Time to read: 8 min
Why Monte Carlo?
The Monte Carlo method is an extremely powerful computational technique in any mechanical engineer’s toolkit. There are a number of common use cases in mechanical engineering to which Monte Carlo simulation naturally applies, including:
- Statistical tolerance analysis
- Reliability design
- Uncertainty analysis in measurement
- Robotic error, position, and attitude analysis
- Design optimization
In this article, we will be focusing on building an understanding of the methodology, establishing a framework for analysis that can apply to a variety of problems, and applying this framework to a common statistical tolerance analysis problem that mechanical engineers are likely to face often.
Method Overview
The fundamental concept with Monte Carlo methods is to use randomness to solve deterministic problems. For example, if I roll three six-sided dice how often will the sum of the dice be greater than seven? The problem itself is deterministic, meaning it has one and only one answer. Dice behave the same way no matter where they are rolled and who rolls them. And yet, there is an element of randomness as well. You cannot predict what any individual die will land on before you roll it.
However, it is quite easy to see the result of a single dice roll and check against the condition we laid out in our problem statement (do they add up to more than seven?).
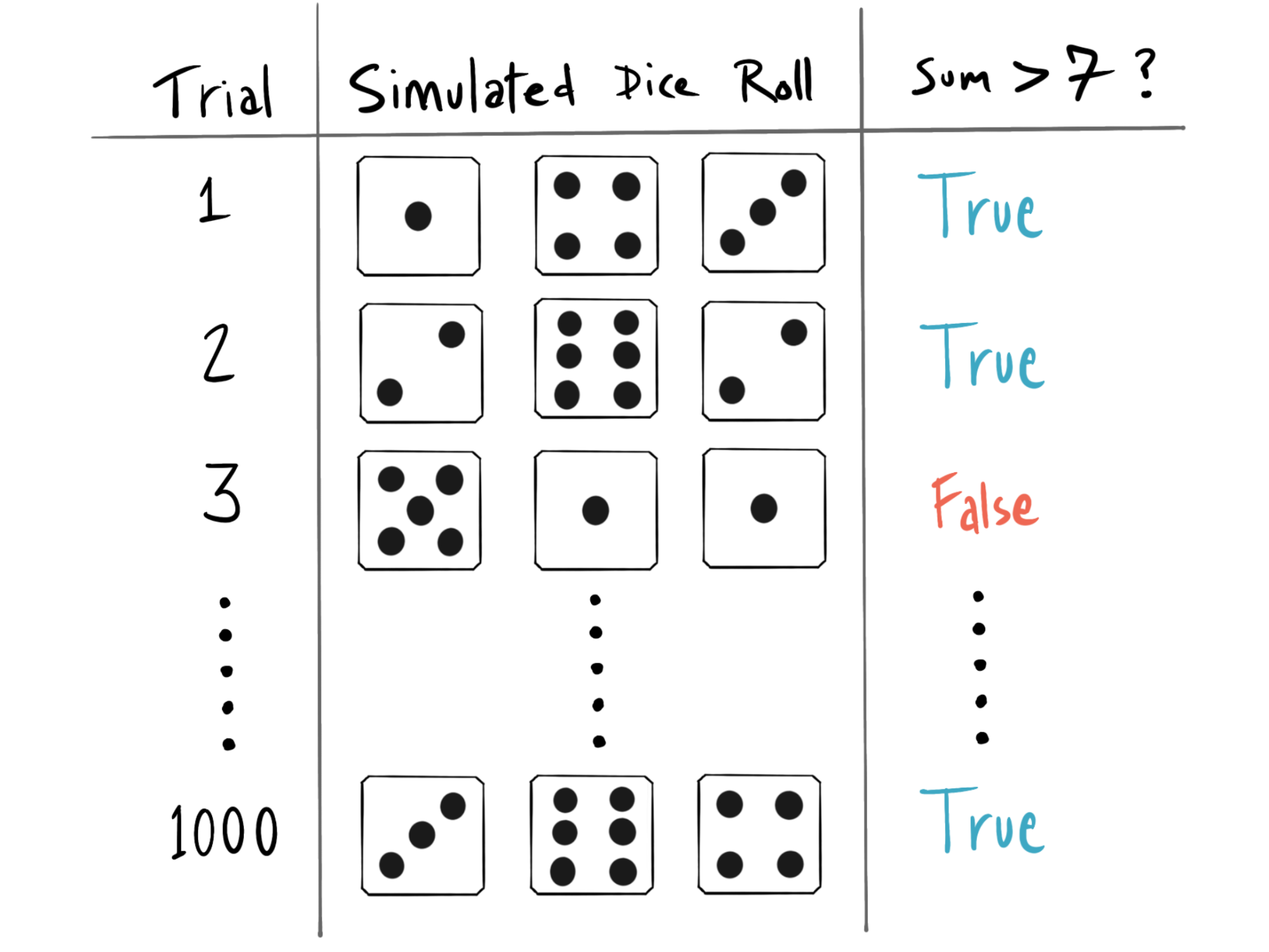
That’s the beauty and power of the Monte Carlo method. There are many problems where computing the answer directly is extremely difficult, but checking if the outcome of an “experiment” (in this case a dice roll) is trivial. The method relies on conducting a sufficiently large number of experiments or trials, such that counting the outcome of each trial tells us the answer to the original question in a general sense.
