Time to read: 6 min
We’re taking a look at two lower resolution and cheaper 3D printing materials for prototyping: ABS and PLA. When will PLA suffice? When do you gain much more by going with ABS?
A lot of people look at price and automatically choose to print in PLA because hey, it’s the cheapest material! But depending on your design, sometimes PLA isn’t the best option. If you have overhangs, complex geometries involving support, or are more concerned about surface finish, ABS is often the better choice, while still being cost-conscious. It’s worth spending a bit more to have a useful prototype than to cut costs and have an unsuitable—or sometimes even failed—part!
We’ll go over the design features to look out for when picking your material, to make sure you get the most value out of your design and material choice in early-stage product development.
Key Differences
Both PLA and ABS use FDM technology for printing, but the key difference comes from the quality of the printers and how parts are produced using each material. While the achievable specs of the materials are the same, the consistency and quality of ABS is better because of the professional machines used.
Support Material
PLA is printed using a breakaway support, a rigid material that is the same as the PLA filament itself. This support is removed by hand (via pliers), meaning that the surface in contact with the support structure is rougher.
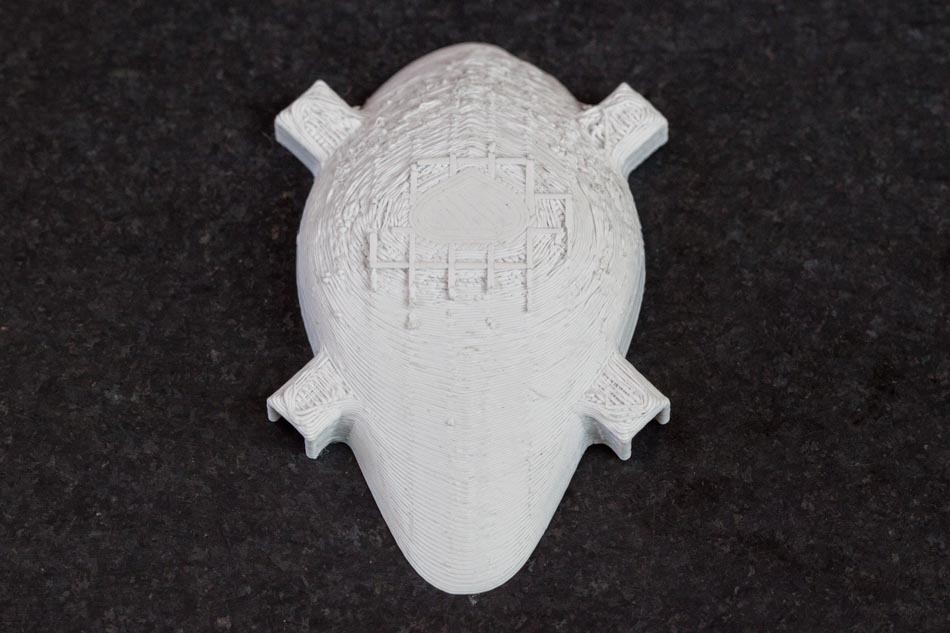
Because the support is broken off, for intricate or fragile features, there is a likely chance that removing support would break the part features.
In some cases, PLA is printed without support at all, in order to get a smoother surface or to avoid the breaking of certain components. The tradeoff is that overhang features are more prone to sagging. If you’re considering PLA, check out our Design Guidelines for Prototyping with PLA for a more in-depth look.
