Time to read: 6 min
Corrosion is a common phenomenon—where there’s metal, there will be rust. In scientific terms, corrosion is a chemical process in which refined metals get converted to their more chemically stable form.
Four basic ingredients found in your home environment cause corrosion: reactive metal, air, moisture, and electrolytes. And while a quick spray of WD-40 battles corrosion, from sticky keyholes to stuck hinges, to truly avoid corrosion, we need to start from the design.
Knowing the causes of corrosion make it easier to design against it. This article explores strategies for increasing metal corrosion resistance. One note: There are a few unconventional types of corrosion relating to microbial activities on polymer, which we won’t address in this post.
Passive Coating keeps out water and salt
Bicycles are a great example of how you can design a corrosion-resistant product. Typically made of steel, aluminum, and carbon fiber, bicycles are also regularly exposed to the elements. Rain + road dust = water + electrolytes = corrosion. Adding a physical barrier to prevent direct contact with the external environment helps to keep corrosion in check; options include painting, powder coating, vinyl wrapping, anodizing, and even waxing. These methods, referred to as passive coating, serve to keep water and salt out, preventing corrosion, and it’s important to plan for them when designing products that you know will spend time outside in the elements.
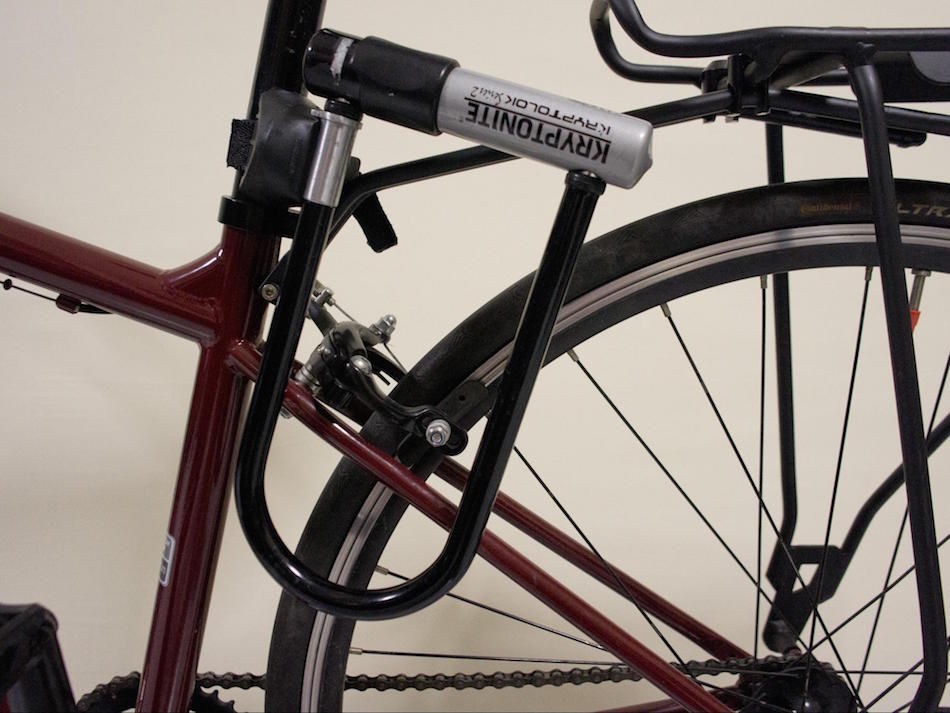
Painting
You can plan to make your design corrosion resistant by factoring in the need for passive coating, which is what bicycle manufacturers use to improve corrosion resistance. Bicycle frames are painted to form a barrier layer—painting on a clean, dry surface means moisture can’t get trapped beneath the coat.
Powder coating
if you’re designing a product like bike racks, many of which are made of aluminium, you’ll want to plan to have the product powder coated, to avoid the pitting that can result when aluminum is scratched and in contact with water. Powder coating is done by spraying a layer of dry powder (thermoplastic or thermoset plastic polymer) electrostatically.
In powder coating, the powder coat gun has a positive charge, while the workpiece is grounded. This electrical difference drives the tiny particles towards the workpiece, kind of like the hair-rising balloon experiment you may have done in school. This ensures even coating, which is followed by a curing session.