Analysis Framework Fundamentals
The probability density function (PDF) is a core component of any Monte Carlo simulation. A PDF completely describes the behavior of any random variable that is being simulated. In the dice roll example the PDF is easy to understand. When you roll a single die, there is an equal (⅙) chance of any number being rolled. This uniform probability density function is plotted below.
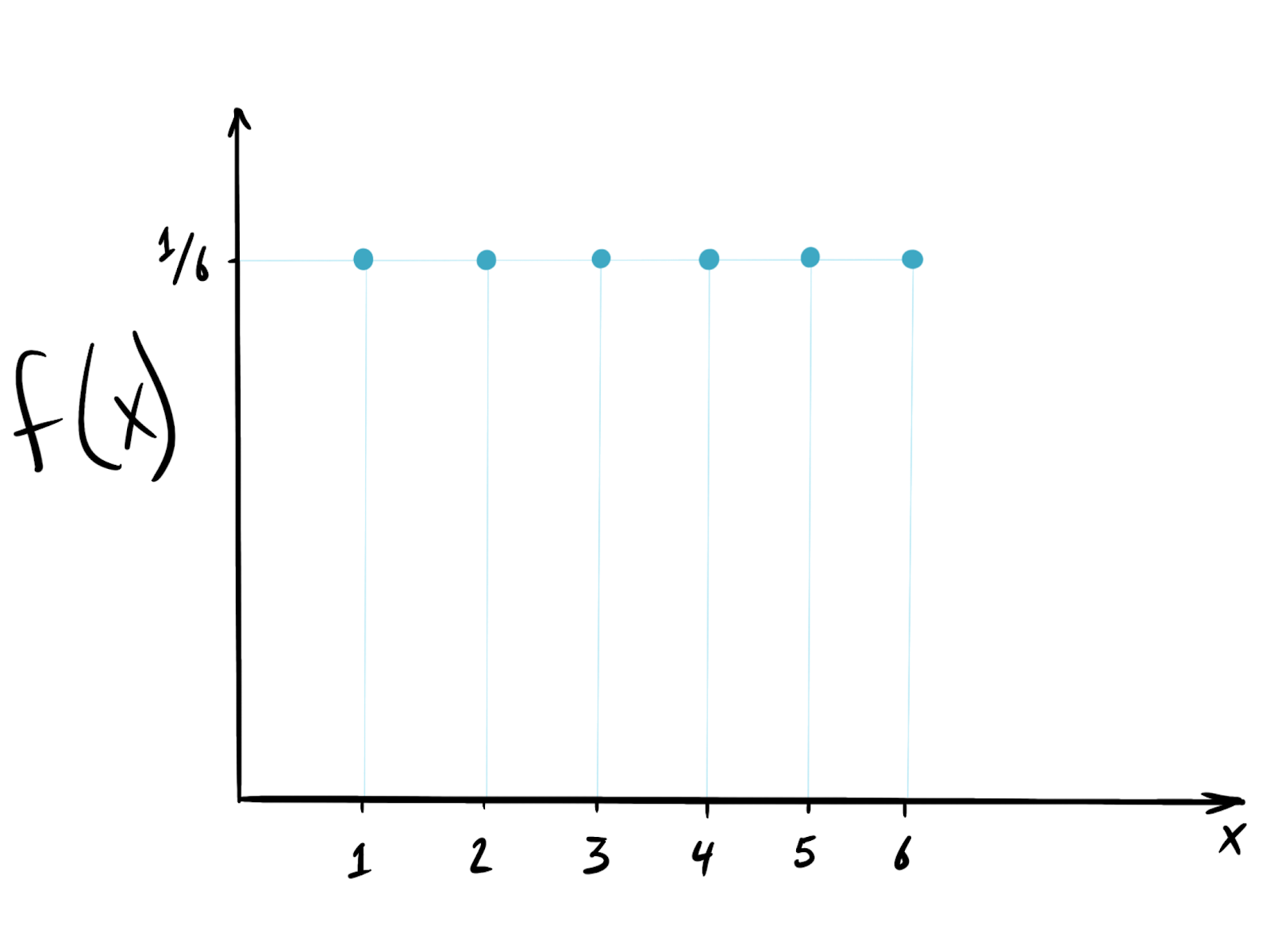
In order to construct a useful Monte Carlo simulation, you must use a representative PDF that accurately captures the behavior of each trial in the real world. Unlike dice, the dimensions of mechanical parts and other engineering processes exhibit continuous variability. With continuous random variables, there are an infinite number of values possible even within a finite range. Accordingly, you need a function such as a Gaussian (or normal) distribution to accurately represent continuous random variables.