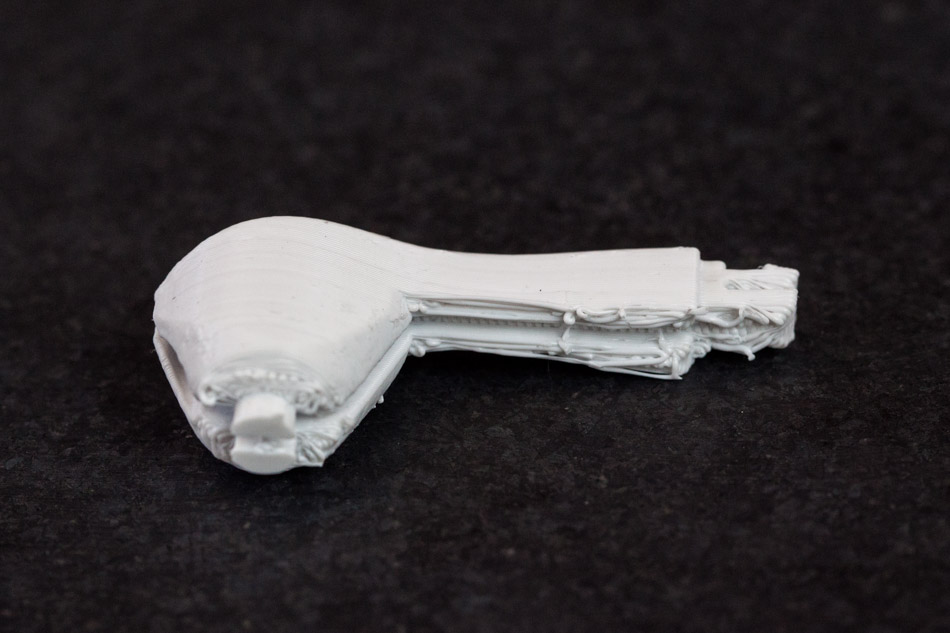
If you do have a simple shape with a flat base, flat surfaces, and no overhangs, like a box, or even a simple upright cylinder, PLA often ends up looking just as good as ABS, and it’s more cost-effective. In such cases, you don’t lose much at all by choosing PLA over ABS.
ABS uses a soluble support system. Support is removed via immersion in a bath, followed by drying of the part. As long as every feature has a clearing for the support to be removed, and there are no enclosed channels, support is removed very cleanly.
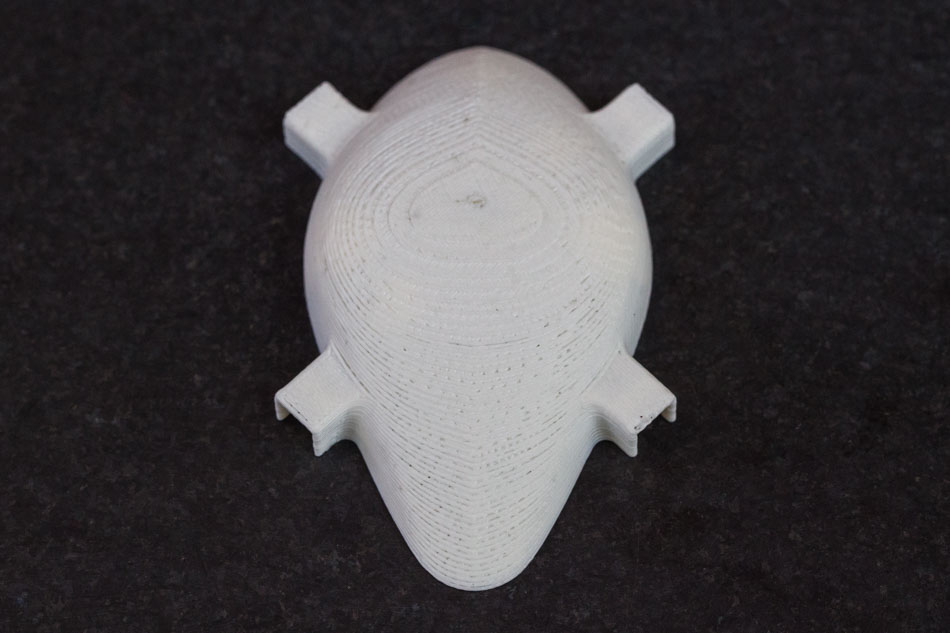
Therefore, ABS is great with more delicate and/or complex features and is the better material for parts that have overhangs or require a higher-quality surface finish.