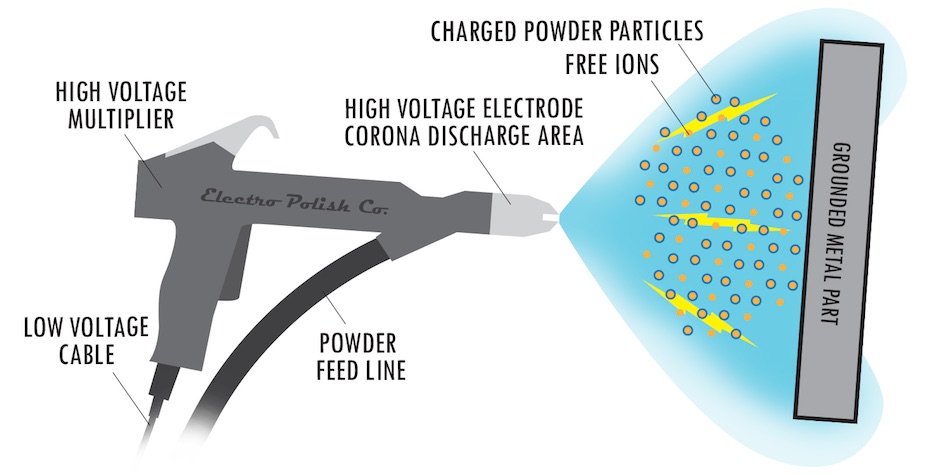
Vinyl wrapping
You count on your U-lock for security, and you don’t want it to get corroded, so most U-lock manufacturers wrap the locks in vinyl to protect them from the elements—and as a designer, you’ll want to plan for this. Vinyl wrapping is like shrink wrapping; heat is applied once the U-lock has been sleeved with the vinyl (see the black, U-shaped tubing in the image below).
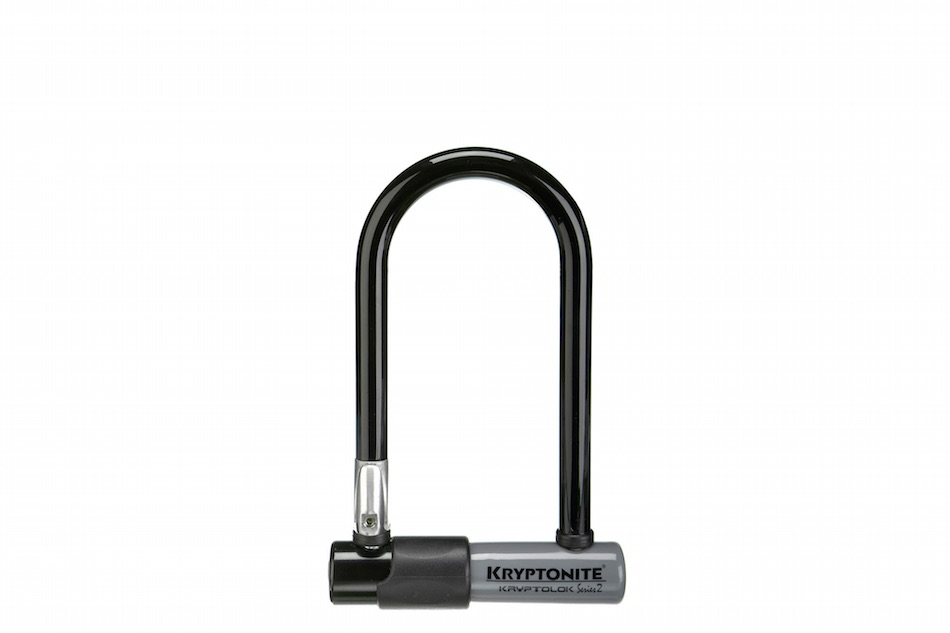
Anodizing
Stainless steel and cnc machining aluminum have the inherent capability to form a layer of protective oxide. However, in the natural form, this layer of oxide is only about 4nm thick. Anodizing the metal is a way to provide extra corrosion and wear protection, so be sure to add that to your plans for steel and aluminum products.
In some cases, anodizing is used as a decorative element, allowing designers to add different shades of color. Apple does this with their different colored devices: Space Gray, Rose Gold, and Gold.
Anodization is done through by placing the workpiece in a dilute solution. The workpiece is being connected to an electrical circuit where it is an anode. The positive oxygen ions will be attracted to the workpiece, creating more oxide layer on the workpiece.
Active Coating provides a strong physical barrier
Galvanizing
When you’re designing products to be corrosion resistant, you may want to to keep in mind that galvanizing provides a stronger physical barrier than passive coating does, by forming a chemical bond with the physical substrate of the material, instead of just coating the surface. This chemical bond is much stronger than what passive coating can offer, with a bond strength of 3000psi. Best of all, it has dual action—it makes the base metal cathodic by attaching a more reactive metal onto the surface. The thin layer of coating will rust first, instead of the base metal.
Galvanizing is best done after all secondary processes have been completed, since any new cut will expose fresh metal, allowing rust to form. Besides street light posts and steel bridges, galvanizing is commonly done on vehicles and fasteners to ensure corrosion resistance.
Hot-dipped galvanizing is a high volume manufacturing technique. The process is shown below. Each object has to go through caustic cleaning, followed by a few more stages of preparation, before it is dipped into a zinc bath and cooled.