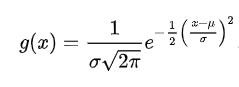
The exact PDF necessary for your analysis depends on the phenomenon you are trying to represent and may require some other distribution besides Gaussian (ex: power law, Weibull, Bernouilli, Binomial etc…)
Analysis Framework
Now that we understand the core component of a trial (the probability density function) we can build an analysis framework around it. There are five steps in the framework outlined below. These steps will be explained using pseudocode, as well as particular references to Google Sheets, MATLAB and python functions you can use in your own applications. You can construct a useful simulation in spreadsheets or with your programming language of choice as long as you understand the framework and apply it accurately.
- Construct PDFs. Represent all variables as probability density functions, either discrete or continuous. (ex: multiple normal distributions each with their own independent mean and standard deviation values)
- Construct functions to sample from these distributions. In google sheets you can use the NORMINV() function combined with RAND() for random sampling. In python you can use the np.random.normal from the numpy package.
- Construct a trial check function. This function looks at an individual simulation trial and checks the results of that trial against some deterministic outcome. For example, is the sum of the three dice greater than seven (true or false)? This function (or functions) should aggregate and store your individual trial’s results for later use. In excel or g-sheets this usually means constructing a trial results column. In python or MATLAB you should construct a list, tuple, or array (or other data structure) where you store the trial results.
- Construct a simulation results check function. This function poses your engineering question in such a way that it can be answered by running some computation on the individual trial results. This is where your creativity really comes into play, and it is also where the flexibility and power of the method comes alive. Coming up with creative ways to relate the aggregate trial data to engineering problems is what allows this method to work in so many domains.
- Construct the main simulation using the following pseudo code as a guide.
# For each trial (main simulation loop) # sample from the relevant probability distribution functions # check the samples using your trial check function(s) # store the results of each trial check # Run the simulation results check function to compute your simulation results
Note: There are numerous other simulation frameworks that you can use for Monte Carlo simulation. Some simple simulations benefit from running the results check function inside the main simulation loop, incrementing results variables after each trial. The suitability of one framework over the other depends on the nature and complexity of the problem being solved and your personal preference.
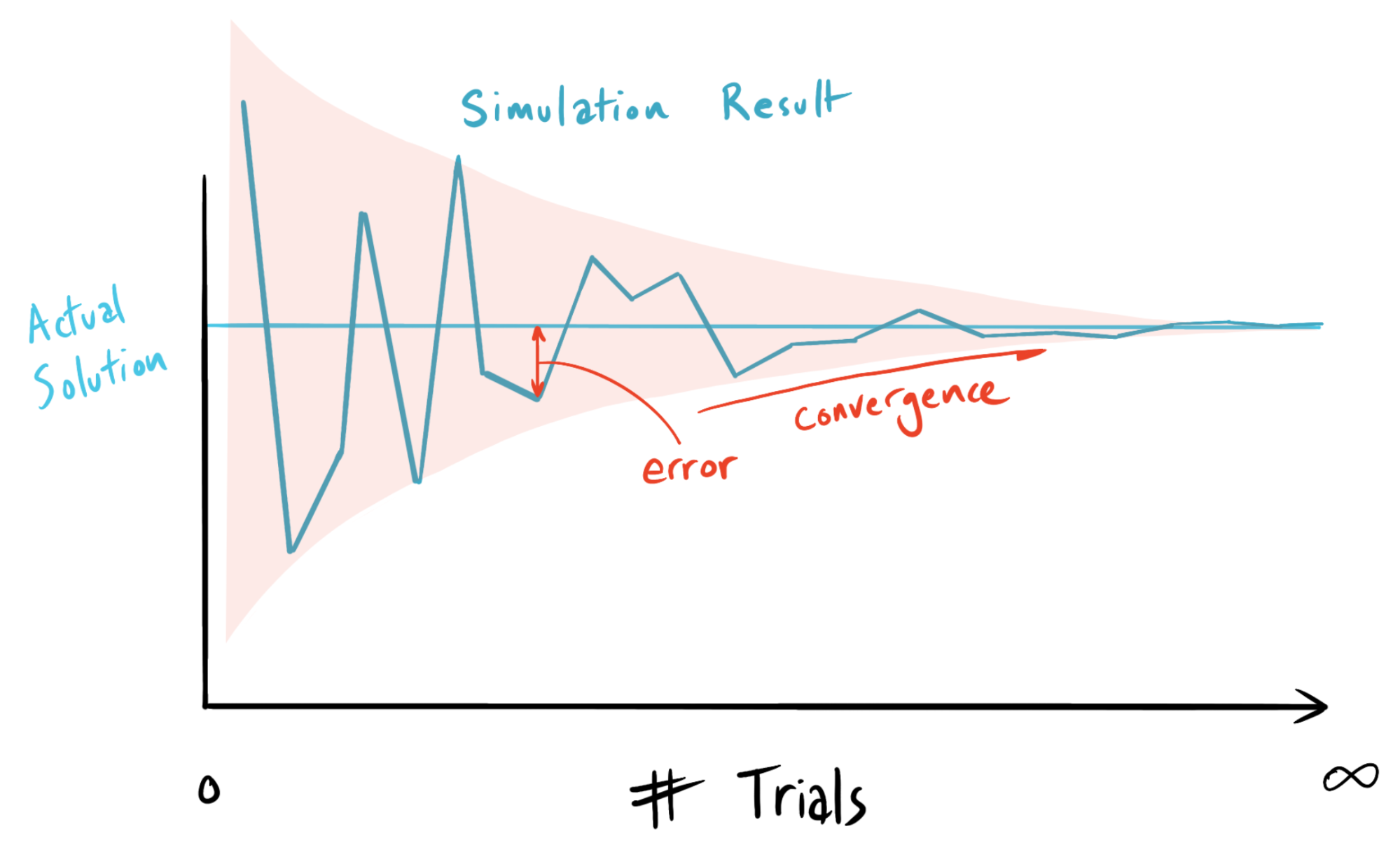
Tolerance Analysis Example: O-ring compression problem
Suppose we are designing a hydraulic piston and cylinder actuator that uses buna-n O-rings to seal around the piston (see schematic below).