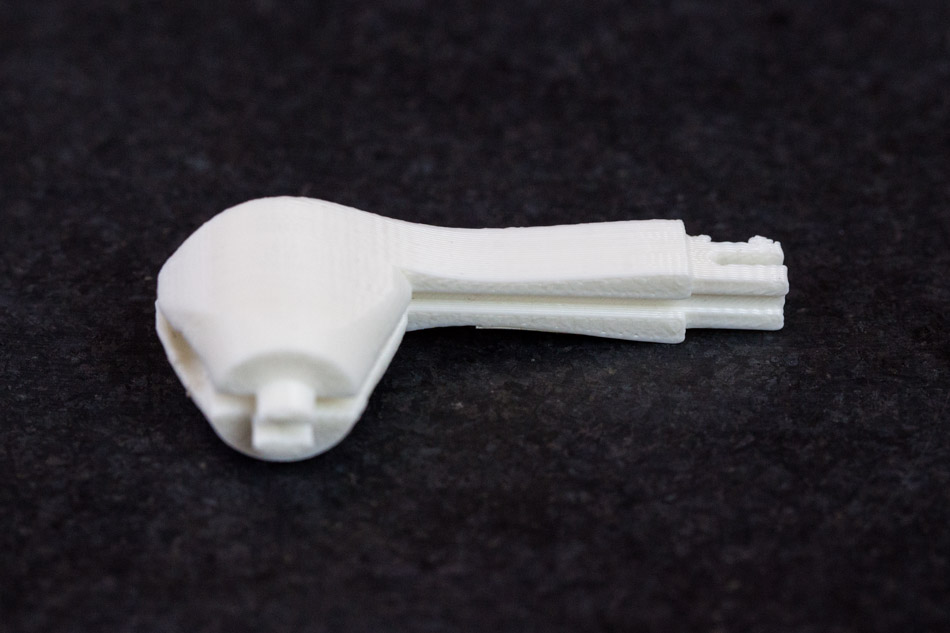
Consistency
PLA is printed in open-air conditions, so it’s more vulnerable to temperature fluctuations that affect cooling conditions. Since conditions are not as strictly controlled, tolerances have greater variation. The way the resin cools has a significant impact on how consistent the part is to the digital design, so beware when your part requires very precise dimensions!
It’s also good to be aware of consistency between printers and individual prints. Different machines may be used, and there is variation between the filaments themselves. As a result, in terms of color, while two different print jobs may indicate the “same” color, because PLA filament material colors are not standardized, they can appear a slightly different tint. It is harder to match the color exactly between parts printed at different times.
Even when the same brand of machine and same filament are used, open-air conditions mean that print can be affected depending on the time of day. Different room temperatures and humidities may cause different gloss levels. Additionally, since the build bed is not insulated, large PLA parts are more susceptible to warping and/or shrinkage.
ABS is printed in a closed environment and more controlled conditions. This controlled process helps negate the warping and shrinkage that may occur in a PLA print. The quality is significantly better than PLA for complex shapes, and ABS is more dimensionally accurate.
For reference, and if you’re keeping track of value and of costs, note that PLA is printed on ~$3k hobbyist machines, whereas ABS is printed on ~$100k range professional machines. As such, there is much greater reliability and consistency in ABS printing than in PLA, as the quality of the machine is much greater.
Material Properties
PLA is a more brittle and weaker material than ABS. Mechanical features like snap fits, or some that require more detail, like threads, tend to break or not resolve well in the production.
While not as strong, PLA is food-safe and biodegradable, so if you are working with food, consider using PLA for early testing (learn more about food-safe prototyping here).
ABS will have greater strength, so it should be the choice for very early-stage mechanical testing.
Bonding and Assembly
For large parts, PLA can be bonded to other PLA pieces by heat bond. With PLA’s melting temperature around 130℉, the parts can be welded via soldering iron and will have a clean, yet visible, bond line. If printing a part in components and bonding them together, keep in mind that aesthetically, there would be a seam in PLA.
For large parts, ABS can be bonded to other ABS pieces by an acetone weld (simply brushing the surface with acetone and joining two pieces). This chemically bonds two ABS pieces, resulting in not only much greater aesthetic (much less visible seam), but it also preserves the structural properties of the whole piece.
Design Features
So when will PLA suffice? When do you gain much more by going with ABS?
Based on the support material, quality of machine, and property of the material, ABS is best for more complex designs and when you’re asking for more in terms of surface finish, consistency, and strength.
