Time to read: 5 min
Injection molding design mistakes can cost you time and money. If there’s a problem with the design of your injection mold, you may need to modify or discard your tooling. And that means paying for and waiting for a replacement tool – which will delay the start of production accordingly. Plus, if there’s a problem with the design of your mold, the parts it produces could have defects that result in costly material waste and time-consuming rework.
Fortunately, most design problems with injection molds and injection molded parts are preventable. Although there are some common mistakes in injection molding design, there are also proven solutions. China Manufacturing parts, Inc. can help you with both your mold designs and your part designs to accelerate new product introduction (NPI) and get great injection molding results every time.
Injection Molding Design Mistakes
There are five common mistakes with injection mold design:
1. Choosing the wrong mold material
2. Incorrect parting line placement
3. Inadequate venting
4. Gate problems
5. Cooling channel problems
#1 Choosing the wrong mold material
Injection molds are usually made of either aluminum or steel. Hardened steel lasts longer than aluminum, but some designers think that steel molds are cost-prohibitive. With China Manufacturing parts, however, you can get hardened steel molds that are affordable. Plus, steel molds produce much higher volumes of parts than aluminum molds, which reduces the cost per part over time. Steel molds are also better at supporting more complex part features.
#2 Incorrect parting line placement
The parting line is where the two halves of the mold meet. For best results, parting lines should be paced on sharp, straight edges. Otherwise, molten material may escape and produce flash, or flashing. Also, it’s a good idea to locate the mold parting line so that it splits the draft (the angle applied to part faces to facilitate clean part ejection from a mold). If you place the parting line without considering the draft, scraping during ejection could damage the part.
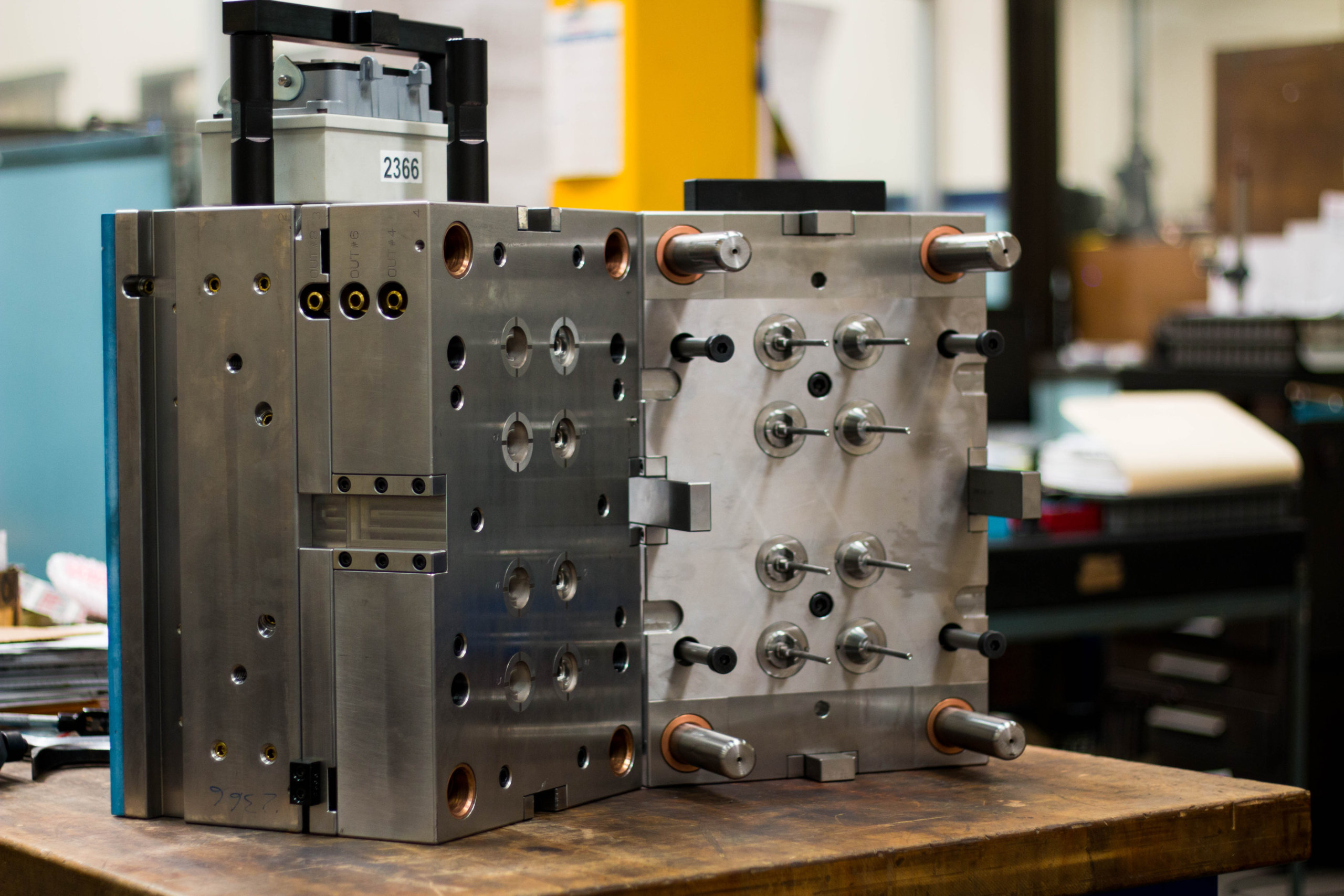
#3 Inadequate venting
Air vents near the mold’s parting line enable air to escape as material fills the mold. As a rule of thumb, always vent at the end of the fill location. If there aren’t enough vents, or if vents are in the wrong places, air can pool and compress in pockets, then ignite, burn and discolor parts as they’re formed. Inadequate venting can also produce flow lines, wavy lines, streaks, or patterns.
#4 Gate problems
Injection molding gates slow the incoming molten material and regulate its flow as it enters different parts of a mold. If the gates are too small, parts may exhibit “gate blush,” a circular or halo-like pattern. Gates that are too small can also cause the uneven flow of material or result in knit lines, blemishes that occur where two resin flows meet. A mold with too few gates is susceptible to cooling problems, but a mold with too many gates introduces avoidable points of failure. Lastly, using the wrong type of gate, such as a tab gate for a thick profile instead of a thin one, can also cause problems.
#5 Cooling channel problems