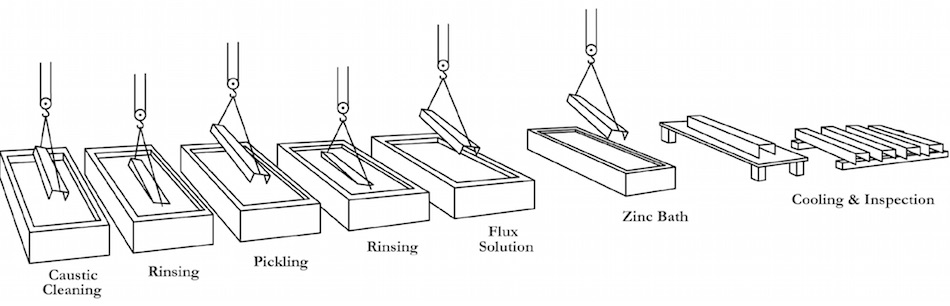
Ensure galvanic compatibility
When you’re designing fasteners, it’s important to ensure that there is galvanic compatibility with the fasteners and the object. On the Galvanic Scale, metal that is more anodic is more prone to corrosion, and when more anodic metal is in contact with a metal that’s lower on the scale, corrosion activity is enhanced. The greater the disparity, the faster the rate of corrosion.
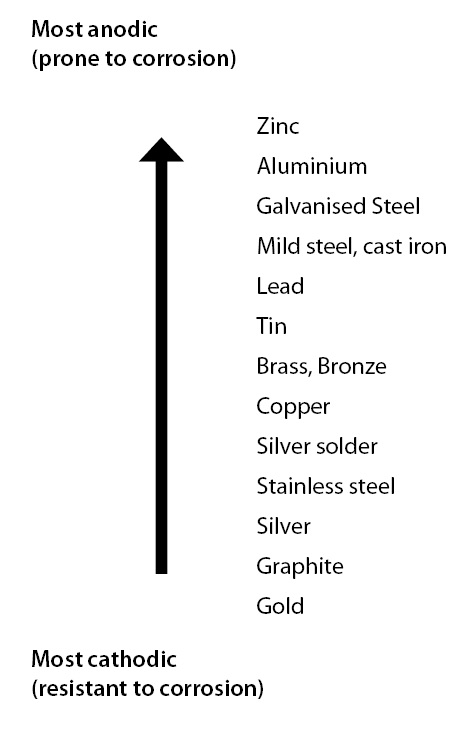
Therefore, you don’t want to mix and match coating and metals; if you choose hot-dipped zinc-galvanized material, use fasteners and hardware with the same coatings. Screws and rivets are the most commonly used fastening methods, and the majority of them are made of steel, which happens to be lower on the Galvanic Scale, so you have to be aware of this.
If you start combining different types, there’s a chance the different metals will start their own corrosive reactions—which is exactly what you are trying to prevent. Stainless steel will degrade galvanized steel, so don’t install galvanized sheets with stainless steel screws.
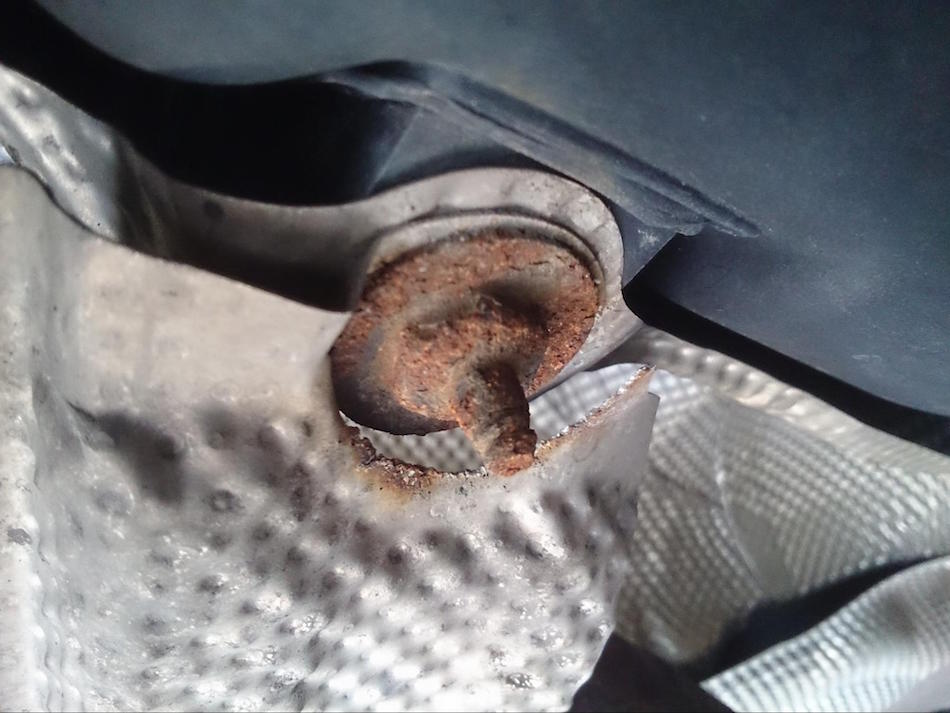
In fact, you can use galvanic incompatibility to your advantage. In the marine industry, sacrificial metals are used to protect ship hulls from corrosion. Pieces of zinc are mounted directly onto the ship hull, below the water line. This works by intentionally allowing the sacrificial zinc to be corroded, instead of the steel ship hull.