For simple geometries and when precision is not of essence, PLA works very well. In some cases and for certain specific designs, it will look very close to ABS, albeit being less expensive. Here are some quick guidelines to look out for in your design:
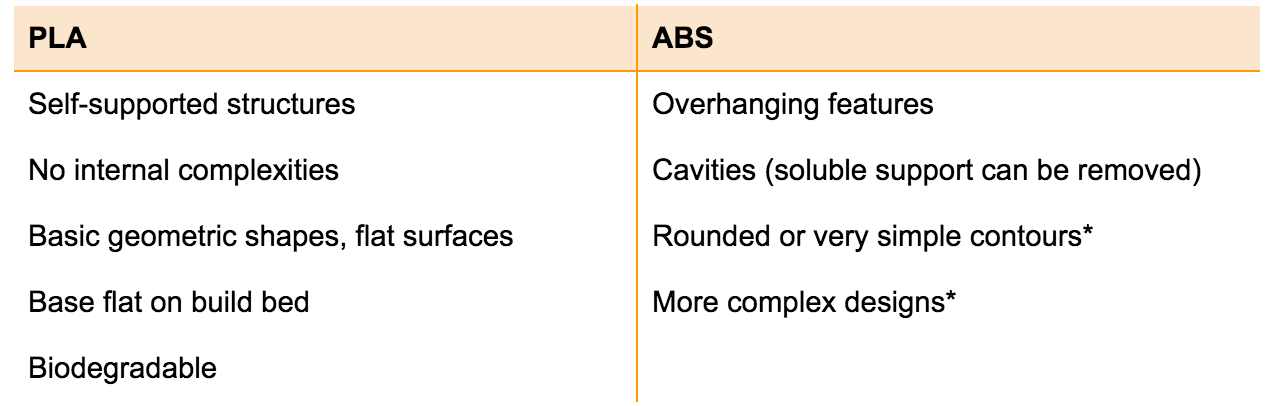
*Note that while ABS is superior to PLA for complex designs and contoured shapes, it will still have visible stepping. For the greatest quality and the best finish for highly complex/intricate designs and organic surfaces, that’s where you want to step up to a PolyJet printer!
Side by Side
Since pictures are worth a thousand words, here is a comparison of the two materials used to print components of a drone.
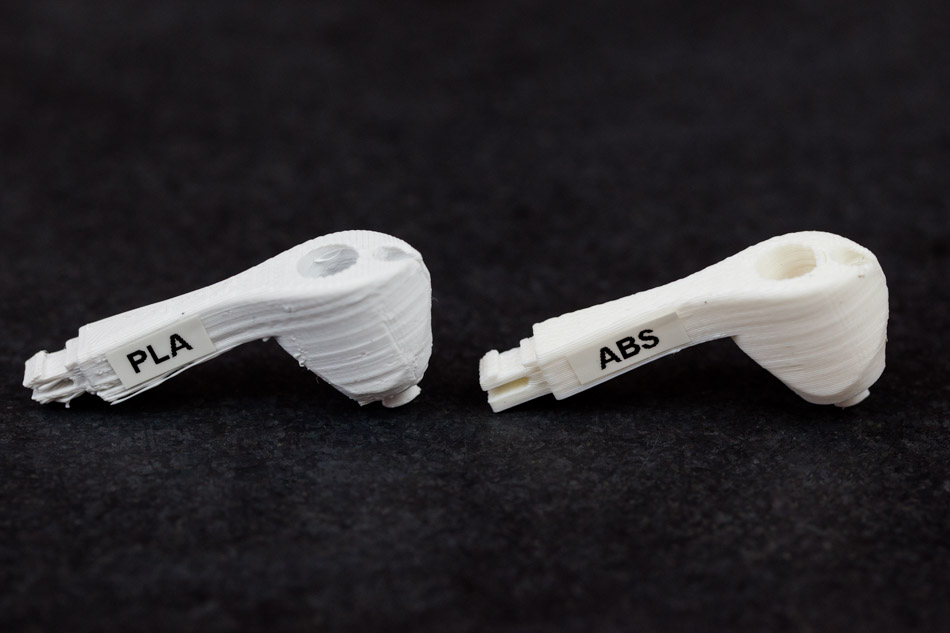

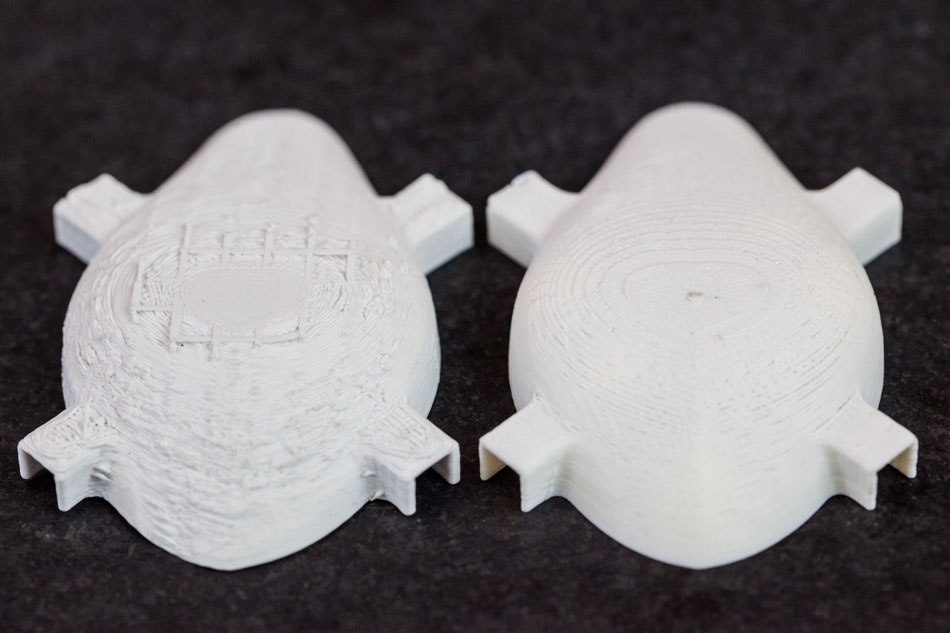
Prototyping Considerations
If you’re in the prototyping cycle, here are some other practical and logistical considerations for how to choose materials. Keep these in the back of your mind when you’re working to hit deadlines or need to present parts to investors or involved parties!
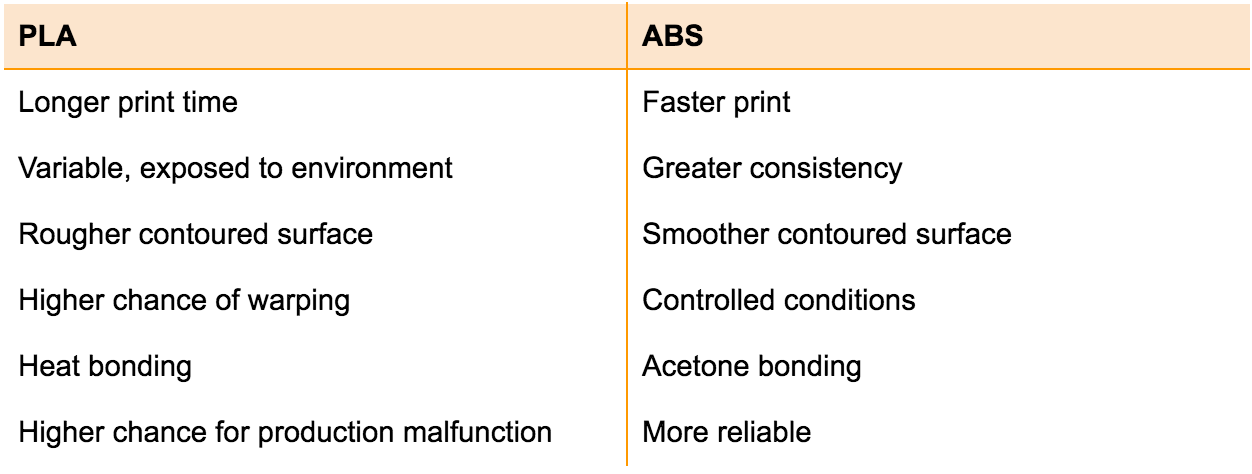
Takeaway
As long as you know what to expect from PLA, it’s a great prototyping material! Use it for rough prototyping and when you need to flesh out a concept quickly and cheaply.
When you require greater consistency, have complex features, and are still in the early prototyping stage, ABS is the way to go. ABS is also advantageous in that these prints, by virtue of machine quality and controlled conditions, are much less susceptible to production failures than PLA.
Just make sure that whatever material you go with, it will give you the most value. If PLA isn’t well suited, even though it’s cheaper, you won’t gain very much from your prototype. Better to have something that works well than to cut costs on something that does not work at all!
It’s important to prototype quickly, so you can fail early and fail often. That’s where these lower-resolution materials shine! As parting advice, just be sure that you learn something from every prototype, and that the material selection will allow you to learn, rather than impeding your learnings by compromising parts of your design.
As long as you do, you’ll be on your way to cruising (well, really grinding, since it’s a gritty and often involved process) through the product development lifecycle!