Cooling channels circulate coolant throughout a mold so that injected molded parts can cool properly before the mold opens. As a rule, cooling channels should be as close as possible to the mold’s interior space. Avoid cooling channel dead-ends that form air traps, and use larger cooling channels with thicker walls. Poor cooling channel design can lead to sink, or depressions in the surface of a molded part that occur when different areas of a part cool at different rates.
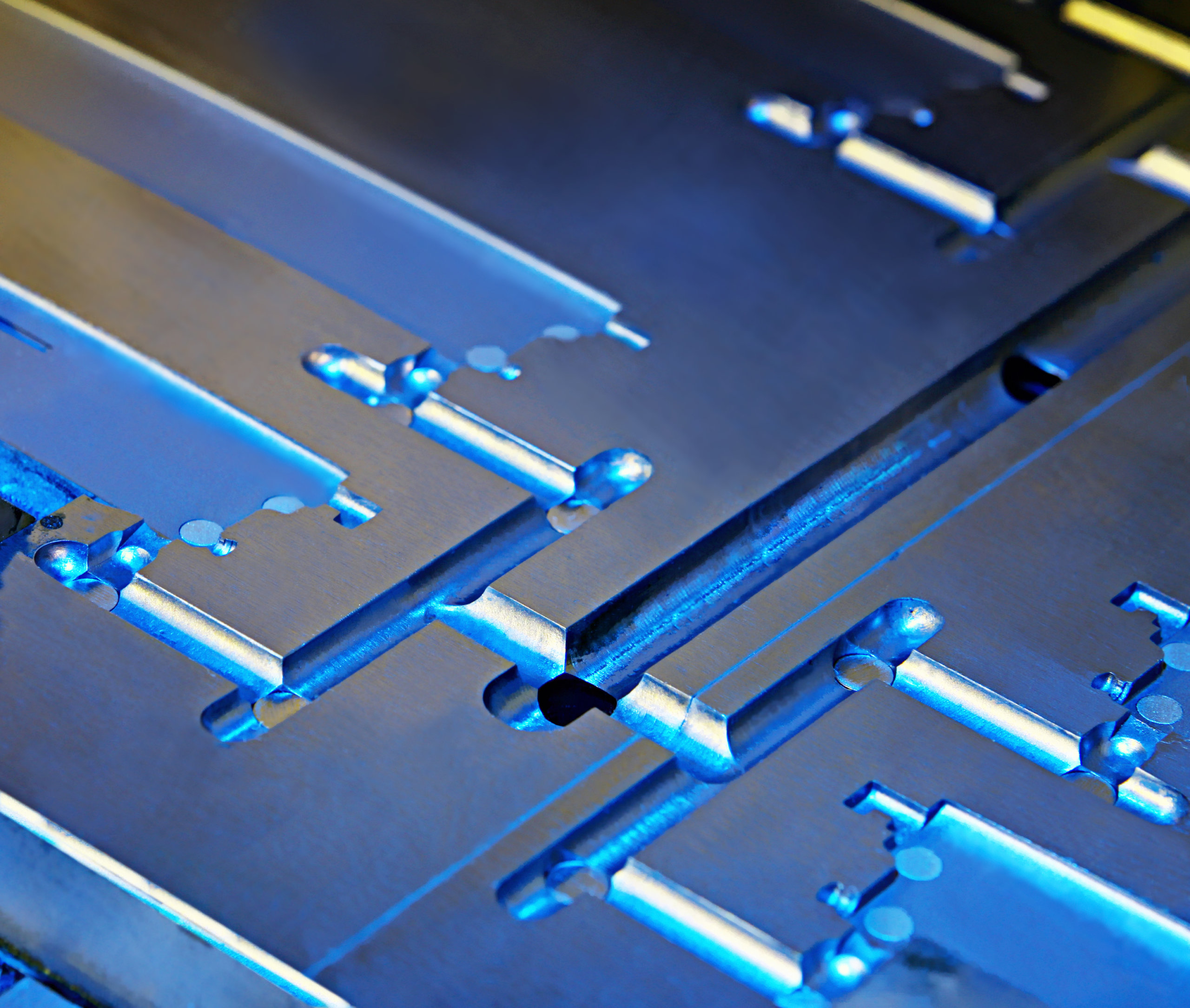
Injection Molding Part Design Mistakes
There are five common mistakes with injection mold part design.
1. Choosing the wrong part material
2. Using the wrong wall thickness
3. Inadequate draft
4. Problems with sharp corners and radii
5. Unnecessary undercuts
#1 Choosing the wrong part material
Most part designers know that there are many different types of injection molding plastics, and that the choice of a plastic material can determine the success or failure of a project. Yet, polymer selection isn’t just about material properties. It’s also about the interaction between properties, part design, and manufacturability. For example, a fiber-reinforced plastic might seem like a good choice for a C-shaped part that needs added strength, but fiber-reinforced materials don’t shrink uniformly, and can warp as they cool.
#2 Using the wrong wall thickness
Different materials have different wall thickness recommendations. For example, the recommended wall thickness for polyurethane (0.080” to 0.750”) is twice that of polycarbonate (0.040” to 0.150”). With thicker walls, you may have excessive mold shrinkage, internal voids, molded-in stresses, and post-molding warpage.
And walls with a non-uniform thickness are problematic because thinner areas tend to warp and thicker areas tend to shrink. So, if you need to design thinner walls in places, make them no less than 40% to 60% of the width of the adjacent walls.