Replacing metal with plastic
One way to boost corrosion resistance is to plan to replace parts with a suitable inert material, such as plastic. Water pipes used to be made from metal, but have since been replaced with plastic, as have bearings. You may avoid corrosion with plastic, but there are unique issues with plastic, like problems with UV degradation, acid and heat that are important to note, although they won’t be covered here.
Avoid crevices in your design
The graphic below shows how drops of water on the body of a product can result in rust formation. When the surface of a reactive metal gets wet, the oxygen concentration is lower relative to the surrounding. The area around the drop becomes cathode, while the surface below is anodic.
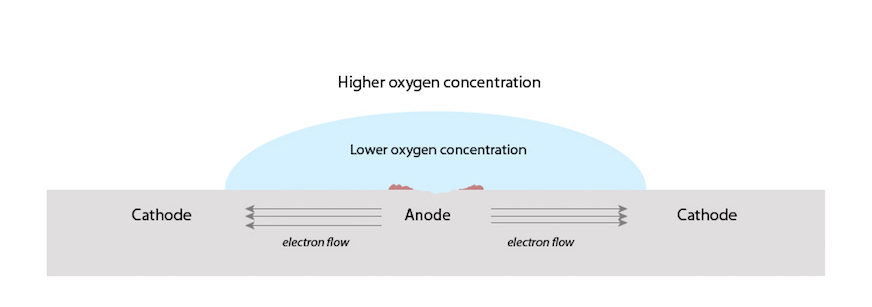
This localization of electrical activity is what causes spots of rust to form on a kitchen basin, which gets worse with a lower grade of stainless steel. You can design against this form of corrosion by removing traps to ensure that there is uniform oxygen concentration around the bodywork.
We can learn from the construction industry, which does crevice corrosion prevention best. Rules like allowing water and dust to flow freely but not get trapped onto the surface are helpful. Designs are simplified to reduce the number of crevices, and if crevices cannot be avoided, weather-sealing can help counter corrosion.
In other words, reducing the number of joint parts, coating, and sealing can help avoid crevice corrosion.
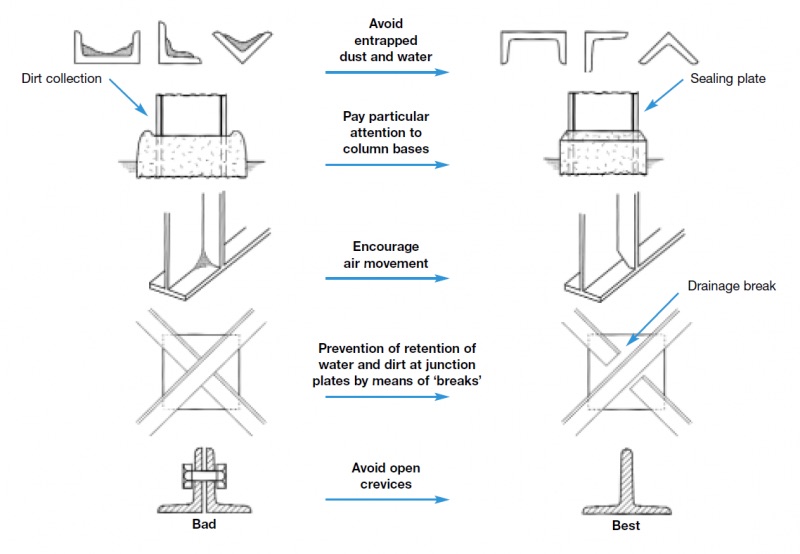
Main Takeaways
It’s important to understand what causes corrosion and to use strategies for increasing metal corrosion resistance in your product design process. Incorporate plans for coatings, vinyl wrapping, and galvanizing into your product design process when working with metals, and avoid crevices in your design. You can check out China Manufacturing parts’s Capabilities Guide for more information about materials. As in all hardware development, always be thorough with your testing procedure, and check back on the usage behavior and the operating environment. Being able to understand what your product will experience in the environment is half the battle won.