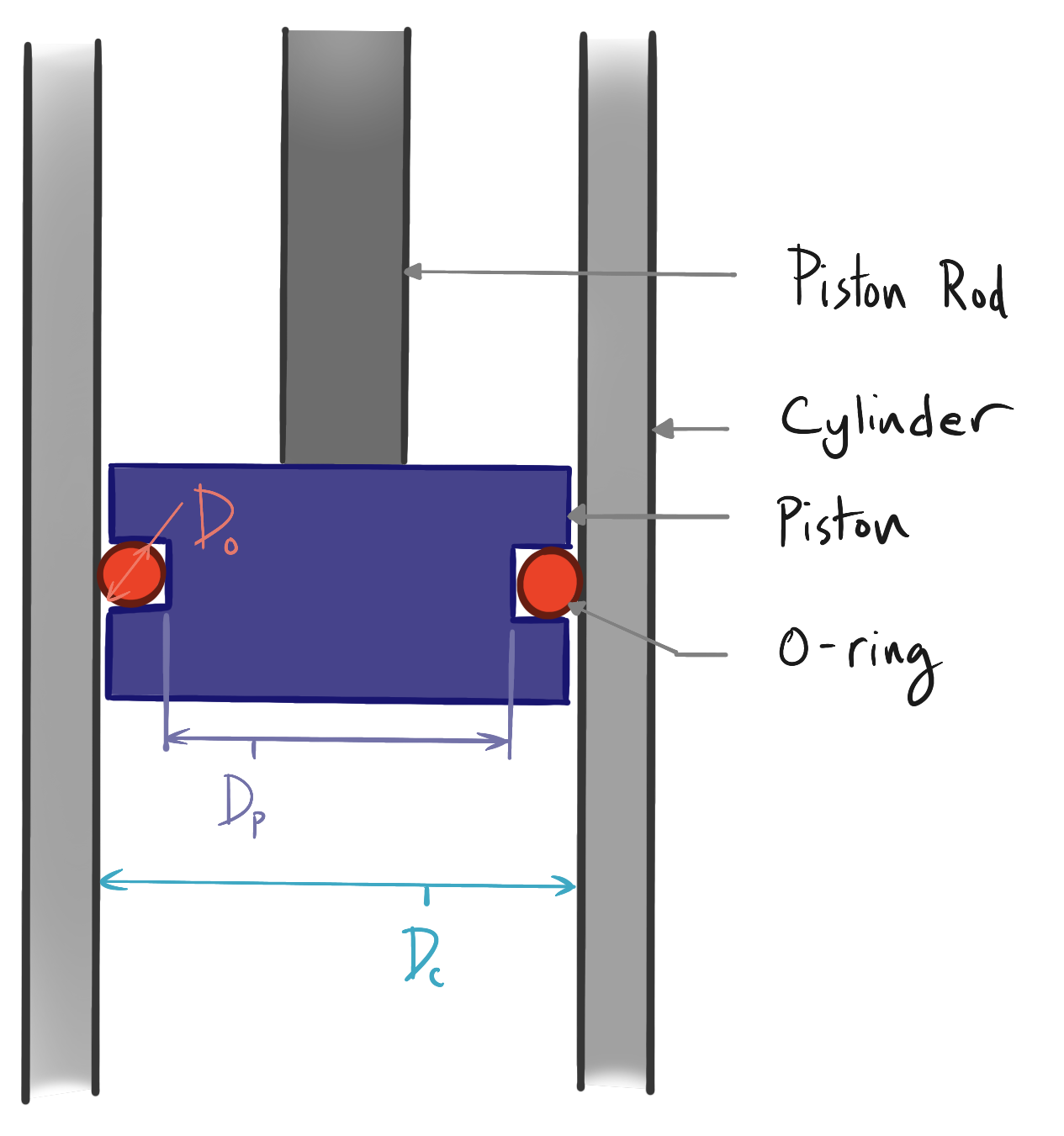
The O-ring is designed to work in a certain interference (compression) range which we will call X. The cylinder, piston and O-ring have the following dimensions and manufacturing tolerances.
