Time to read: 8 min
A robot climbing stairs was barely possible 30 years ago, but now, Honda’s ASIMO robot can not only walk up the stairs of an auditorium stage, it can play the violin. Honda uses ASIMO to showcase innovations in programming, electronics, sensing, and mechanics.
And with its case off, ASIMO reveals craftsmanship in every detail, including the clear wire guides creating highways of information and electricity to animate this amazing robot.
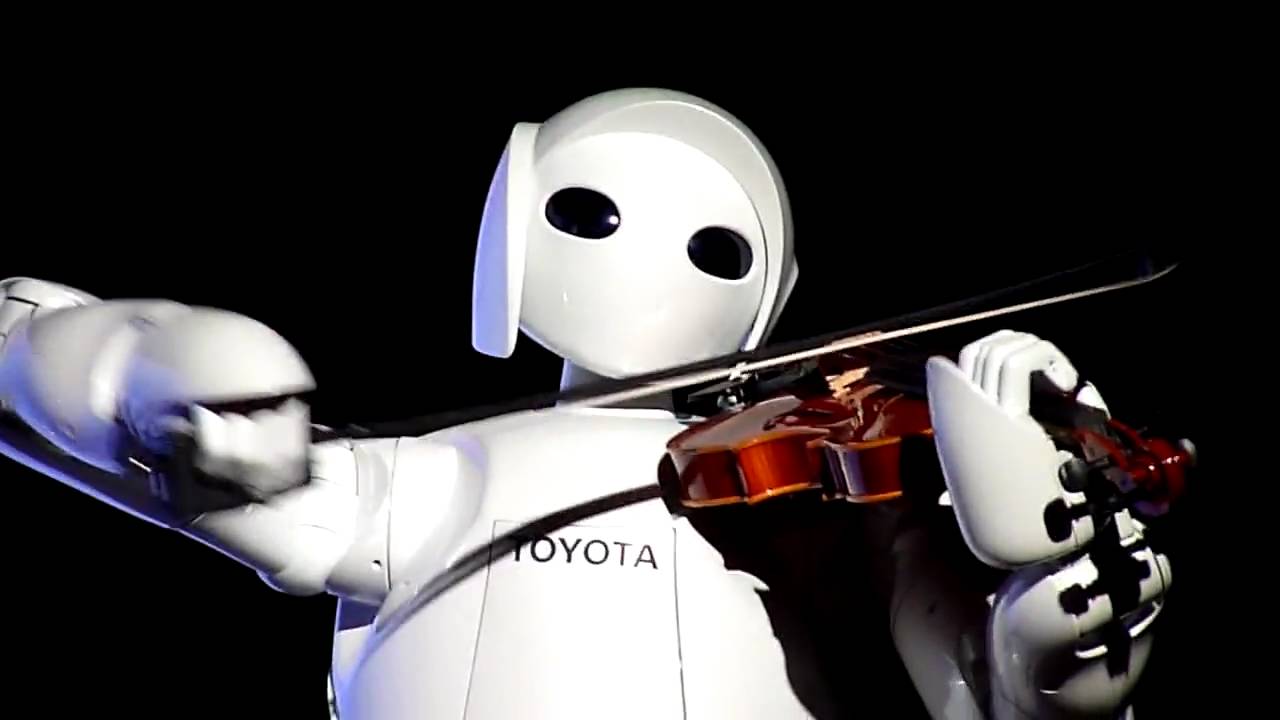
After facing some challenges in my most recent case design, all I can think when I look under the shell is, “How do they manage not to crimp wires with every move?” While you pay attention to the way the case looks on the outside, carefully planning every detail down to the last button stroke, wire guides are the type of thing that gets thrown in at the last minute.
On the inside, you carefully find support for the electronics, worry about ribbing and strength, and focus on the mechanics of the movement. Wire guides are often just there to keep a mess out of the way, not to be a creative or beautiful part of most designs.
And at a minimum, that’s fine, though many designs fail even to do that: Wires make it hard to close the case, can prevent key components from mating, thereby ruining a good design-for-assembly, and sometimes interfere with the internal movement of gears and levers, causing unexpected (and embarrassing!) failures.
Paying attention to clean wire routing and effective guides solves all these problems and can also create unexpected beauty in a design.
