Time to read: 4 min
Computer Numerical Control (or CNC) machining combines the efficiency of computer programming with the accuracy of lathe machines. The programmed software controls the movement of the tools and other machinery, thereby automating the manufacturing process and maintaining design consistency.
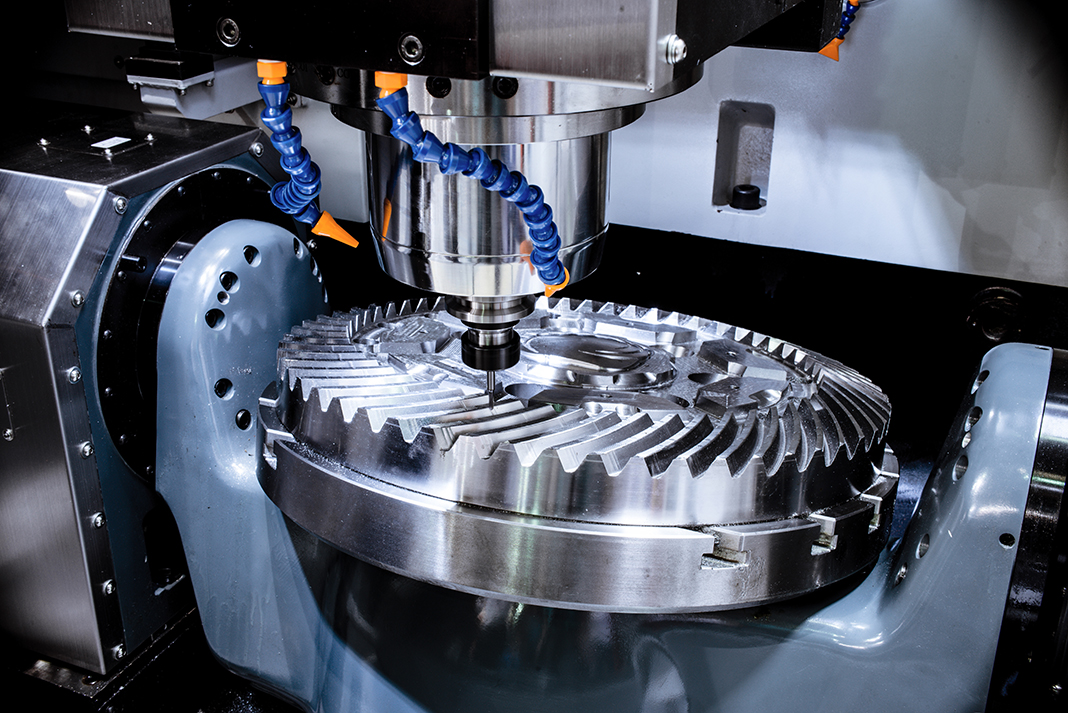
Modern-day multi-axis CNC Milling Machines come with a wide range of features, which adds value and functionality. However, these are only useful when the machine can move seamlessly along its axes. Furthermore, these axes are primarily responsible for maintaining accuracy in shaping the feed. So essentially, they form the life and blood of any milling machine.
Let us examine the functions and capabilities of various multi-axis CNC milling machines.
3-Axis CNC Machining
3-axis CNC machining evolved from rotary filing. Here, the workpiece occupies a stationary position while the cutting tool moves across the X-, Y-, and Z-axes. The X-axis is along with the lathe table, the Y-axis is towards the front/back of the table, and the spindle that drops from the top marks the Z-axis.
It is ideal for simple tasks that do not require intricate detailing or depth. As such, it is one of the most preferred techniques for creating mechanical parts for automation. Additionally, you can also use it for cutting sharp edges, boring, milling slots, tapping, and drilling holes.
Limitations:
3-axis machining possesses the following limitations:
- It functions in a complex programming environment.
- The initial capital investment and the installation costs are high.
- It requires highly skilled professionals for operating and maintaining the machine.
4-Axis CNC Machining
The 4-axis CNC functions pretty much like its 3-axis counterpart. The feed is in a stationary position, and the cutting tool works on it to remove the excess and mold the desired part.
However, as the name indicates, 4-axis machining involves an additional axis apart from the usual X, Y, and Z planes. This extra movement is present in the form of rotation along the X-axis, which forms the fourth plane – the A-axis (horizontally). However, the cutting may also take place along the B-axis (vertically). But since Horizontal Machining is considered more productive than Vertical Machining, the former is more common.
This milling technique is useful for cutting holes, cutting along an arc, or carving cutouts, especially on the sides or around a cylinder. It is also useful for high-quality precision engravings, millings, and drillings.
