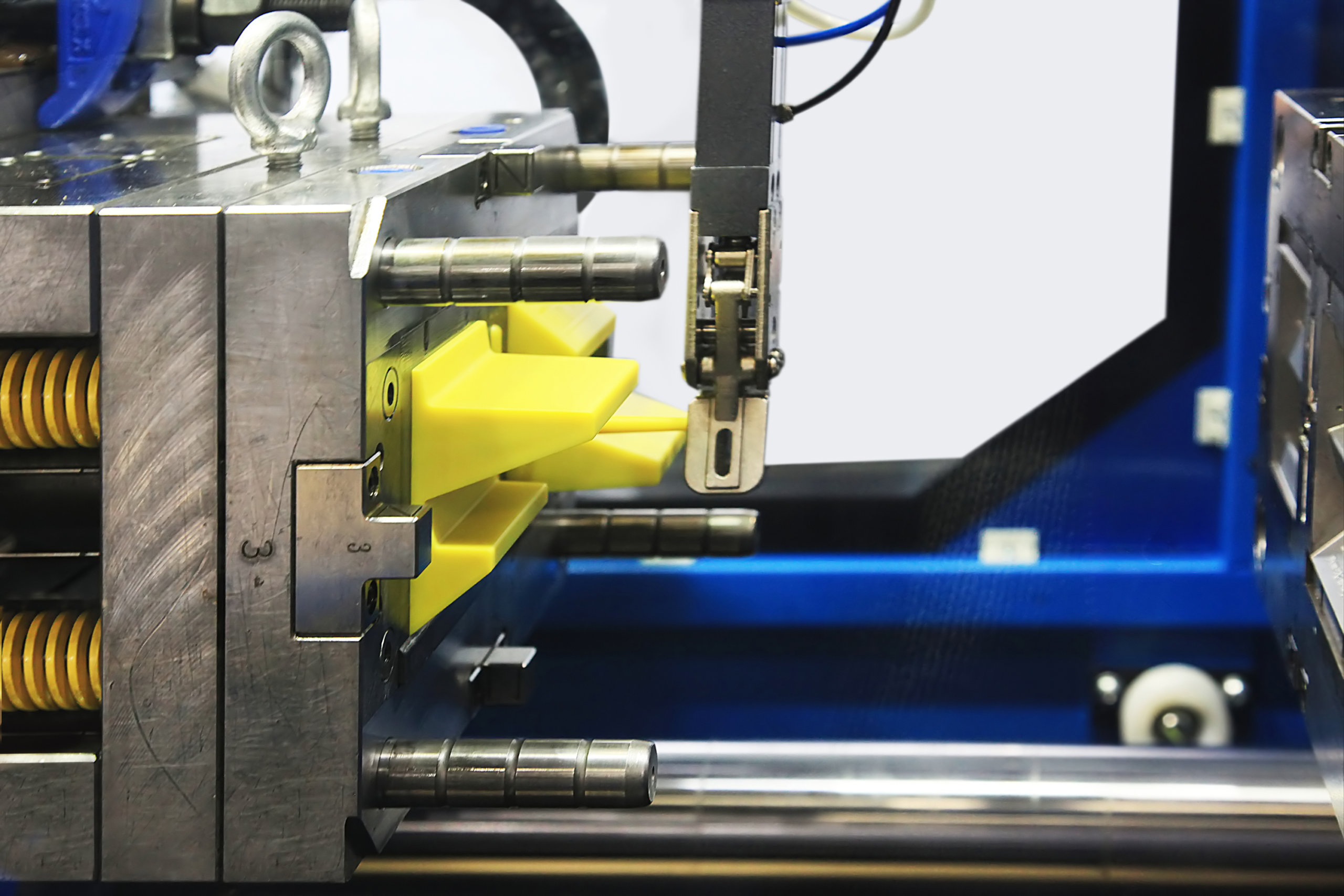
The Impact: Better, More Cost-Effective Injection Molded Parts
Fictiv’s design for manufacturing (DFM) review helps you to avoid common injection molding mistakes such as the use of unnecessary undercuts. Yet, if your design requires them, we can help you to implement undercuts efficiently and cost-effectively. Our DFM process also supports better injection molded parts by helping you to avoid other types of mold design mistakes and part design mistakes.