O-ring diameter = 3mm ±0.09 mm = DO
Cylinder inner diameter = 25mm ±0.1 mm = DC
Piston ring groove diameter =22.5mm ±0.03 mm = DP
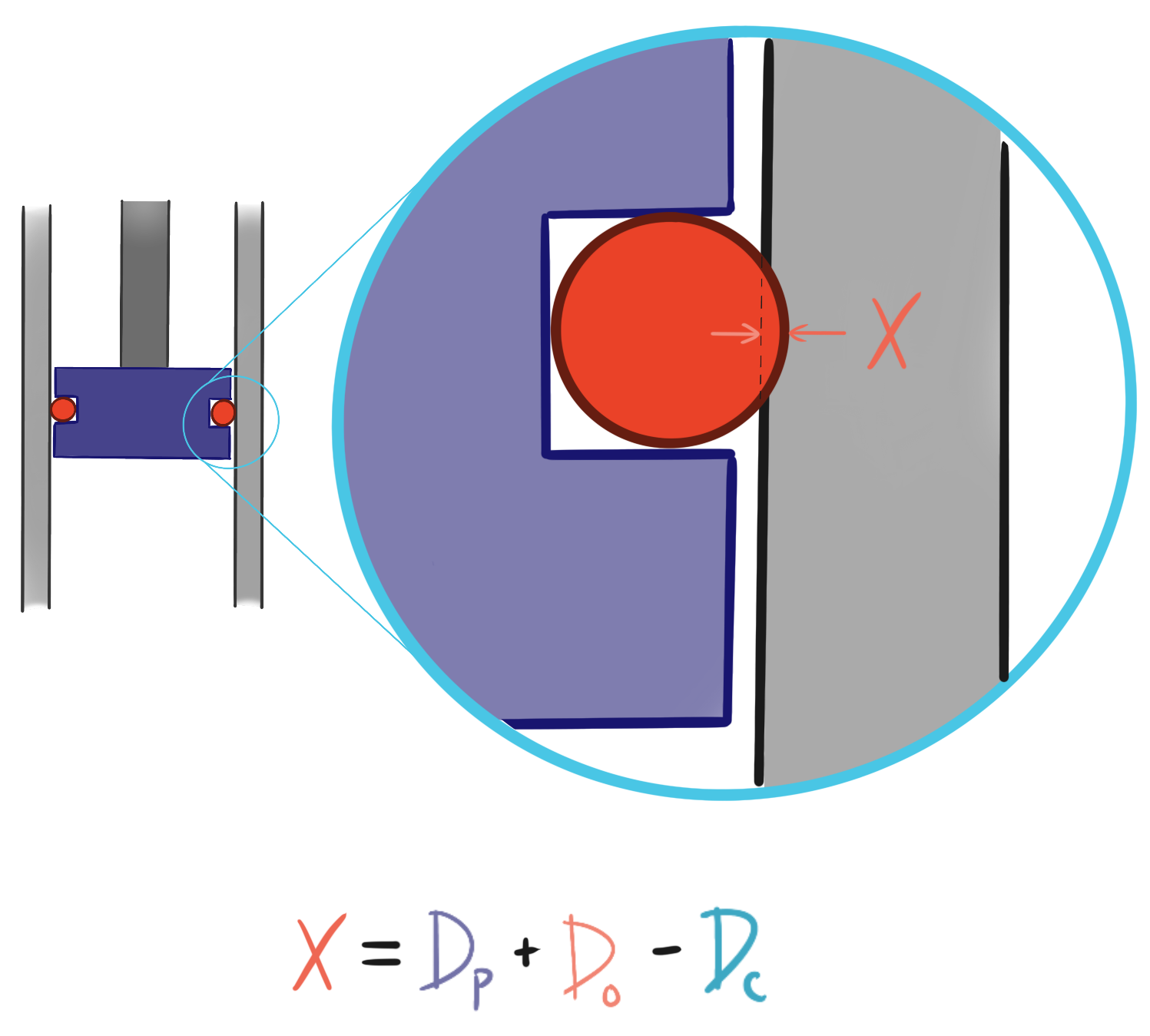
In order for the piston seal to function properly, the O-ring compression must remain between 0.3mm and 0.6mm. With the above manufacturing tolerances, what percentage of actuators will not be functional?
Solution
Using our analysis framework we must first choose a PDF to represent each machining process and critical dimension of the assembly. We will use a normal distribution where the mean is the target dimension, and the standard deviation is derived from the specified machining tolerances. A common assumption with these types of tolerancing problems is that the tolerance specified in design is achieved on 99.7% of parts, or a three standard deviation (sigma) coverage.