Limitations:
The greatest limitation of the 4-axis milling machine is its Geneva Mechanism. While the Geneva Mechanism is quite common for its simplicity, reliability, and precision, it allows the 4th axis only in principle. However, it does not support continuous machining in practicality as it possesses a fixed set of stops. Hence, the operators can only use the machine as a pure indexer. Other drawbacks include:
- Quick wear and tear of the worm gear mechanism, especially during high-intensity use.
- The issue of backlash can affect your accuracy or the durability of the machine.
5-Axis CNC Machining
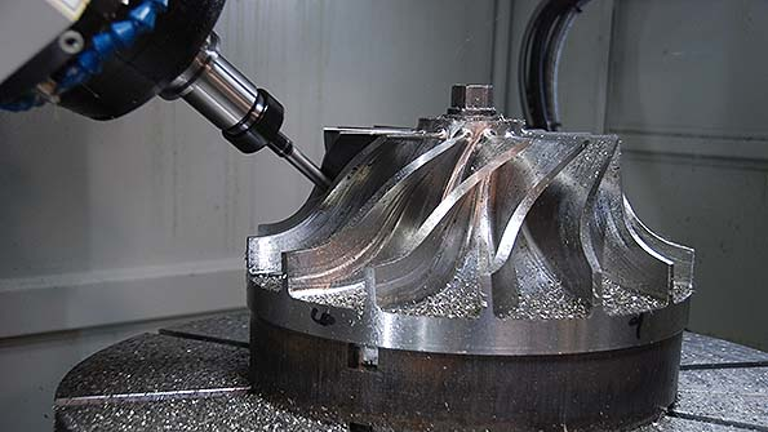
The 5-axis CNC milling machine marks the pinnacle of innovation in 21st-century machining. It bears greater competency than its 3- and 4-axis milling machines and is a precise, fast working, micromachining powerhouse.
In this setup, the X, Y, and Z-axes are similar to a 3-axis machine layout. The table then rotates along the A-axis, as it does with the 4-axis. However, the 5-axis machine involves the pivoting action at the joint of the table, followed by rotation along the C-axis, which defines the fifth movement.
5-axis machining allows the operator to simultaneously hit five different sides (or more!) of a part depending on the design complexities. Resultantly, the tool is highly capable of creating highly precise products and parts. Hence, it should come as no surprise that it finds wide usage in medical technology, research and development, architecture, military, automotive industry, and even creative arts. It also finds use in hole drilling at compound angles.
Limitations:
While the 5-axis CNC machine is excellent in terms of speed and accuracy, it ails with the following issues:
- The CAD/CAM programming for 5-axis machines can be extremely complicated, especially while envisioning the spatial trajectory.
- Since 5-axis milling machines are not that common yet, purchasing and maintaining one is quite a hefty investment. Similarly, the tooling solutions are equally expensive.
- You would require a highly skilled CNC machine operator that you can trust with your 5-axis beauty.
7-Axis CNC Machining
The 7-axis CNC milling machine can create long, slender, and heavily detailed parts. The 7-axes involved are the usual right-left, top-down, back-front, followed by the axes defined by the spinning of the tool, rotation of the part, rotation of the tool head, and movement for clamping, reclamping, or removing the part. This high degree of movement imparts greater accuracy to the finished product without the need for post-fabrication processes.
9-Axis CNC Machining
The 9-axis CNC blends lathe and 5-axis machining. As a result, the part can be turned and milled along various planes in a single setup, thereby offering sharp accuracy. One of the greatest advantages of a 9-axis CNC is the elimination of secondary fixtures and manual loading. The 9-axis CNC is highly capable to the point where it can complete an entire fully-finished product in a single operation!
12-Axis CNC Machining
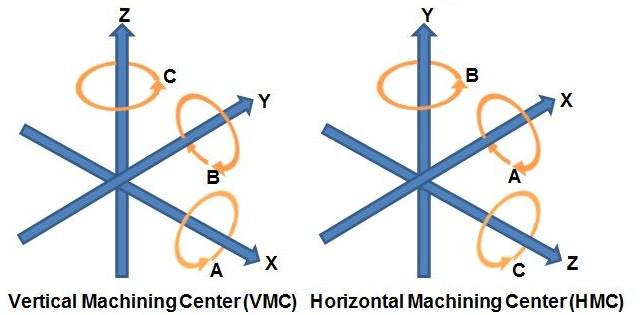
If 9-axis CNC machining is the whole package, then its 12-axis counterpart is an absolute beast! The 12-axis CNC machines typically contain two heads that allow movement along the X, Y, Z, A, B, and C-axes. This configuration doubles the productivity and accuracy while cutting down manufacturing time by half!
Final Thoughts
CNC machining continues to stay relevant and effective to this day. It serves various manufacturing-intensive sectors and maintains product quality, precision, and standardization. As machines acquire more axes of movement, they are only bound to get better with each iteration. So while they may be a significant investment, they also promise long-lasting service in return!