Time to read: 5 min
Depending on the intended use case for your 3D printed part, structural integrity can be a crucial ingredient. It could be a matter of ensuring that your product doesn’t collapse when used or even a matter of ensuring user safety. The world in 2022 seeing a vastly accelerated need for 3D printed parts in mult-disciplinary industries, such as aerospace, medical, automotive, and even in-home personal use. Choosing the optimal 3D print design tips for layer direction, design and material for your 3D printed parts can ensure the best structural quality for your product.
We’re going to look at an artistic, yet functional Wacom pen holder as an example and ascertain the different considerations and precautions utilized to ensure structural integrity in the 3D print.
For those of you using your own 3D printer, this will help you understand the best settings to use. If you’re ordering 3D print parts online, this will give you a better understanding of the different technologies and materials available for durable 3D print parts and what to communicate to your vendor.
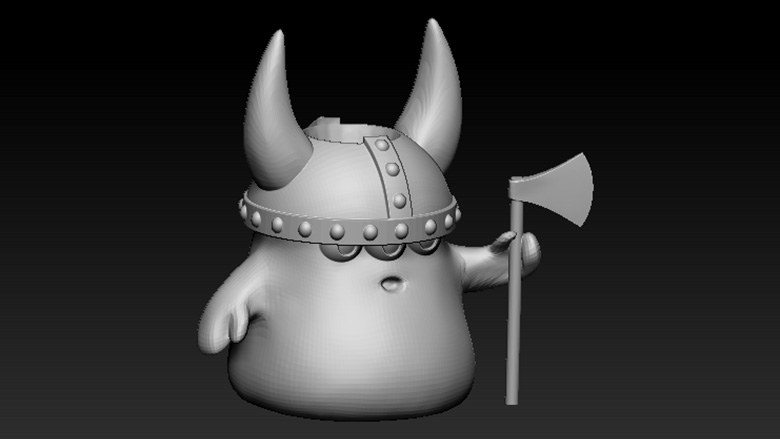
For this product, an artist’s Wacom pen or writing instrument will be inserted into the pen hole, applying a force as shown in the image below. The force is relatively small and applied in the same direction as the force due to gravity on the pen or writing instrument is applied.
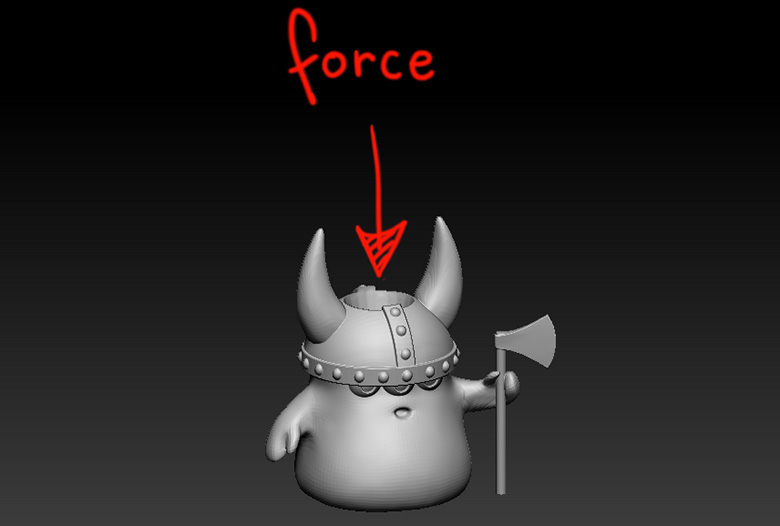
What can we do to make sure this penholder has a long lifespan? There are a few design optimization methods to utilize to ensure durability and the most effective material usage. Read on to learn our top three tips.
1. Layer Direction
One of the biggest considerations for the durability of your 3D printed parts is the direction of the 3D printed layers. If possible, you want to reduce the potential for a failure due to a shear force since you want your vertical force to distribute amongst the layers at a direction perpendicular to the layers. Therefore, it makes sense for your layers to be printed horizontally. Alternatively, if the force on your 3D printed structure is coming in from the side, underneath, or at any angle other than straight down, we will get an effect called shearing amongst the horizontal layers.
Most engineers are already familiar with the term shearing, but for the designers, think of this as a deck of cards; they won’t slide apart if you press down on them from the top, but if you push them from the side, the deck will fall apart because the layers slip apart easily. The same concept can be applied to 3D printed part: the cards are like the 3D printed layers that make up a solid object with more force applied to it.