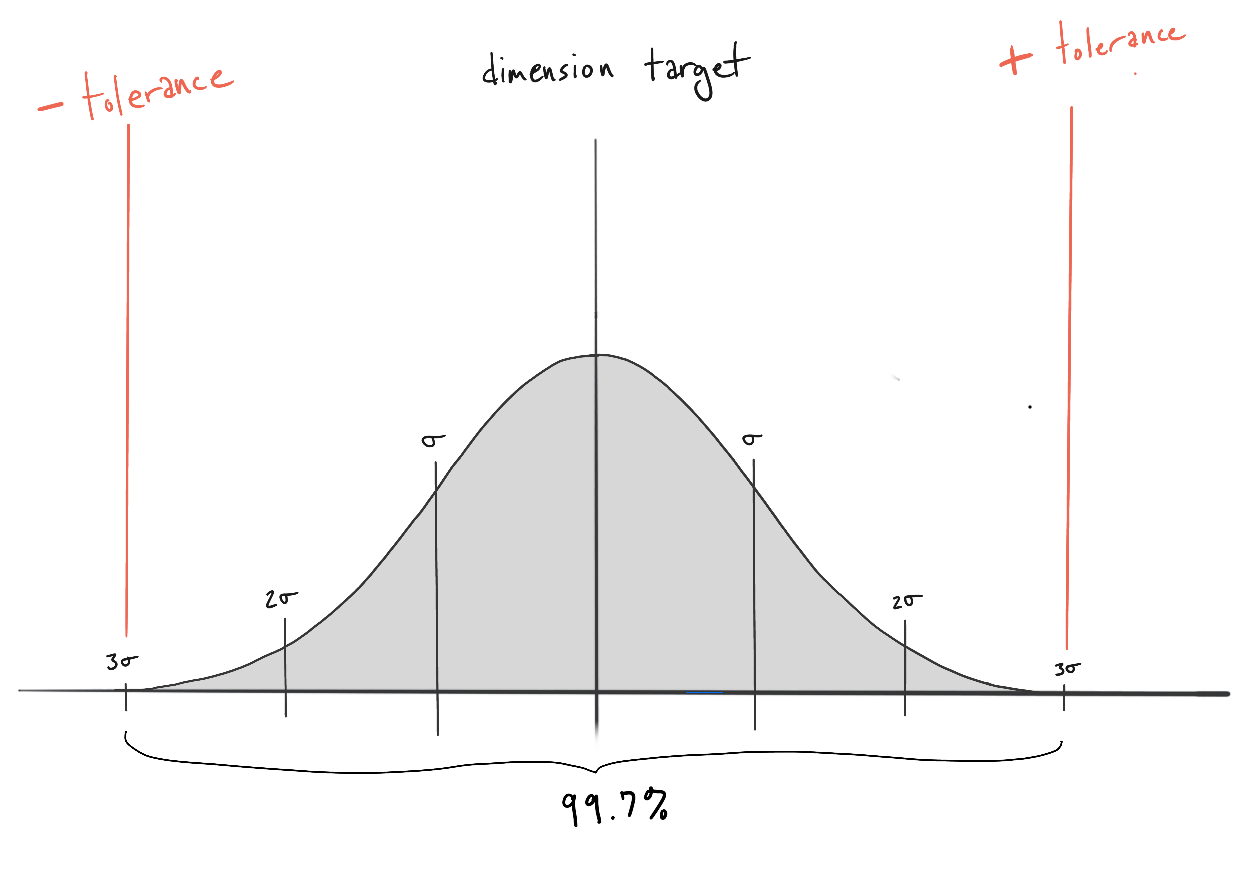
After choosing our PDFs for each dimension in the tolerance stack, we will then sample each distribution to “build an assembly” for each simulation trial. Finally we will check each assembly against our functional O-ring specification and aggregate the results. To see the Python code expand the section below.
Python Example Code
import numpy as np
import matplotlib.pyplot as plt
n = 1000000 # number of trials
# Component specifications
sigma = 3 # assume 99.7% of components in tolerance spec
dp = 22.5 # piston diameter
tol_dp = 0.03 # piston diameter tolerance
do = 3 # o ring diameter
tol_do = 0.09 # o ring diameter tolerance
dc = 25 # cylinder diameter
tol_dc = 0.1 # cylinder diameter tolerance
def calculateInterference(dp, do, dc):
"""
in: diameters
out: o ring interference
"""
interference = dp + do - dc
return interference
def checkInterference(interference, lower, upper):
"""
in: o ring interference
out: Bool, T for pass, F for fail
"""
if interference < lower or interference > upper:
return False
else:
return True
# set interference limits
lower = 0.3 # smallest permissible interference
upper = 0.6 # largest permissible interference
interference_list = [] # initialize a list to store interference values per trial
results = [] # initialize a list to store our trial results
# Main simulation loop
for trial in range(n):
# Sample PDF for each component
piston_sample = np.random.normal(dp, tol_dp/sigma)
oring_sample = np.random.normal(do, tol_do/sigma)
cylinder_sample = np.random.normal(dc, tol_dc/sigma)
# compute and store interference
interference = calculateInterference(piston_sample, oring_sample, cylinder_sample)
interference_list.append(interference)
# Trial check: log results of interference check
results.append(checkInterference(interference, lower, upper))
# results check
goodAssemblyCount = sum(results)
failurePercentage = 100*((n - goodAssemblyCount) / n)
print('Percentage of failed piston assemblies: ', failurePercentage, "%")
Our one million trial simulation shows a piston assembly failure percentage of 1.4738 %.
However, we don’t know the distribution of failures or how we might modify our design to prevent these failures. To visualize the distribution of O-ring interference, we can plot a histogram of our simulation data with the following python code.