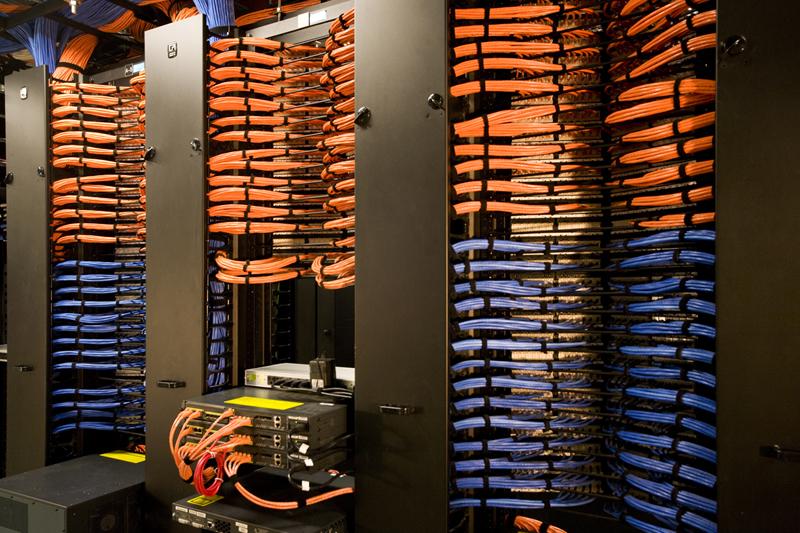
Why Wire Guides?
You need to route the wires through the mechanics—that much is obvious. But how? What are the key concerns? All solutions start with examining the failures.
First and foremost, good wire guides keep electrical wires and data cables away from critical movement components, protecting both electronics and components. A complex robotic arm may move in all six degrees of freedom, extending linear actuators and crown-gear rotors. Often, the wires will need to pass through and around the joints with enough slack for ease of movement.
Allowing sufficient slack at the right points means keeping distance short in others. If the mechanical assembly moves with the wire attached, some difference in length will typically ensue, and your design needs to account for that.
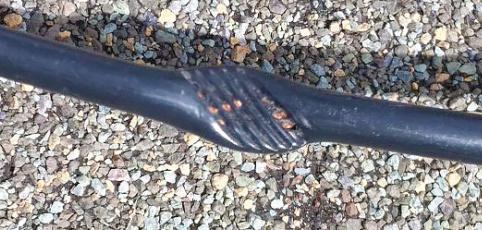
This brings us to the second requirement: strain relief. As the design moves, it’s easy for a wire to be pulled, testing the strength of the electrical connectors or creating sharp bends. Good wire guides will allow slack around the joints, while ensuring that any pull is against a strong mechanical piece, rather than the delicate soldered or crimped connections.
Especially in these days of RoHS-compliant, lead-free solder, joints are brittle and can only withstand very limited strain.
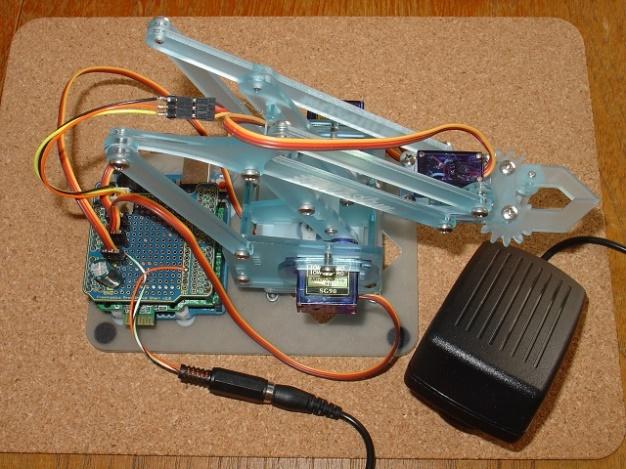
Of course, your design isn’t going to assemble itself (at least, not yet!), so you’ll also need to consider the people putting your case together and the order in which components are assembled. Good wire guides will direct wires and cables away from joints and connectors, allowing for easy one-try assembly between components. If you’ve ever tried your hand at reassembling old radios, you know how frustrating it can be to try to get those components back together with stray wires poking every which way out of the case.