If you’re working with a 3D printing vendor, the main takeaway here is to make sure you explain the intended use of your part so the operator can choose the best build orientation.
2. Density
Another element that will guarantee better structural integrity is your 3D printing material density. In the software of every FDM printer, there is usually a Fill Density option; the software for these printers automatically knows to print a pattern of filament inside your model.
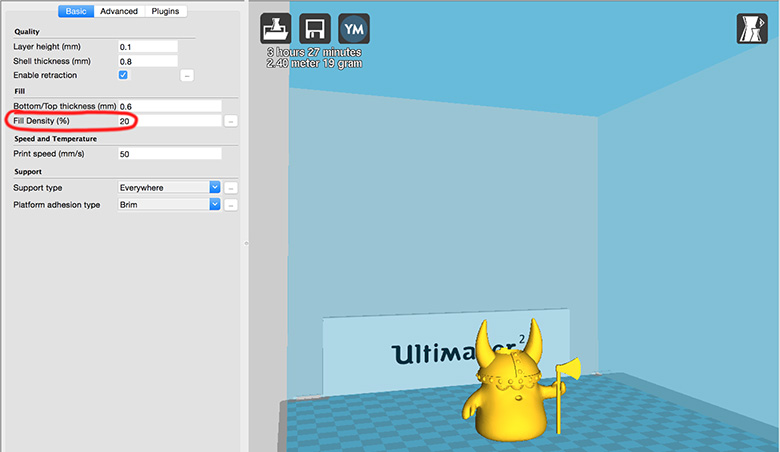
At the default setting of 20%, your Fill Density will fill up your model with a nice light amount of filament. This is designed to provide stability while also reducing printing time and material costs. However, if structural integrity is a critical feature of your project, the Fill Density percentage can be increased.
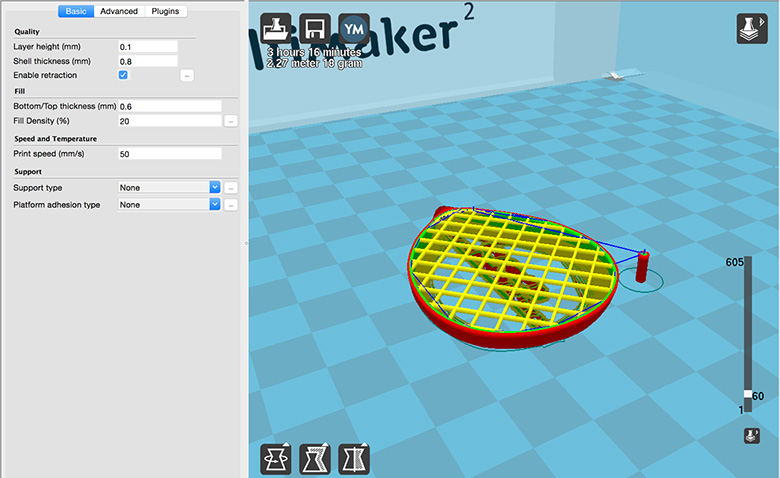
By simply increasing the Fill Density by an extra 10%, you can see the Viking Wacom Penholder will be printed as a much more solid and slightly heavier object:
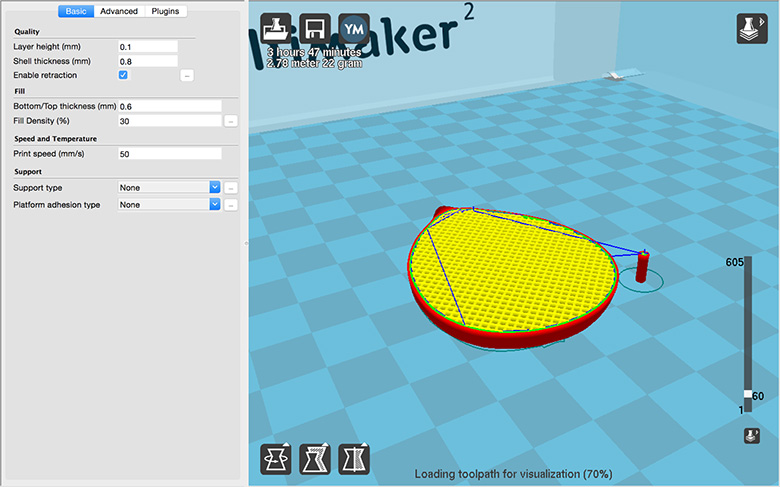
If we jump over to an SLA printer such as the Form 1 +, these printers automatically fill all geometry with resin. Many people “hollow out” their models before printing to save time and material cost, but since we’re looking to increase structural integrity, filling the entire geometry with resin is a great option.