Python Example Code
# Plot results
#setup histogram parameters for plotting
n_bins = 500
heights, bins, _ = plt.hist(interference_list, bins=n_bins) # get positions and heights of bars
bin_width = np.diff(bins)[0]
bin_pos = bins[:-1] + bin_width / 2
# mask for coloring failures differently
maskleft = (bin_pos <= lower)
maskright = (bin_pos >= upper)
# plot data in three steps
plt.figure(figsize=(14, 4))
plt.bar(bin_pos, heights, width=bin_width, color='#281E78', label='Good Assemblies')
plt.bar(bin_pos[maskleft], heights[maskleft], width=bin_width, color='#ea4228', label='left tail failures')
plt.bar(bin_pos[maskright], heights[maskright], width=bin_width, color='#49C6E5', label='right tail failures')
# axis labels and vertical markers of left and right tail failures
plt.xlabel("O ring interference (mm)")
plt.ylabel("# samples")
plt.axvline(lower, linestyle='--',linewidth=1, color='grey')
plt.axvline(upper, linestyle='--',linewidth=1, color='grey')
# remove upper and right spines, set ticks
ax = plt.gca()
ax.spines['right'].set_visible(False)
ax.spines['top'].set_visible(False)
ax.xaxis.set_ticks_position('bottom')
ax.yaxis.set_ticks_position('left')
plt.legend()
plt.show()
The histogram of O-ring interference shows that all failures are happening on the right tail of the distribution, meaning there is too much interference.
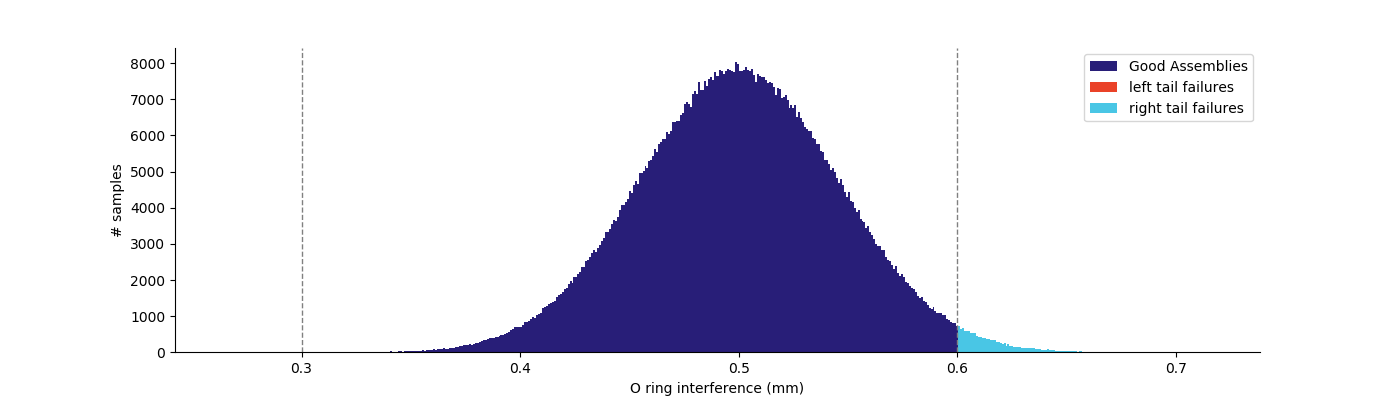