And finally, wire guides can add a certain ordered beauty to a project, like the subtle lines of a French formal garden. Steve Jobs was known for such details, having learned from his father at an early age that details where no one can see them are still important, and he carried that philosophy into each of his products, even having the signatures of each of the original Macintosh team engraved on every case. Beauty can seem like an esoteric requirement, but we’ve all learned how much better everything works when elegance becomes a project goal.
Types of Wire Guides
(not to be confused with “wiry guides,” the compact but amazingly strong Sherpas)
There are many common ways to guide wires, but let’s start with the easiest: off the shelf cable guides.
Cable Guide Clips
Easy to use and cheap, these parts will do the job in a bind, without causing any pinching. For many projects, these guides will provide everything necessary in the case design and only require that you pay attention to the boss for the screw inside the case. However, they may not exactly inspire awe at their beauty, and the additional components add both extra cost and extra time to the assembly.
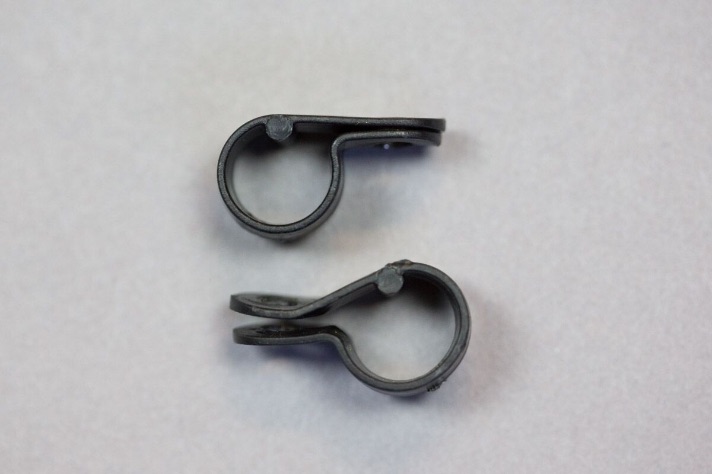
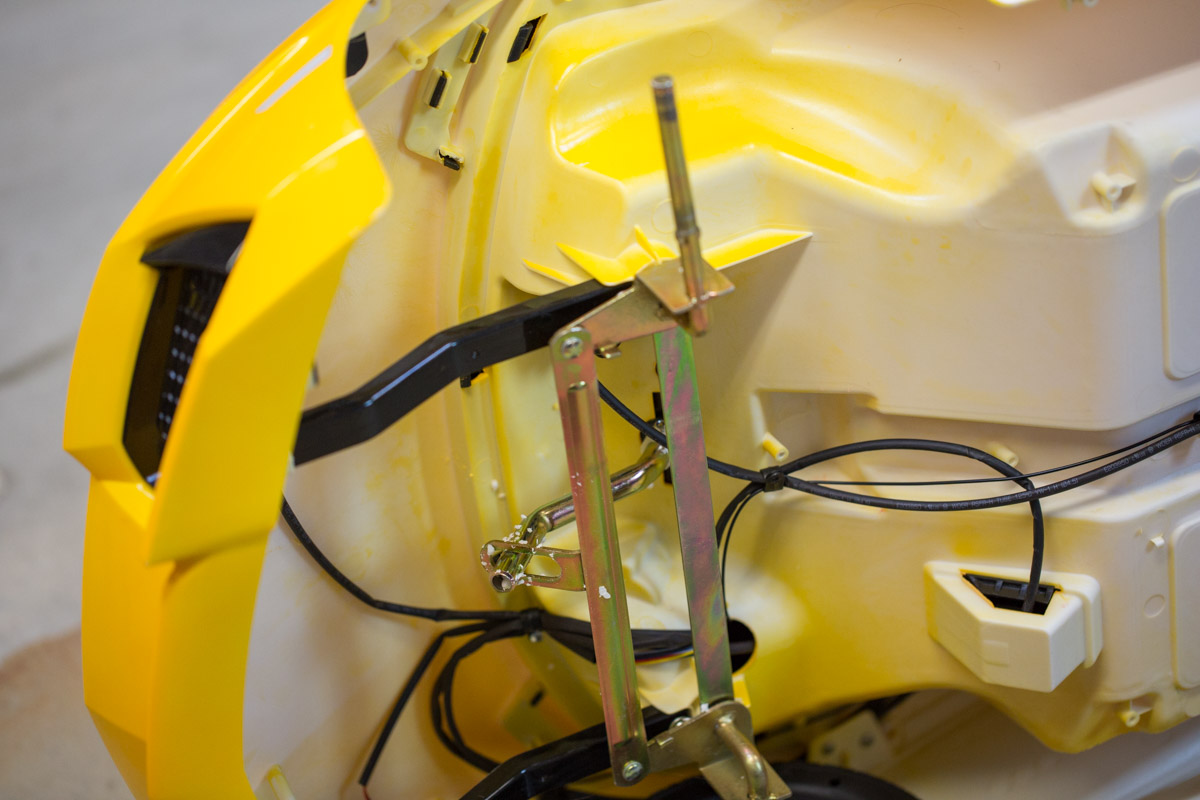
Strain Relief
As mentioned above, with many wire guides, strain relief itself is a major requirement, and it’s a good idea to include a strain-relieving wire guide as the first wire guide point after a connector. The most common type of strain-relief wire guide creates a double bend in the wire, pinching the wire between a post and a horseshoe to create slack at one end, even when there’s tension on the other.