If you do decide to hollow out your model, 3mm minimum wall thickness in VeroWhite is a good place to start. Go from there to determine the best wall thickness for your application.
3. Material Choice
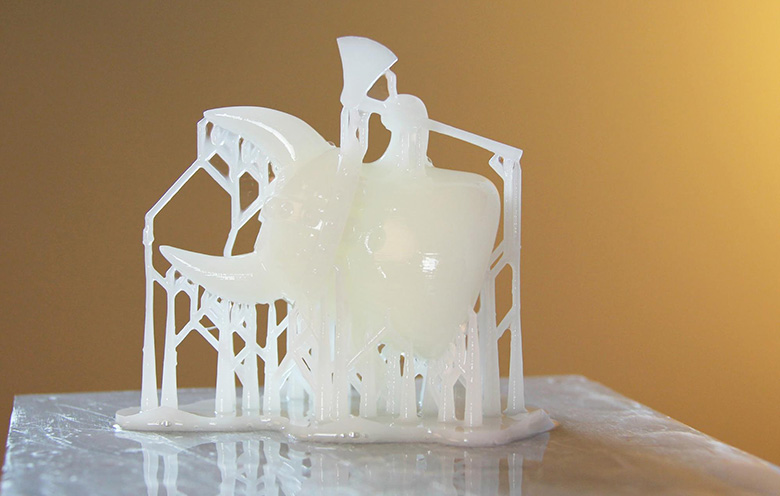
Another one of the most important considerations for structurally sound 3D printed parts is choosing the strongest 3D printing material for your application. Here are 3 great options for durable 3D printing mechanical parts:
- ABS – great for parts that need to have strength, but won’t receive heavy use. The variability in the filament diameter also causes concerns for overall part shape, precision and deformation during cooling.
- ABS-Like – more expensive than ABS, but great for 3D print parts that will receive heavy use.
- Nylon – most expensive material, but works great for 3D print parts that will receive heavy use and need to be high-resolution (i.e. visual models).
- PLA – marketed a recyclable alternative that is less susceptible to warping during cooling. But the material starts to break down at relatively lower temperatures.
- PTEG – a widely utilized thermoplastic 3D printing filament which has excellent strength, impact resistance, transparency, and stability.
Your material selection should also take into consideration the moisture content of the plastic filament. Depending on the 3D printing bulk material you chose, they can either be hydroscopic (moisture loving) or non-hygroscopic (moisture resistance). Any presence of moisture in these bulk materials can cause your final product to be brittle or structurally weaker than its 3D printing mechanical parts design.
If you want to use 3D printing materials other than plastic resins or are looking to produce more than 1 or a few products, you can consider other fabrication technologies including:
- Direct Metal Laser Sintering
- Multi Jet Fusion
- CNC Machining
- Electron Beam Melting
Follow the tips in this article to ensure your 3D printed parts perform to the best of their ability.
Here’s what the final pen holder design looks like molded and cast out of metal:
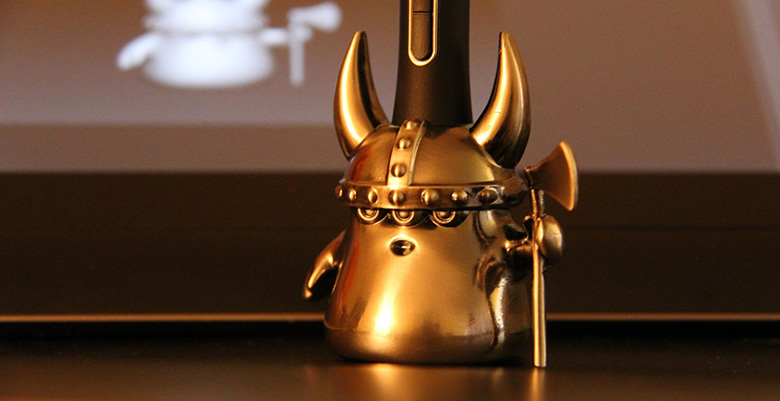
Quick FAQS:
- 3D printed parts are as strong as their weakest layer due to their additive manufacturing method. A 3D printed part is typically weaker than a part manufacutred utilizing another technology, such as milling, molding, or resin pouring.
- 3D printed parts offer a great durability for their manufacturing method and modifiable geometry.
- Polycarbonate is the strongest 3D printer filament by many manufacturers.
- As described in this article, strength of 3D printed parts is impacted by layer direction, density, and filament material selection.