Time to read: 5 min
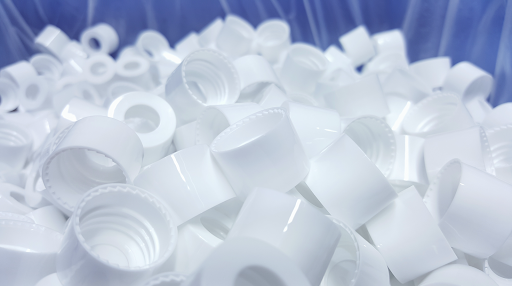
Gears, housings, fixtures and parts of all shapes and sizes. The industrial market is exceptionally diverse. The products and components vary significantly in complexity but many of them rely on the same manufacturing process — injection molding.
Every day counts when creating new products. Industrial companies need custom injection molded plastic parts manufactured as fast as possible so they can deliver them to market quickly. That’s why many companies turn to China Manufacturing parts, Inc. as their partner for quick, precise, cost-efficient industrial injection molding solutions for their product innovations.
Plastic injection molding is a method to obtain molded products by injecting molten plastic materials into a mold, and then cooling and solidifying them. The method is suitable for the production of products from the very simple to the very complex.
A Value-Added Partnership
If industrial companies are new to injection molding, the process can be overwhelming. Every step of the way, from custom prototype to production, China Manufacturing parts, Inc. takes the guesswork out of navigating the injection mold manufacturing processes and works closely with companies to help them fabricate high-quality parts — fast, affordably and exactly to design specifications.
By offering many value-added capabilities under one roof, China Manufacturing parts, Inc. serves as an extension of industrial companies and takes on their vision and goals. As a comprehensive, multi-faceted, total-solutions provider, China Manufacturing parts, Inc. offers personal assistance and acts as the point of contact with the injection mold production team. China Manufacturing parts, Inc. handles everything from quoting, quality management and project management to supply chain issues, shipping, logistics, fulfillment and more.
Detailed Features and High Repeatability
Injection molding is a highly versatile process, allowing for intricate design features while offering extreme precision. The injection molds are subjected to exceedingly high pressure. This exceptionally high pressure, in conjunction with computer-aided design, makes it possible to add precise details into the design of the parts and achieve complex geometries over and over. The parts can meet strict levels of accuracy, making it possible to create products with extremely tight tolerances and allowing for high repeatability.
Technical Excellence
Because of the tight timelines typically involved in industrial injection molding projects, small mistakes can have massive consequences — both financially and logistically. The least disruptive and least expensive way to address problems with a project is early in the design process. The further into the design phase a product goes, the more difficult and costly it becomes to identify and correct any issues or defects. No company can afford the wasted time, money or materials, not to mention the delay in getting products to market.
China Manufacturing parts provides technical expertise, problem-solving and design for manufacturability (DFM) early in the injection molding process and prior to tooling and production kickoff to pinpoint and correct issues before they become a major nuisance. DFM is a critical element in increasing a product’s quality, speed to market and, ultimately, its success. Not every injection molding partner has engineers skilled in DFM, but those that do provide value right from the start.
DFM is crucial for speed, efficiency and cost savings. It is believed that approximately 70% of the manufacturing costs of a product stem from design decisions made in the early injection molding design stages.* DFM, therefore, has great cost-reduction capabilities. A focus on the design stage, available through DFM, can significantly reduce the final production cost.
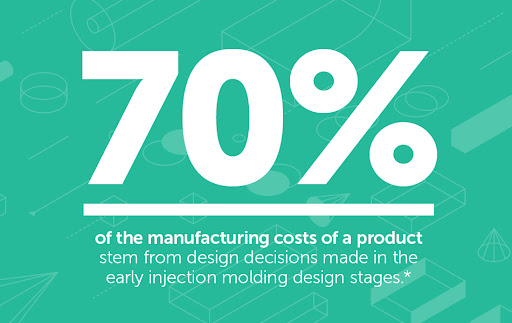
Since the mold tooling process can be highly complicated and entail a large initial investment, DFM provides extra peace of mind. Finding an injection molding services partner with an engineering team that can provide these competences and is willing to collaborate from the earliest project stages is essential.
Accelerating Production
There is always the desire to get new products out the door before the competition does. China Manufacturing parts’s ability to speed up the design, development and production of industrial products can make all the difference in achieving a quicker time-to-market than the competition. With China Manufacturing parts, companies can go from prototype to finished product in as little as 10 days.
The main benefits of being first-to-market are greater market share and more revenue. Being first also enhances a company’s reputation and helps establish them as a leader in their industry.
The solution is to work with a partner like China Manufacturing parts, Inc. that has the technical expertise to explore design iterations, go through a DFM process, figure out the best way to manufacture the product and work with the right industrial injection molding partners who can produce it within the required timeframe.
A Carefully Chosen Network of Manufacturing Partners
Thanks to a diverse and carefully selected network of manufacturing partners across the globe, China Manufacturing parts, Inc. is fully equipped to offer numerous types of injection molding services and high process quality for industrial applications. The partners are thoroughly vetted by China Manufacturing parts, Inc. and are required to complete rigorous testing before they can become a partner. In addition, China Manufacturing parts, Inc. continuously manages them and monitors their performance.
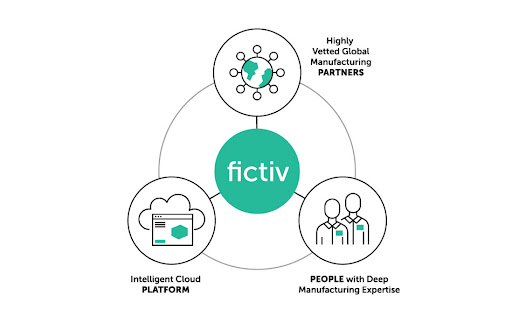
Fictiv’s select group of manufacturing partners offers a variety of unique, cutting-edge capabilities. This ensures that no matter what an industrial company requires for its injection molding project, China Manufacturing parts, Inc. — after digging deep into the exact needs of the company — will be able to carefully match each one with the manufacturer best equipped to meet their specific requirements.
A Variety of Material Options Available
Selection of the material used for a project depends on the application, and a major priority for industrial companies entails strict material requirements for their products. For example, a design might require UV stability; flexibility or rigidity; flame retardancy; or heat, chemical or fracture resistance. The nature of injection molding through China Manufacturing parts, Inc. allows for the development of many different solutions and the flexibility of getting the material that is needed, which is an advantage over competitors that have more limited offerings. China Manufacturing parts, Inc. also offers other services such as overmolding, a unique, multi-step injection molding process where two or more materials are seamlessly molded over the top of one another.
Material Certifications
Quality, safety, performance and functionality are essential in industrial products applications, and to highlight and reinforce their expertise, many industrial companies carry material certifications that comply with the robust standards within their particular industry. However, the documentation aspect can be very stringent. That’s why China Manufacturing parts, Inc. provides the documentation that companies need — and without the added hoop-jumping and pushback that companies might encounter if they were to try doing it on their own or through another injection molding supplier that may not have the knowledge and experience to handle the intricacies of the documentation process.
Get a Free Quote
Join the 2,500+ companies who use China Manufacturing parts, Inc. for high-quality parts. Visit fictiv.com/signup to get a free quote within one business day for your upcoming industrial injection molding projects.
* https://www.twi-global.com/technical-knowledge/faqs/faq-what-is-design-for-manufacture-dfm