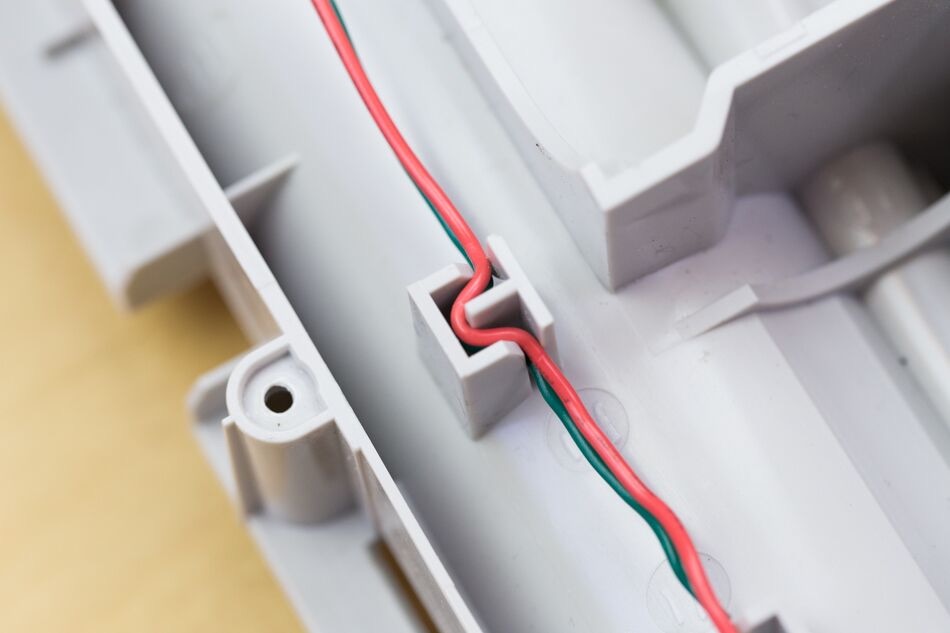
This design requires a balance between a) not bending the wire too tightly, which can create strain on its own and b) creating sufficient friction between the two parts to ensure that the wire won’t slip. While for repeated wire bending you’ll need to limit the bend radius to at least eight times the wire thickness, in a design like this, where the wire will only be bent once, a minimum bend radius of the wire diameter will generally be sufficient.
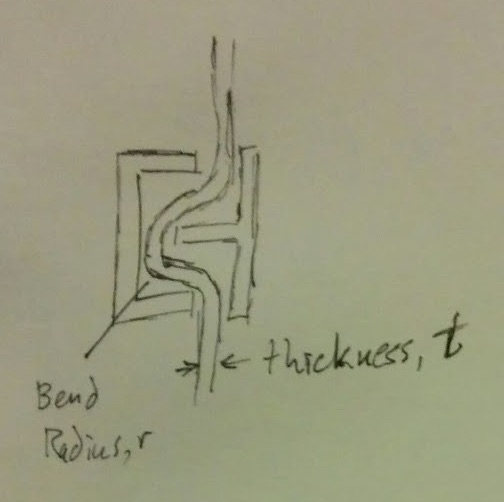
The second critical part of this design is creating sufficient friction to keep the wire in position. Formulas are simple but always require complex interaction between materials—the rule, of course, is that the tighter the bends in the wire, the more force it can handle without slipping. Since this is directly against minimizing strain, it’s good to go with the minimum bend radius (one wire thickness) in your design, where possible.
