Time to read: 4 min
One of the greatest challenges hardware teams face is in figuring out how to approach low volume production at awkward volumes of 100 – 1,000 units, before scaling to manufacture tens of thousands of units. In part 1 of this series, we covered best practices for manufacturing field testing units or made-to-engineer products at low volumes of 10-100 units.
In this article, we offer tips on how to efficiently and economically approach production at volumes of 100-1,000 units.
Bridging the Gap: How to Economically Manufacture 100 – 1,000 Units
If you’re looking to produce 100-1,000 units, this is likely a batch of finished goods being sold to real customers, which could be a first generation product in a pilot market or a slow-moving, low-volume product.
Slow-moving products, such as customized industrial hardware, can benefit from just-in-time assembly commonly done in-house, which allows for greater customization.
The challenge here is that 100-1,000 units can be an awkward volume to source; it’s too slow and expensive for prototyping methods like urethane casting, but not quite large enough to effectively amortize the high cost of hard tooling.
Minimize Custom Components
Since tooling can be a significant cost, we recommend minimizing the number of unique custom-designed components. Spend your dollars on cosmetic and critical components, and economize internal, non-critical components.
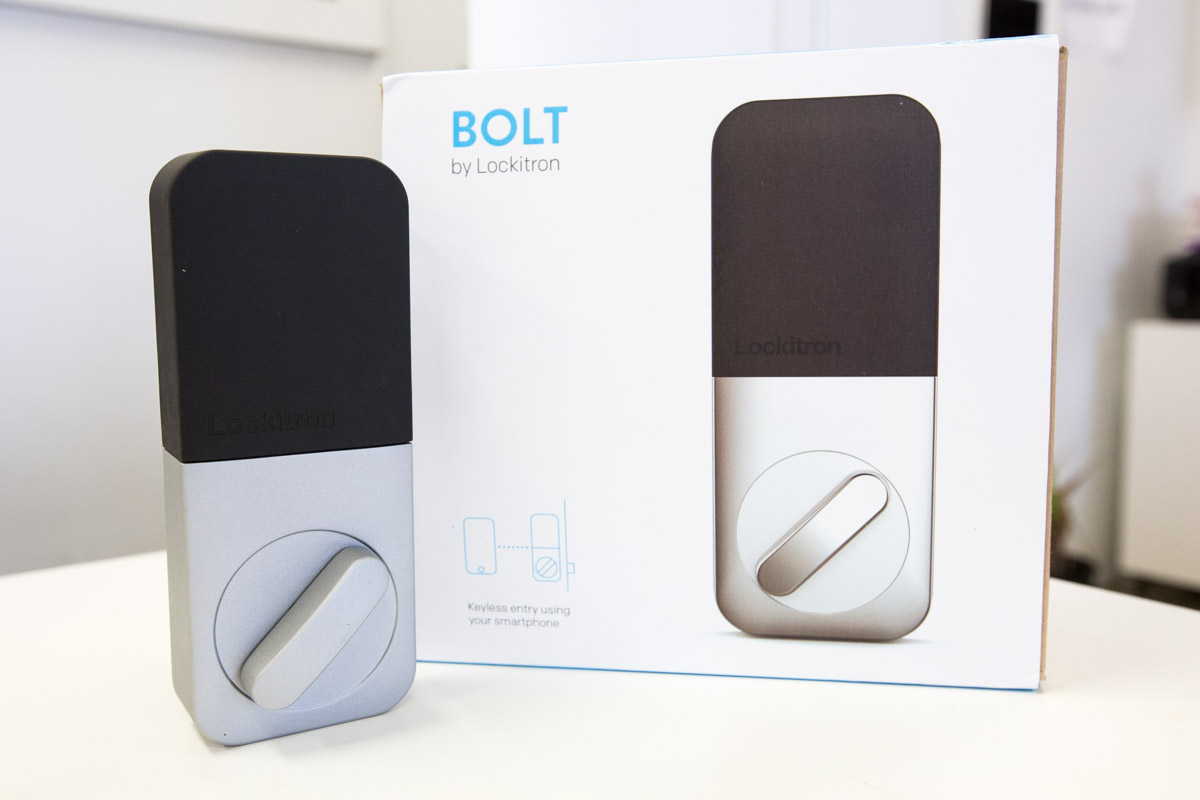
To avoid the high upfront cost of tooling, you should use off-the-shelf components wherever possible and explore alternative manufacturing methods that won’t incur high upfront cost. For example, instead of die cutting a foam gasket or molding a silicone gasket, consider laser-cutting them.
A Development Partner is Key
Choosing the right manufacturing partner is critical to manufacturing 100-1,000 units economically. We find that working with small, flexible manufacturers with low overhead is key to efficient, economical manufacturing at low volumes.