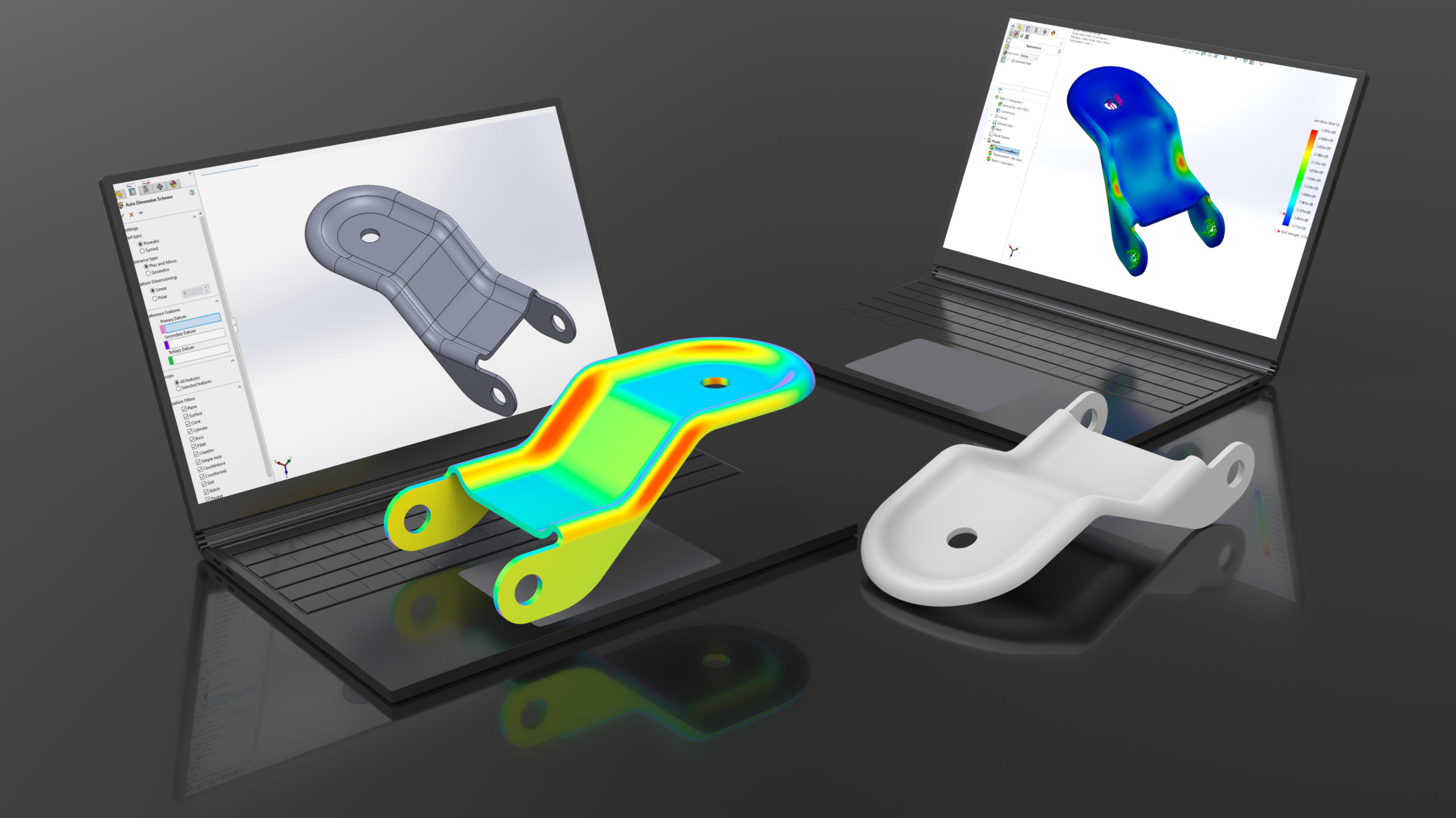
#3 Inadequate draft
Plastic parts that don’t have enough draft won’t eject smoothly from a mold. The problem isn’t just with the mold, however. If the part design doesn’t have enough draft, the mold design won’t either. As a rule of thumb, apply 1° degree of draft for every 1” of depth in the mold cavity. Also, apply the draft at an offset angle that is parallel to where the mold will open and close.
#4 Problems with sharp corners and radii
Sharp corners increase stress concentrations, which can lead to part failure. These corners don’t always look like the edges of a rectangle, however, since bosses and ribs can create sharp corners, too. If your design needs sharp corners, then apply radii to reduce stress concentrations and fractures, but avoid adding radii around the parting line — otherwise, your parts may exhibit flash and minor undercuts.
#5 Unnecessary undercuts
Undercuts are recessed features that provide a fastening point or locating edge. Though undercuts make it harder to eject an injection molded part, China Manufacturing parts, Inc. can support undercuts if you need them. For simpler and more cost-effective tooling, however, part designers should avoid unnecessary undercuts. During the design for manufacturing (DFM) review, China Manufacturing parts, Inc. can help you to explore alternatives to these part features.