Thermoplastic Secured Wire Guides
For situations in which the wires will be kept in place indefinitely and must stay secure (like, say, when a bunch of ten-year-olds are running the final product through the back yard in intense mock battles, as with the old LazerTag guns), a heat-formed bond over the top of the wires provides a secure guide, with minimal risk of the wire slipping out.
Of course, your design will need some care to ensure that the guides will melt together without ruining the wires beneath, so adding energy directors—an area of thinned plastic that allows for faster melting—is a good idea.
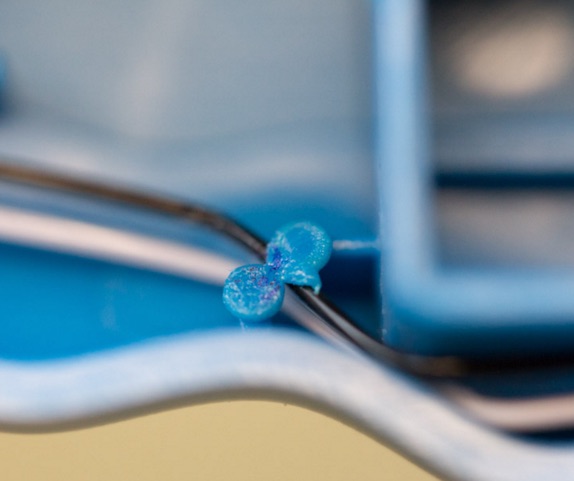
Snap-In Wire Guides
Assembly should be a snap (groan), and snap-in wire guides allow for the easiest assembly of any wire guides. No screws or other hardware, no heating, no careful bending: Just push the wire through, and it remains fixed. Design is simple, too—a snap, you might say (can I get another groan?).
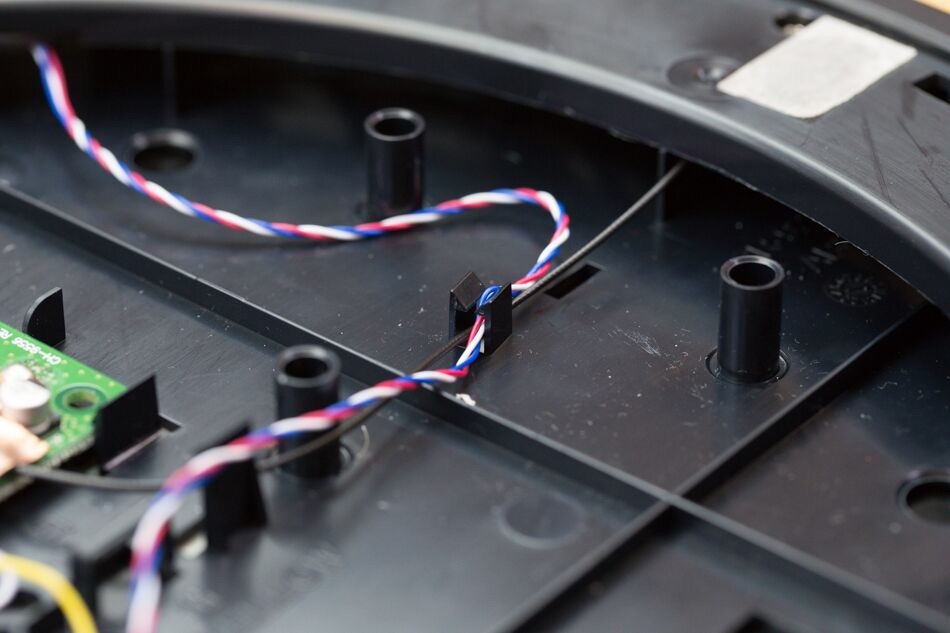
A snap is simply a cantilever beam where the desired deflection is the depth of the snap, and at that deflection, the maximum strain can’t exceed the plastic deformation limit for the material. What?!?! That’s not simple! No, really, it is.