If your order size matches what the manufacturer handles typically, you can at least have confidence that your order will not be deprioritized. Low-volume manufacturers also tend to have shorter frozen periods of production, which means they will be more responsive. The trade off can be less stringent internal processes, which means you may need to be more hands on with quality assurance and project management.
At Fictiv, we vet and manage a large network of high quality, low volume manufacturers. We also have stringent in-house quality assurance and logistics processes, so you can continue to focus on getting your technology to market quickly, while we partner with you to handle the fabrication logistics. Send us an email if you’re looking to manufacture volumes of 100-1,000 units so we can provide you with a custom quote.
Tips to Minimize Costs for Plastic Injection Molding at Low Volumes
When most people think of mass-produced plastic components prevalent in consumer goods, they’re thinking of injection molded parts. Injection molding tooling costs start in the low thousands per mold, which is amortized over its production life.
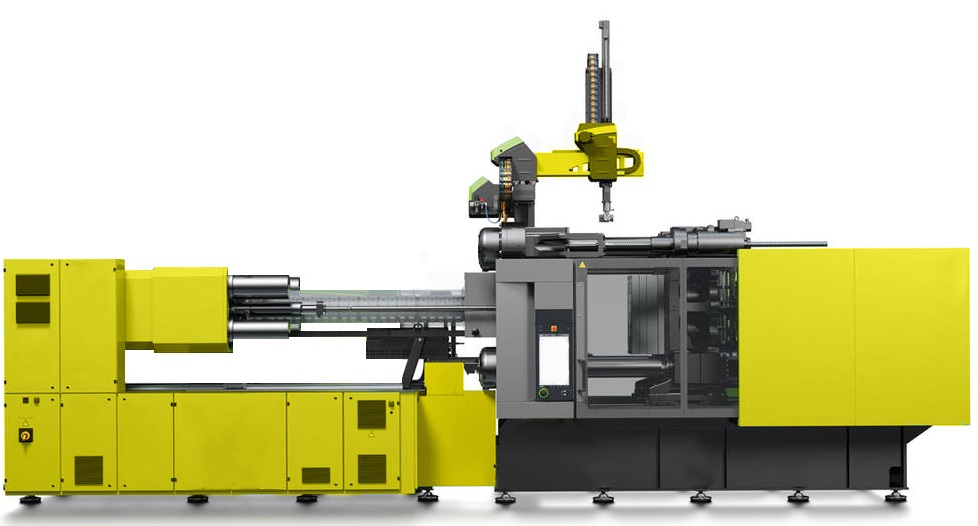
As mentioned above, it’s key to keep the tool simple to minimize part cost at lower volumes. We recommend you minimize the number of side actions (requiring sliders and lifters) and avoid specialized molds, such as collapsible core and two-shot molds. Also be realistic about cosmetic standards: High gloss is much more expensive than a standard matte look, especially for large parts.
Injection molding costs and tooling lead time can vary greatly from vendor to vendor, even for the same design. A few factors determine this, including:
- Tool base metal (aluminum, P20 steel, etc.)
- Manual vs. automatic sliders
- Cold vs. hot runners
- Use of cooling lines
All of these factors will impact the quality of the part, especially cosmetic. Manufacturing is really a game of tradeoffs, mostly between “quality” and cost.
The fastest and most basic injection molding tool will be made out of aluminum, using manual sliders, cold runners, and not incorporating cooling lines. This is very much meant to be a quick-turn prototyping tool, but it may work for non-cosmetic components and the unit cost will be especially economical for quantities in the low hundreds.
Aluminum tool life is usually around 1,000 units. Above 1,000 units, you’ll need steel tools with automatic sliders to reduce cycle time.
Many injection molding manufacturers will make a family mold for small parts that are produced in relatively low quantities. This means that more than one component will be cast together in one mold, which saves on tool base material cost and cycle time per component. To leverage this, use the same material for as many components as possible in your design.
The Case for Low Volume Production at Higher Per-Unit Costs
A brief word of caution: a lot of hardware startups start their MVP run at 10,000 units, but this is quite dangerous without committed pre-orders. Selling a few hundred units is quite easy, but selling a few thousand is surprisingly hard. Although the unit cost for 1,000 might be higher than 10,000 units, there is an argument for shipping fewer units and iterating quickly.
There’s a Lot to Know — We’re Here to Help
There could be an entire book devoted to this topic, with a sequel just for assembly processes! The choices are vast and the considerations are many, so know that you can always contact our team to help you make the best decision for your project needs. Just shoot us an email at inquiry.mf@chinamanufacturingparts.com or give us a call at +86-755-27092530.