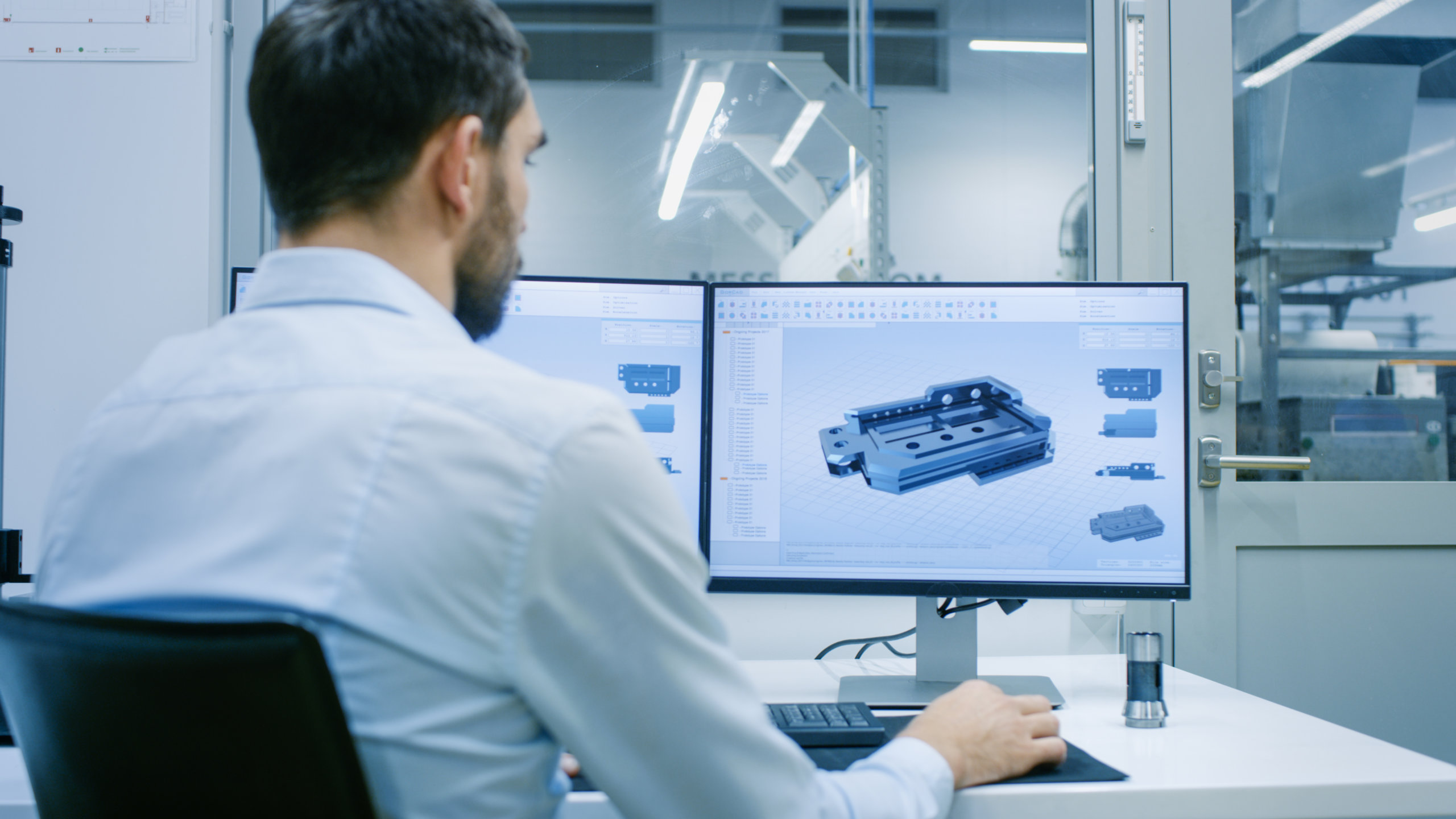
Avoid Common Mistakes in Injection Molding Design
These are just some common mistakes – and they aren’t the only injection molding design flaws that can cost you time and money. For example, during the injection molding process itself, a machine with an injector that works too quickly or that doesn’t apply enough clamping pressure can produce part defects. Even if you design your mold perfectly and your parts flawlessly, a poorly machined mold can also contribute to defects.
China Manufacturing parts can help you to avoid common mistakes in injection molding design – and we know how to avoid the uncommon ones, too. With our resources, knowledge, experience, and production network, we can deliver the quality parts that you need every time. To get started, create an account and request a quote.