Where:
- ∂_max is the depth of the snap, or maximum deflection
- ε_max is the maximum permissible strain for the material (less than 2% for ABS)
- l is the length of the beam from the base to the snap
- h is the thickness of the beam, and
- 0.67 is a constant for the rectangular geometry
For a wire (or bundle of wires), you’ll just need to plan enough depth to allow for the wire to pass through the two cantilevers (half for each, typically), and your design is essentially done.
Clip Wire Guides
Similar to a snap-in design, clip wire guides will securely hold wires out of the way of your mechanical components and allow for easy assembly. Even better, these designs are great for ribbon cables in designs that require large numbers of individual cables.
As with strain relief guides, take care not to create any crimps in the wire that could compromise the mechanical integrity or electrical conductivity.
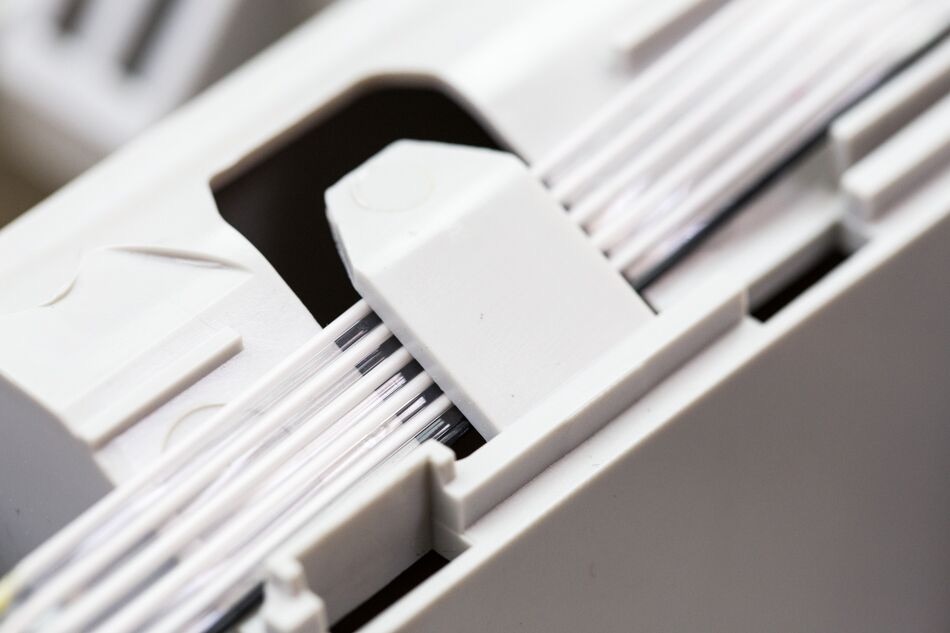
Zip Ties
The ultimate weapon, zip ties, will join cockroaches and Twinkies to outlast us all. Zip ties are a ubiquitous solution and great for prototyping, but use with some caution: Though very strong, they can still break if they come in contact with sharp edges, and if the ends aren’t clipped properly, the pieces can jam in mechanical assemblies, just as easily as the wires they guide. Use sparingly, and preferably only in prototypes.
Final Design Notes
While any one of these designs would be better than providing no wire guides at all, some of them work much better than others when the rubber meets the road, or when the case meets the mechanics. In considering the best type and location of wire guide, ask yourself these questions:
- Is there a way to keep the wires near the core components, so the case pieces can come off without being attached by wires?
- What is the most direct route the wires and cables can take through the assembly?
- What areas of the mechanical design will be especially vulnerable to pinching cables and wires?
- Where can I save the assembler from needing tools to route the cables?
- How can I make the proper cable route obvious to the assembler?
- How can the cable routing add beauty to the machine?
Main Takeaways
Case design details like wire guides can often be seen as inconsequential, hidden parts of grander projects, but the attention to such details is the essence of artistic craftsmanship and can separate out designs that consistently function flawlessly, from assembly through years of use, from those that have you fiddling with the screws to maneuver around stray wires.
Your boss may never allow you to insert your signature into your design, but I certainly wouldn’t mind at least being able to take pride in consistent, smooth function—and even beauty, once the case comes off. If you need some help convincing the rest of your team of the importance of these details, feel free to share this article with them—and tell them it’s what Steve Jobs would do.