Given that there is room on the left tail of the distribution, a simple fix is to adjust one of the dimensions in the stackup to shift the assembly distribution left. We can simulate this by reducing the piston ring groove diameter from 22.5mm to 22.45mm, while keeping all tolerances the same. Simulating this condition reduces failure to 0.1118% by centering the O-ring interference distribution between the left and right tail cutoffs. This is visualized below
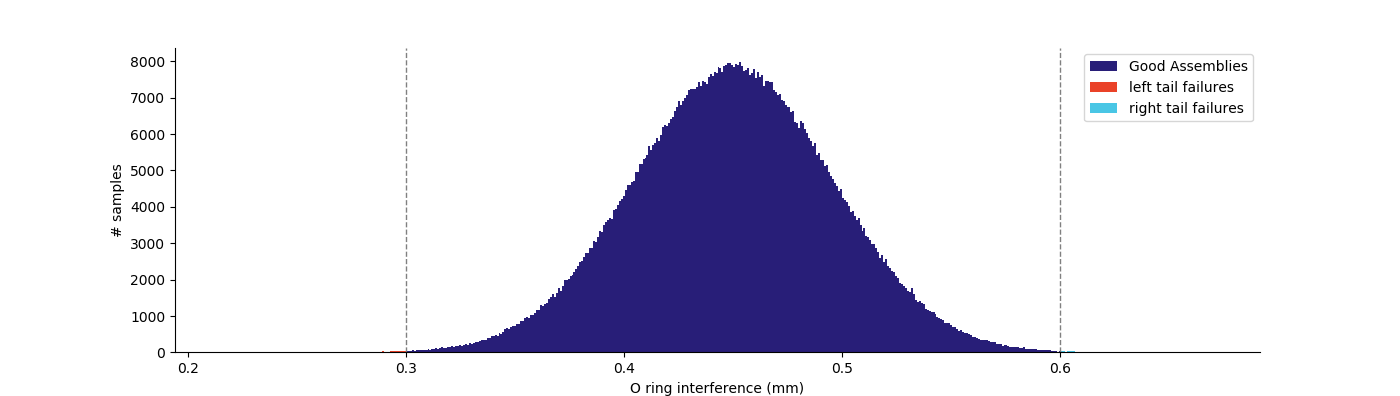
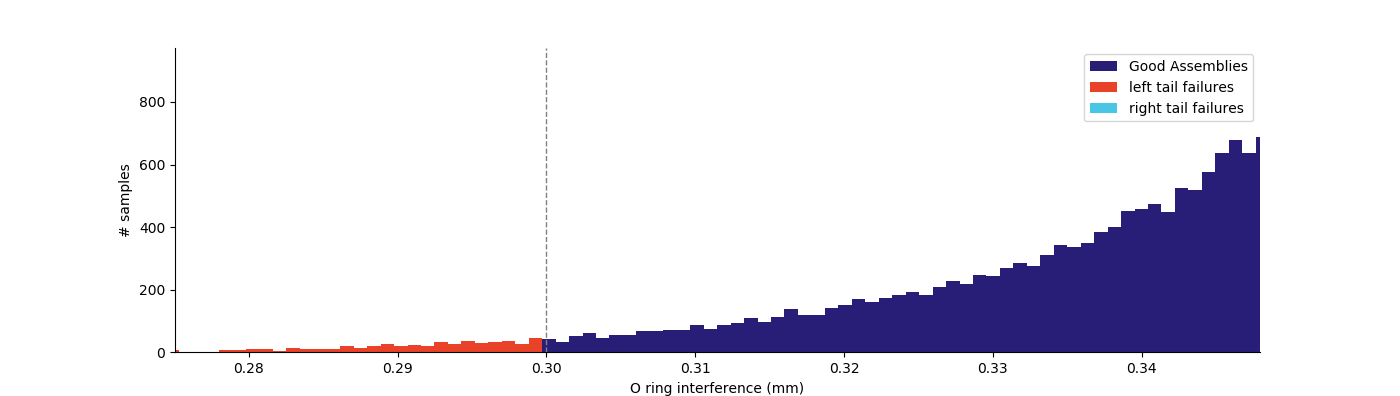
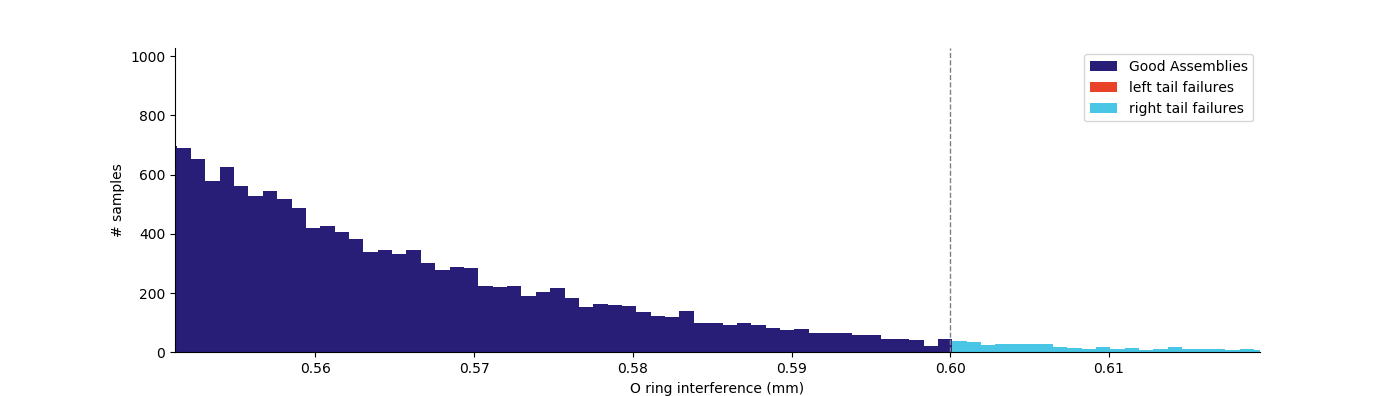
Takeaways
The main thing we hope you take away from this post is that the Monte Carlo method is not difficult to implement and can be incredibly flexible and useful for a variety of common mechanical engineering problems. Understanding the basic framework allows you to quickly create useful simulations in spreadsheets or python code in just a few minutes. When assessing the accuracy of your simulations it is important to remember these key facts:
- The probability density functions you must be representative of the actual system behavior in the real world.
- The samples you draw from the probability density functions must actually be random samples, otherwise your models will not represent the population accurately.
- The law of large numbers dictates that as sample (trial) count increases, model accuracy increases.
- For models that require highly accurate answers, trial count should be increased until the accuracy of the simulation no longer changes. Checking convergence does not guarantee that the model is accurate, but it does yield efficient results by allowing you to balance the cost of computation against marginal increases in model accuracy.