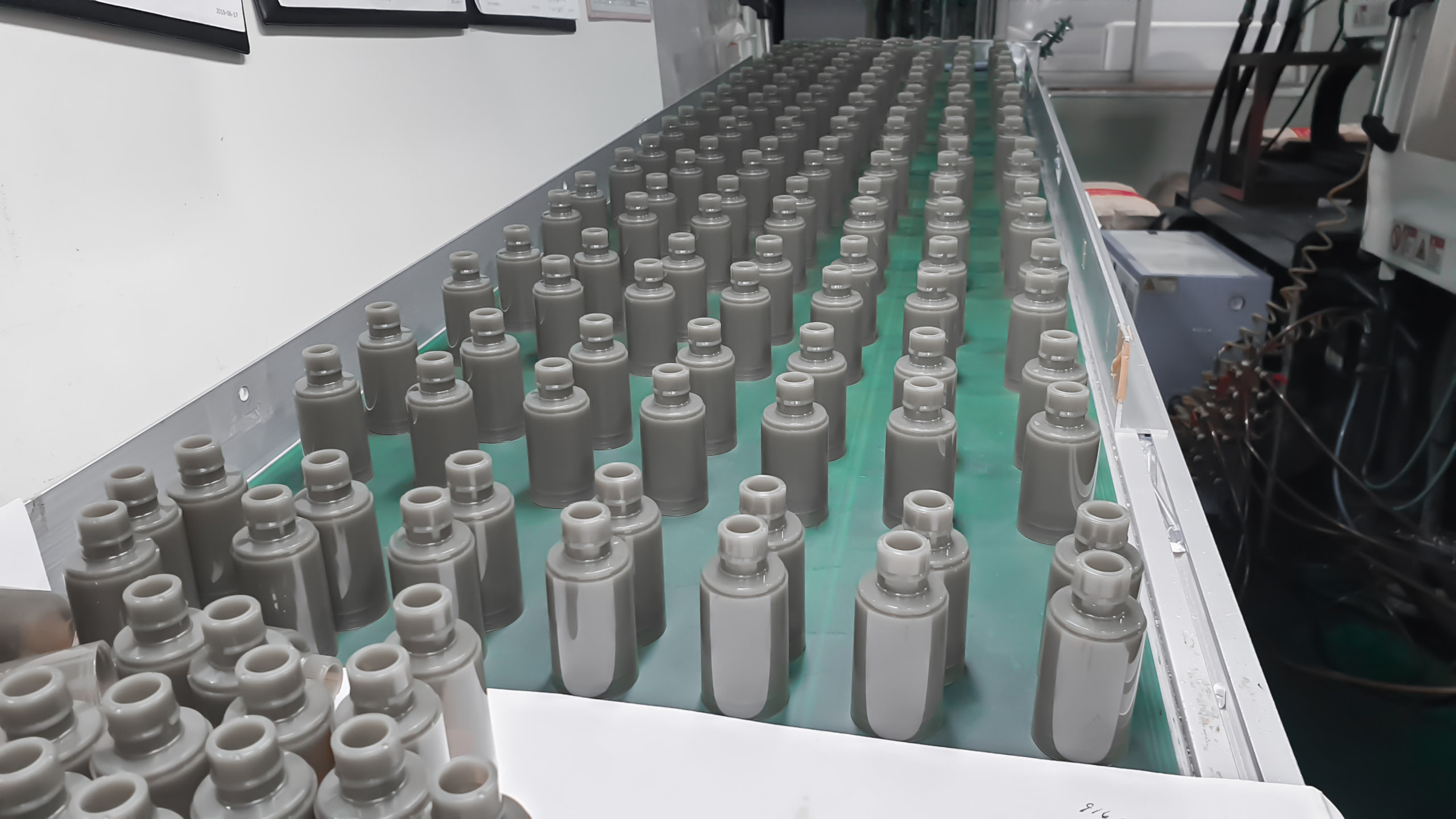
At China Manufacturing parts, we have the resources, know-how, and manufacturing network to deliver the plastic injection molding products that you need. Learn more about our injection molding services and create an account to get a quote today.